Estimated reading time: 8 minutes
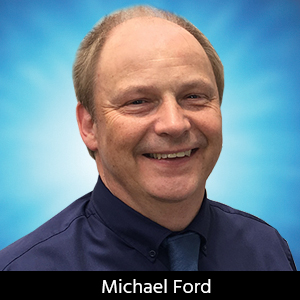
Advanced Digitalization Makes Best Practice Part 1: Digital Remastering
As digitalization and the use of IoT in the manufacturing environment continues to pick up speed, critical changes are enabled, which are needed to achieve the levels of performance and flexibility expected with Industry 4.0. Existing practices must be questioned and re-evaluated in the digital factory context. In this series, we look at examples of the traditional barriers to flexibility and value creation and suggest new digital best practices to see how these barriers can be avoided, or even eliminated.
To understand more advanced opportunities provided by factory digitalization and IoT, we will consider both the manufacturing operation and the plight of the machine vendor, who has invested time and money, working hard to create an excellent automation technology that meets an industry need in a highly competitive environment. Even after the core technology of the machine has been developed and refined, there have traditionally been significant barriers to overcome related to the communication of critical information. The machine itself in isolation is an example of Industry 3.0, an automated, self-contained process.
The connection of the machine into the digital infrastructure of the factory is the first key step towards Industry 4.0. The part played by the digital IoT revolution is to remove these communication barriers and bring a real value to the machine vendor, not only reducing needless costs, but also enabling the creation of additional added-value in the machines themselves. The first such information exchange is the engineering data needed to create the detailed machine instructions.
From Legacy Engineering Data Processing...
For any automated machine to operate, it is necessary to have a sequence of digital instructions to follow. The creation of these involves a clear and detailed understanding of the product design and the bill of materials (BOM). As there are many automated machine processes involved with the assembly of a circuit board, each assembly process needs to understand their role, and select the data from the design/BOM combination that is relevant. This is repeated at every process, hopefully without duplication or anything missing. For assembly processes, the materials or actions that need to be performed at the process will be selected, with an understanding of what has been done at prior processes.
For test or inspection processes, the clear and detailed knowledge of what has been done at prior processes is essential. Production engineers using the machine vendor software must make sense of information and select the appropriate data from what is given in whichever format the customer makes available. As there is so much variation in data formats and potentially many documents and files, there is a lot of checking and adjustment or translation of data to be done to avoid conflicts.
This is a major pain for the machine vendor, as the customer ends up needing many layers of user-interfaces with which to perform these tasks, which the machine vendor is expected to provide. Any mistakes in the data preparation manifest themselves as incorrect machine operation, which often is initially attributed to the machine itself. A lot of effort is expended by the machine vendor to try to eliminate risks and issues, even though these are not essentially the vendor’s responsibility.
The machine data preparation software should be focusing on taking the product data, together with knowledge of the machine features and capabilities, to create the most efficient and effective operation as possible. With the continuous increase in product mix, the frequency of changes from one product to another increases, which brings a greater frequency of new product introductions and changes in machine setup. In many cases already, the time taken to change the setup of the machine between sequential work-orders representing different products exceeds the actual time that the machine is working to add value. Were the machine vendor to have visibility of the data for the whole sequence of expected production work-orders in the near-term, their operational optimization could be extended to include consideration of how to reduce setup time between products (e.g., through the creation of the common location of materials, as long as machine execution time was not too severely affected). This can be especially effective where multiple processes in a connected line are grouped and managed through a single overall machine vendor software platform such as those currently provided by the larger machine vendors. However, this creates the need for product data to be available to the machine vendors’ software earlier.
As Industry 4.0 brings a yet higher level of flexibility requirement, this easily overloads the engineering data preparation capability. In most operations it is already a challenge to keep up with data preparation on a done-by-one basis. Neither machine vendors nor manufacturing engineering will be able to achieve the expected flexibility in the flow of data required for Industry 4.0 without the help of digitalization.
…To Digital Best Practice
Having data from design (both electrical and mechanical) and BOM delivered as a single digital product model, in the form for example of the IPC-2581 standard, means that a vast amount of product data processing of the otherwise many documents and files is eliminated. This approach really makes sense considering that practically every product is designed digitally and every BOM is maintained digitally. There is simply no reason any more why the product data should be split into legacy formats intended for humans to process. Issues raised about product IP protection are nonsense, as however the data is sent, the product data itself is eventually re-created by the manufacturing entity in a format that can easily be replicated. The core issue is that the use of legacy formats forces human intervention, which creates unnecessary cost, delay, and the likelihood of mistakes, all of which fundamentally affect the business performance of the product. Being an open standard, the use of the IPC-2581 digital product model is available as a standard single-click output from professional design systems. The design through manufacturing flow, that is the communication of the product model to manufacturing can therefore be done in seconds, rather than hours or even days.
