-
- News
- Books
Featured Books
- design007 Magazine
Latest Issues
Current IssueAll About That Route
Most designers favor manual routing, but today's interactive autorouters may be changing designers' minds by allowing users more direct control. In this issue, our expert contributors discuss a variety of manual and autorouting strategies.
Creating the Ideal Data Package
Why is it so difficult to create the ideal data package? Many of these simple errors can be alleviated by paying attention to detail—and knowing what issues to look out for. So, this month, our experts weigh in on the best practices for creating the ideal design data package for your design.
Designing Through the Noise
Our experts discuss the constantly evolving world of RF design, including the many tradeoffs, material considerations, and design tips and techniques that designers and design engineers need to know to succeed in this high-frequency realm.
- Articles
- Columns
- Links
- Media kit
||| MENU - design007 Magazine
The Impact of HDI on PCB Power Distribution
December 27, 2017 | Craig Armenti, MentorEstimated reading time: 2 minutes
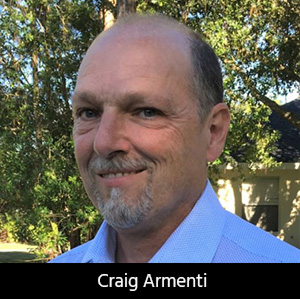
High-density interconnect (HDI) technology is often used to meet the requirements of today’s complex designs. Smaller component pitches, larger ASICs and FPGAs with more I/O, and higher frequencies with shrinking rise-times all require smaller PCB features, driving the need for HDI. Beyond some of the more obvious electrical effects of the microvias used on HDI designs, there is also an impact to the power integrity the PCB. This includes different effects of mounted inductances of decoupling capacitors, changes in plane performance due to reduction in perforation from chip pinouts, and the inherent plane-capacitance changes from using dielectrics of various thicknesses.
HDI Primer
HDI can be a confusing topic, especially for new engineers and designers, or those not well versed in the subject matter. Although this article is not intended to be an in-depth tutorial on HDI technology, a quick review of the key aspects is appropriate.
HDI is a technology that, through a combination of high density attributes, allows for a higher wiring density per unit area as compared to traditional PCB technology. In general, HDI PCBs contain one or more of the following: reduced trace width and spacing, microvias including blind and buried, and sequential lamination.
Current generation HDI designs are typically found in mobile phones, digital cameras, laptops and wearables to name just a few. Basically, whenever a product needs to be compact and/or lightweight, then HDI technology will most likely be applied. The benefits of HDI technology include:
- Reduced space requirement using smaller vias, reduced trace width and reduced trace spacing, all of which allow components to be placed in closer proximity
- Reduced layer count as a result of increased routing channels on internal layers
- Improved signal integrity due to shorter distance connections and lower power requirements
- Improved power integrity due to ground planes closer to the surface parts and improved distribution of capacitance
- Potential to lower fabrication and assembly costs by consolidating multiple PCB’s into a single PCB
When utilizing HDI technology, two basic HDI structures exist:
- Build-up or sequential build-up (SBU) structures
- Any-layer structures
A key aspect of HDI technology is the use of microvias. For reference, the IPC HDI Design Committee has identified microvias as any hole equal to or less than 150 microns. Multiple types of HDI stack-ups associated with blind and buried microvias can be used to meet the density and cost requirements for today’s products. Design teams should develop stack-ups in conjunction with the board fabricator to minimize cost and meet signal integrity requirements. There may also be additional requirements related to plating and specific materials. As a rule, the vendor will adjust all the stack-up variables as needed during their process to meet the end-product requirements.
To read this entire article, which appeared in the November 2017 issue of The PCB Design Magazine, click here.
Suggested Items
2025 ASEAN IT Spending Growth Slows to 5.9% as AI-Powered IT Expansion Encounters Post-Boom Normalization
06/26/2025 | IDCAccording to the IDC Worldwide Black Book: Live Edition, IT spending across ASEAN is projected to grow by 5.9% in 2025 — down from a robust 15.0% in 2024.
DownStream Acquisition Fits Siemens’ ‘Left-Shift’ Model
06/26/2025 | Andy Shaughnessy, I-Connect007I recently spoke to DownStream Technologies founder Joe Clark about the company’s acquisition by Siemens. We were later joined by A.J. Incorvaia, Siemens’ senior VP of electronic board systems. Joe discussed how he, Rick Almeida, and Ken Tepper launched the company in the months after 9/11 and how the acquisition came about. A.J. provides some background on the acquisition and explains why the companies’ tools are complementary.
United Electronics Corporation Advances Manufacturing Capabilities with Schmoll MDI-ST Imaging Equipment
06/24/2025 | United Electronics CorporationUnited Electronics Corporation has successfully installed the advanced Schmoll MDI-ST (XL) imaging equipment at their advanced printed circuit board facility. This significant technology investment represents a continued commitment to delivering superior products and maintaining their position as an industry leader in precision PCB manufacturing.
Insulectro & Dupont Host Technology Symposium at Silicon Valley Technology Center June 25
06/22/2025 | InsulectroInsulectro, the largest distributor of materials for use in the manufacture of PCBs and printed electronics, and DuPont, a major manufacturer of flex laminates and chemistry, invite fabricators, OEMS, designers, and engineers to attend an Innovation Symposium – Unlock the Power - this Wednesday, June 25, at DuPont’s Silicon Valley Technology Center in Sunnyvale, CA.
OKI, NTT Innovative Devices Establish Mass Production Technology for High-Power Terahertz Devices by Heterogeneous Material Bonding
06/21/2025 | BUSINESS WIREOKI, in collaboration with NTT Innovative Devices Corporation, has established mass production technology for high-power terahertz devices using crystal film bonding (CFB) technology for heterogeneous material bonding to bond indium phosphide (InP)-based uni-traveling carrier photodiodes (UTC-PD) onto silicon carbide (SiC) with excellent heat dissipation characteristics for improved bonding yields.