-
- News
- Books
Featured Books
- pcb007 Magazine
Latest Issues
Current IssueThe Hole Truth: Via Integrity in an HDI World
From the drilled hole to registration across multiple sequential lamination cycles, to the quality of your copper plating, via reliability in an HDI world is becoming an ever-greater challenge. This month we look at “The Hole Truth,” from creating the “perfect” via to how you can assure via quality and reliability, the first time, every time.
In Pursuit of Perfection: Defect Reduction
For bare PCB board fabrication, defect reduction is a critical aspect of a company's bottom line profitability. In this issue, we examine how imaging, etching, and plating processes can provide information and insight into reducing defects and increasing yields.
Voices of the Industry
We take the pulse of the PCB industry by sharing insights from leading fabricators and suppliers in this month's issue. We've gathered their thoughts on the new U.S. administration, spending, the war in Ukraine, and their most pressing needs. It’s an eye-opening and enlightening look behind the curtain.
- Articles
- Columns
- Links
- Media kit
||| MENU - pcb007 Magazine
Study on Application of Four-Wire and Four-Terminal Flying Probe Test Scheme
August 10, 2018 | Jin Erbing, Joint Stars Technology Co., LtdEstimated reading time: 6 minutes
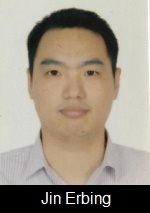
The Problem
The traditional electrical performance conduction test is to determine the open/short circuit by the on-resistance. For example, it is generally set to 20 ohms (Ω). When the entire measured line is less than 20Ω, the line-to-line continuity of the tested line can be determined to meet the requirements. However, in actual production, some defects of the PCB circuit board, such as voids in the holes, thin copper, hole copper, and separation of the innerlayers, will affect the resistance of the circuit. The above defective boards are tested by ordinary conduction tests. The results showed that PASS, after welding or application environment changes, the line resistance will change, and even lead to open circuit. These problems will inevitably have great impact on product quality.
The Problem Analysis
The traditional electrical performance test uses the four-wire two-terminal test principle. It is impossible to measure the actual resistance of the circuit accurately. The tested resistance value includes the test pin, wire and contact resistance (R1, R2), as shown in Figure 1.
Figure 1: Traditional electrical performance test.
How can we more accurately test the resistance of the circuit under test, especially when the resistance of the circuit under test is in the order of milliohm, the test pin, wire and contact resistance cannot be omitted, and four-wire and four-terminal test must be used?
Four-Wire and Four-Terminal Test
Introduction
The four-wire and four-terminal test passes two pins on each test point, so that the test current and the measured voltage do not affect each other, and the measured resistance can be accurately measured as R=U/I (Figure 2).
Figure 2: Four-wire, four-terminal test.
Figure 2a: Four-wire four-terminal test pin structure.
The four-wire test needle technical requirements are as follows:
- The test needle blade is a pair of mirror structure, the tip error of the two blades is within 10 μm
- Insulation must be done between the two blades, and no contact short-circuit condition can occur during the test
- The distance between two blades must be controlled within 20 μm
- Test needle pressure needs to be adjusted to 10g–25g
How to Conduct Effective Testing
For hole breakage, voids, and insufficient hole copper thickness, the hole-to-hole test method is required. The test points are mainly set on both sides of the test hole. The test pins are placed on both ends of the hole. Theoretical values calculate the resistance of the hole and set the test setpoint for each hole directly, as in the calculation shown in Figure 3.
D = bore diameter
h = thickness of copper plating
d = hollow section diameter
L = depth of hole or plate thickness
Figure 3: Hole test schematic.
The formula, R=ρ.L/S, is the formula for calculating the conductor resistance. S is the cross-sectional area of the conductor. The unit is the square meter, ρ is the resistivity of the conductor material, the unit is ohm·m2/meter, and the copper is at 20°C. The resistivity was 1.75 × 10−8 ohm·m2/m, and the cross-sectional area represented is S=π [(D/2) 2 – (d/2) 2 ] = 2.19121 × 10–8m2.
Based on the above data, we can conclude:
Plate thickness of 1.6 mm, aperture 0.3 mm, copper thickness of 1 mil through-hole,
R = 1.75 × 10–8 × 1.6×10–3 ÷ 2.19121 × 10–8 = 1.28 x 10–3 ohms, or 1.28 milliohms
Page 1 of 4
Suggested Items
SHENMAO Strengthens Semiconductor Capabilities with Acquisition of PMTC
07/10/2025 | SHENMAOSHENMAO America, Inc. has announced the acquisition of Profound Material Technology Co., Ltd. (PMTC), a premier Taiwan-based manufacturer of high-performance solder balls for semiconductor packaging.
KYZEN to Highlight Understencil and PCB Cleaners at SMTA Querétaro Expo and Tech Forum
07/09/2025 | KYZEN'KYZEN, the global leader in innovative environmentally responsible cleaning chemistries, will exhibit at the SMTA Querétaro Expo & Tech Forum, scheduled to take place Thursday, July 24, at Centro de Congresos y Teatro Metropolitano de Querétaro.
Driving Innovation: Direct Imaging vs. Conventional Exposure
07/01/2025 | Simon Khesin -- Column: Driving InnovationMy first camera used Kodak film. I even experimented with developing photos in the bathroom, though I usually dropped the film off at a Kodak center and received the prints two weeks later, only to discover that some images were out of focus or poorly framed. Today, every smartphone contains a high-quality camera capable of producing stunning images instantly.
Hands-On Demos Now Available for Apollo Seiko’s EF and AF Selective Soldering Lines
06/30/2025 | Apollo SeikoApollo Seiko, a leading innovator in soldering technology, is excited to spotlight its expanded lineup of EF and AF Series Selective Soldering Systems, now available for live demonstrations in its newly dedicated demo room.
Indium Corporation Expert to Present on Automotive and Industrial Solder Bonding Solutions at Global Electronics Association Workshop
06/26/2025 | IndiumIndium Corporation Principal Engineer, Advanced Materials, Andy Mackie, Ph.D., MSc, will deliver a technical presentation on innovative solder bonding solutions for automotive and industrial applications at the Global Electronics A