The next stage of the digital process is to utilize a digital manufacturing engineering system that has knowledge of production configurations, that will apply the digital product model to a line configuration, automatically splitting out the data as required by each of the processes. Once again, the digital solution reduces work that once took hours or days into a few seconds. As this data assignment process can be done so quickly, the selection of a specific line configuration need not be fixed far in advance. The assignment of line and creation of the work-order can in fact be done very close to the start of production without risk. This means that there is the ability to have a choice of multiple line configurations, each of which can be assessed to decide which one meets the immediate customer need in the most efficient way. The best manufacturing engineering systems therefore support assignment of product to line configuration “on demand.”
This enables real-world factory schedules and work-order assignments to be made just in time, such that immediate reaction can be made to changes in customer demand. This contrasts significantly with prior Industry 3.0 practices, where decisions had to be made at the shop-floor level many days or weeks in advance, with only crude and often ineffective simulation techniques for planning optimization. This new best practice of digitalization of the engineering data preparation process is therefore completely in line with the requirements of Industry 4.0, and in fact without it, there is no chance that an Industry 4.0 operation could practicably be sustained.
DDD Best Practice
Digital best practices, including the use of the digital product mode for both automated machine processes to take place and the creation of paperless product documentation/work-instructions for non-automated processes, which will be covered in more detail later, means that everything required for manufacturing is created digitally, transferred digitally, and executed digitally. For those who remember the birth of digital music on CD, this is the sought after DDD format of music, where no analogue, or in this case human manipulation of the data has taken place.
This is the first piece of our digital re-mastering of MES, where new best practices are developing. As a summary of the digital best practice flow for preparation of data for automated processes:
1. Digital Design Process
a. A digital product model is created by the design system in IPC-2581 format, including both the electrical and mechanical design features.
b. Where supply-chain data is managed centrally (in a multi-site organization with centralized PLM for example), the production BOM is applied to the IPC-2581 file directly before it reaches manufacturing
2. Digital Manufacturing Engineering System
a. The single IPC-2581 digital product model file is received into manufacturing
b. Where supply-chain data is managed locally by ERP, the BOM data is merged, on receipt of a single digital file
c. The manufacturing engineering tool identifies capable line configurations, which are communicated to the digital production planning system
3. Digital Planning Process
a. The decision about which choice of line configuration to use is made depending on the immediate customer demand requirement. The decision-making algorithm considers the capabilities and availability of machine processes, effects of the commonality of product mix and availability of resources.
4. Digital final process optimization and execution:
a. Information is transmitted from the digital manufacturing engineering system to the identified machines. This is best done using the digital IPC Connected Factory Exchange (CFX) IoT protocol.
b. The machine vendor receives an assured dataset, which can be used reliably to create the optimized machine operation. In high-mix or Industry 4.0 scenarios, the machine vendor can include optimization of the machine setup together with execution optimization based on the sequence of products that will be executed.
Following this digital best practice, the manufacturer receives their expected benefit, with a significant reduction in new product introduction lead-times, a step change in flexibility, the elimination of engineering mistakes, and the ability to support an Industry 4.0 operation from an engineering perspective. For the machine vendor, there is a huge reduction in the work needed by the software to resolve external data issues. This enables them to focus on optimization, that includes grouping of products planned in a flexible way, to be executed in a known sequence, such that changeover times can be reduced. Though the time needed to prepare and setup the machine has greatly reduced, the effectiveness and performance of the machine overall will increase, thus increasing the value proposition of the machine especially in Industry 4.0 scenarios.
This is the first part in a series in which we look at new digital best practices. The series includes looking at manual processes, the supply-chain, quality management as well as planning, and how digital data formats and communication standards combine to create the new paradigm of digital manufacturing and Industry 4.0.
More Columns from Smart Factory Insights
Smart Factory Insights: Making Rework a Smart Business OpportunitySmart Factory Insights: The Sustainability Gold Rush
Smart Factory Insights: Today’s Manufacturing Jobs Require a New Skill Set
Smart Factory Insights: Compose Yourself, Mr. Ford
Smart Factory Insights: The Smart Business Case for Local PCB Manufacturing
Smart Factory Insights: Manufacturing Digital Twin—Spanners in the Works
Smart Factory Insights: Machines, People, and AI
Smart Factory Insights: Is Sustainability in Manufacturing a Benefit or Burden?