-
- News
- Books
Featured Books
- design007 Magazine
Latest Issues
Current IssueAll About That Route
Most designers favor manual routing, but today's interactive autorouters may be changing designers' minds by allowing users more direct control. In this issue, our expert contributors discuss a variety of manual and autorouting strategies.
Creating the Ideal Data Package
Why is it so difficult to create the ideal data package? Many of these simple errors can be alleviated by paying attention to detail—and knowing what issues to look out for. So, this month, our experts weigh in on the best practices for creating the ideal design data package for your design.
Designing Through the Noise
Our experts discuss the constantly evolving world of RF design, including the many tradeoffs, material considerations, and design tips and techniques that designers and design engineers need to know to succeed in this high-frequency realm.
- Articles
- Columns
- Links
- Media kit
||| MENU - design007 Magazine
PCB Cooling Strategies, Part 2
January 24, 2018 | Bin Zhou, EDADOCEstimated reading time: 8 minutes
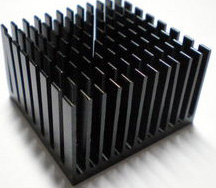
Part 1 of this article appeared in last week’s issue of the Inside Design Newsletter, available here.
In PCB design, the choice of components has a direct impact on the cooling effect. Fortunately, a variety of devices are available for us to choose from. Through-hole (THD) devices or “plug-in” devices feature a small number of pins. The body of the device does not come into close contact with the PCB after soldering, so the thermal correlation with the board is very small. The heat generated by this type of device dissipates through the device surface.
So, in areas with high air mobility, this type of cooling performance is preferable. However, such packages are separate devices and since many PCB boards take up a large amount of space, the package size cannot be miniaturized, so there are some limitations in their use.
Surface mounted (SMD) components require more heat dissipation, so thermal design is critical. The SMD’s pin count and density are high, and after soldering the body of the device is close to the PCB, so the heat of the entire board is closely interrelated. Due to the miniaturization of electronic devices today, the use of SMD devices is increasing. Some products have completely replaced THD components with SMD. So, solving the problem of heat dissipation in SMD devices have become a key issue for chip manufacturers today. SMD components come in many types of packages.
BGA package devices are mounted on the PCB with solder balls or bumps. The heat is mainly dissipated in the package’s surface. Small outline package (SOP) devices are pin-type, with poor thermal performance, so cooling of the device is difficult.
Because the components of the package are relatively small, heat dissipation through the surface of the device is minimal. Once we select an SMD component, we must select a thermal pad package for the center of the device to transfer heat to the PCB. The heat will be dissipated through the PCB’s copper foil area. We must use a heat sink to facilitate cooling.
Component placement plays a decisive role in PCB cooling. Our design methods vary depending on the situation. For example, in a chassis with a fixed fan blowing on the surface of the PCB, the entire system has convection cooling. So, that layout design must consider air duct design issues. We need to create a reasonable layout design to ensure the board has good ventilation to distribute air flow and maintain normal temperatures.
Component Placement Considerations
- With high-heat radiation components, a centralized ventilation and cooling system will work separately to avoid mutual interference with the main motherboard.
- Uniform distribution of heat capacity on the PCB surface is critical. Do not concentrate all the large power devices in one area. If unavoidable, put shorter components upstream from the airflow, and ensure sufficient air flow through the heat dissipation area.
- Make the heat transfer path as short as possible.
- Make the heat transfer cross-section as large as possible.
- Keep in mind the thermal radiation of the surrounding parts. Thermally sensitive components (e.g., semiconductor packages) should be kept away from the heat or isolated.
- Ensure that forced ventilation is consistent with natural ventilation.
- With daughter boards, the device air duct and ventilation must flow in the same direction.
- Create sufficient distance between the air intake and exhaust area.
- The heating device should be placed on the top of the product, and in the airflow channel when conditions permit.
- Components with high heat or current cannot be placed in the corners and edges of the PCB. Install the heat sink as far away as possible from other components. Ensure that the cooling channels are smooth.
Heat Sink Considerations
Adding a heat sink to the board is another good way to dissipate heat. A heat sink transfers the heat from the electronic components to the heat dissipation device, which is made of aluminum, brass or bronze plate, etc. Commonly used heat sink materials include copper and aluminum, and both have advantages and disadvantages. Copper has better thermal conductivity, but it is more expensive and difficult to process. It is heavier (a lot of copper radiators exceed the CPU weight limit), the heat capacity is small, and easily oxidizes. Pure aluminum is too soft, so it cannot be used directly. For most PCBs, an aluminum heat sink is sufficient.
Figure 7 depicts a copper heat sink with four screw holes fixed. With this heat sink, the wind guide groove needs to be placed along the direction of the air flow to prevent the radiator from being blocked and impact the heat dissipation performance.
The heat sink in the Figure 8 is adhesive and does not require a fixing screw hole. Because the air guiding grooves are located on all sides, the mounting directions are not fixed and can adapt to the air flow, making it more flexible.
Page 1 of 2