-
- News
- Books
Featured Books
- pcb007 Magazine
Latest Issues
Current IssueThe Hole Truth: Via Integrity in an HDI World
From the drilled hole to registration across multiple sequential lamination cycles, to the quality of your copper plating, via reliability in an HDI world is becoming an ever-greater challenge. This month we look at “The Hole Truth,” from creating the “perfect” via to how you can assure via quality and reliability, the first time, every time.
In Pursuit of Perfection: Defect Reduction
For bare PCB board fabrication, defect reduction is a critical aspect of a company's bottom line profitability. In this issue, we examine how imaging, etching, and plating processes can provide information and insight into reducing defects and increasing yields.
Voices of the Industry
We take the pulse of the PCB industry by sharing insights from leading fabricators and suppliers in this month's issue. We've gathered their thoughts on the new U.S. administration, spending, the war in Ukraine, and their most pressing needs. It’s an eye-opening and enlightening look behind the curtain.
- Articles
- Columns
- Links
- Media kit
||| MENU - pcb007 Magazine
Catching up with LiloTree’s Dr. Kunal Shah
August 2, 2018 | Dan BeaulieuEstimated reading time: 7 minutes
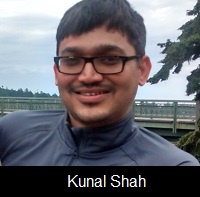
Every so often, a new product comes around that promises to be a game changer and LiloTree has one of those products. Not only is it cyanide-free, it has the potential to save 40% on your entire ENIG process and is proving to be far more stable than traditional ENIG products.
Dan Beaulieu: Dr. Shah, please introduce yourself and your company to our readers.
Dr. Shah: I started the company in 2012 on the basis of supporting electronics customers to improve their products and develop new materials technology to improve performance and reliability of electronic assemblies. LiloTree has been providing product improvement solutions to many industries including medical electronics, aviation-aerospace, semiconductor, naval electronics, etc.
I hold a doctorate in Materials Science & Engineering, and my focus has been developing/supporting materials technologies for various areas of the electronics industry. I was a senior research scientist at Intel and instrumental in developing polymer passivation layer/interlayer dielectric material for microelectronic devices, which got integrated into all ICs from 2008 onward.
Beaulieu: Please tell me the story of your new product. How was it developed and why?
While working with companies in these industries on various projects/failures/issues, one common theme kept arising: surface finish-related failures on PCBs, especially ENIG. Several failures from companies in the medical electronics and aviation-aerospace area included black pad (hyper-corrosion) related failures leading to malfunctioning of electronic assemblies. Usually in product improvement solutions we tend to provide recommendations to customers to improve their products so that the failure at hand would not return. However, in the case of ENIG, there was no solution out there since we understood the fundamental root cause of the problem. That’s when we decided to develop our own ENIG to resolve these issues; we call our discovery and development ENIG-Premium. Our development of ENIG-Premium tied perfectly to our vision of advanced engineered materials.
So, essentially, ENIG-Premium originated from industry needs. There are so many failures we have come across through our wide customer base along with numerous instances reported at various platforms that we realized the need for a better product to resolve these issues. Moreover, most ENIG chemistries available in the market use cyanide-based immersion gold chemistry which has health and ecological hazards. Immersion gold chemistry developed for ENIG-Premium is cyanide-free chemistry, hence eco-friendly.
During the journey of development, we applied for a National Science Foundation (NSF) Small Business Innovation Research (SBIR) grant. In September 2017, LiloTree was awarded a $750,000 grant (till date close to $1M including Phase I) from NSF via highly competitive SBIR Phase II program to develop ENIG-Premium to address the issues just mentioned.
Beaulieu: Can you go into a little more detail about the chemistry?
Shah: ENIG-Premium includes a proprietary barrier layer (patents pending) between the electroless nickel-phosphorus (Ni-P) and immersion gold. The barrier layer passivates the underneath electroless Ni-P and provides significant corrosion resistance. Also, the gold layer deposition has a bare minimum thickness compliant to IPC 4552, which can provide significant cost savings. Moreover, due to the presence of barrier layer, the intermetallic formed between the nickel and tin becomes distinct and compact leading to robust solder joints. This process can be seamlessly adopted by any PCB manufacturer without any overhead or capital investment. The cost and process are the same as for conventional ENIG, but the chemistry is different.
