-
- News
- Books
Featured Books
- smt007 Magazine
Latest Issues
Current IssueWhat's Your Sweet Spot?
Are you in a niche that’s growing or shrinking? Is it time to reassess and refocus? We spotlight companies thriving by redefining or reinforcing their niche. What are their insights?
Moving Forward With Confidence
In this issue, we focus on sales and quoting, workforce training, new IPC leadership in the U.S. and Canada, the effects of tariffs, CFX standards, and much more—all designed to provide perspective as you move through the cloud bank of today's shifting economic market.
Intelligent Test and Inspection
Are you ready to explore the cutting-edge advancements shaping the electronics manufacturing industry? The May 2025 issue of SMT007 Magazine is packed with insights, innovations, and expert perspectives that you won’t want to miss.
- Articles
- Columns
- Links
- Media kit
||| MENU - smt007 Magazine
Estimated reading time: 3 minutes
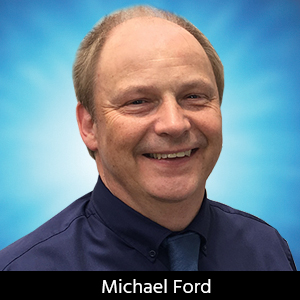
Counterfeit: A Quality Conundrum
There is an imminent, critical challenge facing every manufacturer in the industry. The rise in the ingress of counterfeit materials into the supply chain has made them prolific, though yet, the extent is understated. What needs to be faced now is the need for incoming inspection, but at what cost to industry, and does anyone remember how to do it?
Going back 20 years, the incoming inspection of materials was common throughout the electronics assembly industry. At that time, component material and production technologies were relatively new, with sizes beginning to diminish, led by design pressure, which gave rise to what we would now regard as frequent failures. Having to repair or replace circuit boards after assembly, or later once assembled on the main production lines, was a very expensive challenge. I saw numerous cases of production lines where epidemic rates of material-related quality issues had been detected, and it was decided to simply remove the defective products from the line so that the line could continue while the products were being re-worked. Unfortunately, the re-work rate was often longer than the rate at which defects were discovered, resulting in significant stock-piles. Once, to compound the problem, visitors were due to be touring the plant the next day. Local companies selling very large black sheets saw their sales sky-rocket, as defective products in the factory were hidden in every place conceivable.
The situation was not a one-off. This was daily life at so many manufacturing sites back in the “wild West” days. To be fair, faulty materials were not the only contributor to defect rates that were so bad, a quality manager today wouldn’t allow the factory to produce a single thing. Assembly processes, especially SMT, itself a relatively new technology, were also quite variable in those days. Materials, however, were the one thing that could not be controlled or addressed by industrial engineering practice. The solution, as we would say today, was to “left-shift” the problem into the material receiving operation. There, materials could be measured and inspected as they were booked into the factory, so as to engender confidence that they would be fit for production and not contribute to assembly line failures.
In fact, a great deal of testing also ended up being introduced at many stages in the production flow, as the final assembly line became the one thing in the factory that must not stop, as it would cause delivery issues to customers. Increased forms of in-line testing and inspection, including automated methods such as ICT, AOI, etc., became commonplace and continue to be regarded as essential. Segmentation of production areas, each with associated buffer stock, also became common. The increased cost to manufacturing was quite severe and contributed in no small way to manufacturing moving overseas to areas where the labor needed to per-form all of these enhanced tasks was cheaper.
In the wild West, however, action still need-ed to be taken to reduce the costs of test and inspection as much as possible to keep what little remained competitive. As far as incoming inspection was concerned, manufacturers started to extend relationships with material suppliers to provide guidance on expected quality lev-els and provide help and training in sampling and testing so that suppliers could take owner-ship of the quality of their materials. Once a degree of control was established, contracts were put into place with responsibility for material defects to be placed with the supplier, relieving manufacturing progressively of incoming inspection tasks. The impact on the business of manufacturing was significant, which went beyond the labor saving.
With reliable material quality and supply, buffer stocks could be reduced and handling de-creased. The age of efficient, Kanban and just in time (JIT) material delivery was enabled. Trace-ability was positioned as the police force of the supply-chain, as it could in theory assign responsibility for material defects found in manufacturing and beyond, back to the material sup-plier. In some cases, this happened successfully for those who took traceability seriously, utilizing the specialist software tools needed for complex production processes from multiple vendors with huge bills of materials. With relation-ships and trust in place between material sup-pliers and manufacturers, incoming material inspection has become almost redundant, providing significant cost reduction, which has al-ready helped to tip the balance for the on-shore business case for manufacturing.
That is, until now…
Continue reading this article in the October 2017 issue of SMT Magazine.
More Columns from Smart Factory Insights
Smart Factory Insights: Making Rework a Smart Business OpportunitySmart Factory Insights: The Sustainability Gold Rush
Smart Factory Insights: Today’s Manufacturing Jobs Require a New Skill Set
Smart Factory Insights: Compose Yourself, Mr. Ford
Smart Factory Insights: The Smart Business Case for Local PCB Manufacturing
Smart Factory Insights: Manufacturing Digital Twin—Spanners in the Works
Smart Factory Insights: Machines, People, and AI
Smart Factory Insights: Is Sustainability in Manufacturing a Benefit or Burden?