-
-
News
News Highlights
- Books
Featured Books
- design007 Magazine
Latest Issues
Current IssueAll About That Route
Most designers favor manual routing, but today's interactive autorouters may be changing designers' minds by allowing users more direct control. In this issue, our expert contributors discuss a variety of manual and autorouting strategies.
Creating the Ideal Data Package
Why is it so difficult to create the ideal data package? Many of these simple errors can be alleviated by paying attention to detail—and knowing what issues to look out for. So, this month, our experts weigh in on the best practices for creating the ideal design data package for your design.
Designing Through the Noise
Our experts discuss the constantly evolving world of RF design, including the many tradeoffs, material considerations, and design tips and techniques that designers and design engineers need to know to succeed in this high-frequency realm.
- Articles
- Columns
- Links
- Media kit
||| MENU - design007 Magazine
Advanced Stackup Planning with Impedance, Delay and Loss Validation
August 2, 2018 | Yuriy Shlepnev, SimberianEstimated reading time: 2 minutes
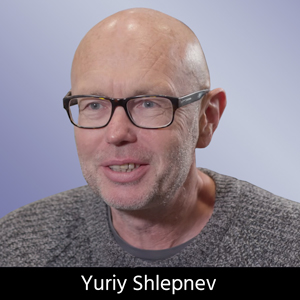
A typical PCB design usually starts with the material selection and stackup definition—the stackup planning or design exploration stage. How reliable are the data provided by the material vendors and PCB manufacturers? Can we use these data to predict trace width and spacing for the target trace impedance or to calculate delays or evaluate the loss budget?
PCB routing is usually done with these preliminary data. The actual stackup may be further adjusted by the PCB manufacturer together with the trace widths and spacing, to have the target impedances. This is the typical impedance-controlled process that is well established and usually produces an acceptable outcome.
But what about the losses? Can we use preliminary data to evaluate the losses and loss-related compliance metrics? Or can we just specify the target losses and rely on the manufacturers, as is done with the impedance? Let’s try to answer these questions. An EvR-1 validation board is used here as an example with the preliminary and final data—all data for this board are provided by Marko Marin from Infinera. This board was featured in our award-winning “Expectation vs. Reality” paper. We will use Simbeor software as the stackup exploration tool to evaluate the accuracy of the characteristic impedance, delay and losses. Simbeor is selected for the stackup exploration because it is systematically validated with the measurements up to 50 GHz.
Stackup planning begins with selecting a PCB manufacturer and possible materials and defining the stackup structure. In our case, the validation board has 20 layers with 8 layers assigned for the high-speed signals as shown in Figure 1. Low-loss Panasonic Megtron6 laminate is selected to rout the high-speed interconnects. The target impedance has been specified for the PCB manufacturer, and the manufacturer has provided expected stackup structure, trace widths, and spacing adjustments to fulfill the target impedances. This is the usual case for a production board.
According to the manufacturer, the expected impedance variations should be within 8%. That is too large to expect excellent correlation up to 30 GHz for 28 Gbps NRZ links, but it may be acceptable. The board manufacturer provided stackup geometry as shown in Figure 1 on the left side, and corresponding stackup entered for the pre-layout analysis into Simbeor software is shown on the right side. Megtron6 specs provide dielectric constant and loss tangent at multiple frequencies—just one frequency data can be used to define causal wideband Debye model. The values for Dk in the Figure 1 are slightly different from the Megtron6 specs and are provided by the PCB manufacturer based upon their experience with this material.
To read this entire article, which appeared in the July 2018 issue of Design007 Magazine, click here.
Suggested Items
Insulectro & Dupont Host Technology Symposium at Silicon Valley Technology Center June 25
06/22/2025 | InsulectroInsulectro, the largest distributor of materials for use in the manufacture of PCBs and printed electronics, and DuPont, a major manufacturer of flex laminates and chemistry, invite fabricators, OEMS, designers, and engineers to attend an Innovation Symposium – Unlock the Power - this Wednesday, June 25, at DuPont’s Silicon Valley Technology Center in Sunnyvale, CA.
Ventec Strengthens Commitment to Halogen-Free PCB Manufacturing in Europe
06/11/2025 | Ventec International GroupVentec International Group, the PCB materials innovator, manufacturer, supplier and one-stop shop for copper clad laminates, prepregs, as well as process consumables and PCB manufacturing equipment has established volume inventory of halogen-free FR4.1 and FR15.1 PCB materials at its European hub in Germany.
Ventec International Group Enters into a Fulfillment and Supply Agreement with Matrix and Launches Ventec Americas
06/09/2025 | Ventec International GroupVentec is excited to announce a new partnership with Matrix aimed at enhancing the fulfillment, value-added conversion, and distribution of PCB base materials across the North American market. This collaboration is set to significantly improve supply chain efficiency, and delivery performance for the company's North American customers.
Panasonic Appoints Matrix as its Authorized Distributor in Europe
06/03/2025 | Matrix ElectronicsEffective July 1st, 2025, Panasonic Industry Co., Ltd. has appointed Matrix Electronics Limited as its Authorized Distributor in the European region.
From DuPont to Qnity: A Bold Move in Electronics Materials
05/14/2025 | Marcy LaRont, I-Connect007DuPont has announced the intended spinoff of a public independent electronics company, Qnity, which will serve as a solutions provider to the semiconductor and electronics industries to enhance competitiveness and innovation in advanced computing, smart technologies, and connectivity. In this interview, Jon Kemp, Qnity CEO-elect and current president of DuPont’s Electronics business, shares his insights on the strategic separation from DuPont.