Beaulieu: How does the product affect reliability?
Shah: ENIG surface finish is prone to black pad defects and failures from de-wetting and/or brittle solder joints, which pose risk of field failures or reliability concerns for electronic assemblies. Depending on the severity of the application and industry, there could be human lives at risk due to malfunctioning electronic devices, which of course can result in financial and legal consequences.
Beaulieu: Besides the advantages it has for their customers, what are the advantages to the shops themselves?
Shah: Most ENIG offerings come with cyanide-based gold chemistry. Depending on its form, dose and rate of exposure, technicians and engineers involved in the processing of cyanide-based chemistry during ENIG plating can be exposed and suffer from the toxic nature of cyanide. A cyanide-gold spill could mix with other plating chemistry to produce toxic gas. Hence, every plating facility must post-process their cyanide-based wastewater to be compliant with their respective county, city and the EPA, which in turn adds cost to ENIG plating process. ENIG-Premium is cyanide-free.
Also, ENIG-Premium costs either equivalent or slightly less than current ENIG offerings. The primary reason for the cost benefit is the gold deposition thickness. Gold layer thickness for conventional immersion gold process is auto limiting, and thickness can’t be controlled, which leads to non-uniform thickness. Distribution can range from 75-100 nm. Gold deposition for ENIG-Premium is uniform and can be controlled to bare minimum thickness of 50 nm (compliant with IPC). This leads to significant cost savings to PCB manufacturers since less gold is better in terms of cost and solder joint reliability.
Beaulieu: Which industries are using your product and how are they using it?
Shah: Industry sectors including aviation-aerospace, medical electronics, semiconductor, etc., have shown very strong interest in the product. Several OEMs/PCB manufacturers have evaluated the product exhaustively and have adopted it. Mainly, the OEMs/PCB manufacturers who identify that high-reliability is critical have shown strong interest in adopting this product.
Beaulieu: What qualifications and certifications do you have?
Shah: We have had a third-party accredited testing lab conduct reliability tests on ENIG-Premium and solder joints, which showed marked improvement in solder joints reliability. We are currently working with various IPC committees to be included as part of various IPC specifications.
Page 1 of 2
Suggested Items
SHENMAO Strengthens Semiconductor Capabilities with Acquisition of PMTC
07/10/2025 | SHENMAOSHENMAO America, Inc. has announced the acquisition of Profound Material Technology Co., Ltd. (PMTC), a premier Taiwan-based manufacturer of high-performance solder balls for semiconductor packaging.
KYZEN to Highlight Understencil and PCB Cleaners at SMTA Querétaro Expo and Tech Forum
07/09/2025 | KYZEN'KYZEN, the global leader in innovative environmentally responsible cleaning chemistries, will exhibit at the SMTA Querétaro Expo & Tech Forum, scheduled to take place Thursday, July 24, at Centro de Congresos y Teatro Metropolitano de Querétaro.
Driving Innovation: Direct Imaging vs. Conventional Exposure
07/01/2025 | Simon Khesin -- Column: Driving InnovationMy first camera used Kodak film. I even experimented with developing photos in the bathroom, though I usually dropped the film off at a Kodak center and received the prints two weeks later, only to discover that some images were out of focus or poorly framed. Today, every smartphone contains a high-quality camera capable of producing stunning images instantly.
Hands-On Demos Now Available for Apollo Seiko’s EF and AF Selective Soldering Lines
06/30/2025 | Apollo SeikoApollo Seiko, a leading innovator in soldering technology, is excited to spotlight its expanded lineup of EF and AF Series Selective Soldering Systems, now available for live demonstrations in its newly dedicated demo room.
Indium Corporation Expert to Present on Automotive and Industrial Solder Bonding Solutions at Global Electronics Association Workshop
06/26/2025 | IndiumIndium Corporation Principal Engineer, Advanced Materials, Andy Mackie, Ph.D., MSc, will deliver a technical presentation on innovative solder bonding solutions for automotive and industrial applications at the Global Electronics A