-
- News
- Books
Featured Books
- smt007 Magazine
Latest Issues
Current IssueSupply Chain Strategies
A successful brand is built on strong customer relationships—anchored by a well-orchestrated supply chain at its core. This month, we look at how managing your supply chain directly influences customer perception.
What's Your Sweet Spot?
Are you in a niche that’s growing or shrinking? Is it time to reassess and refocus? We spotlight companies thriving by redefining or reinforcing their niche. What are their insights?
Moving Forward With Confidence
In this issue, we focus on sales and quoting, workforce training, new IPC leadership in the U.S. and Canada, the effects of tariffs, CFX standards, and much more—all designed to provide perspective as you move through the cloud bank of today's shifting economic market.
- Articles
- Columns
- Links
- Media kit
||| MENU - smt007 Magazine
Cross Functional Teams Drive Strong Focus on Risk Mitigation and Quality
August 15, 2018 | Sandy Kolp, FirstronicEstimated reading time: 4 minutes
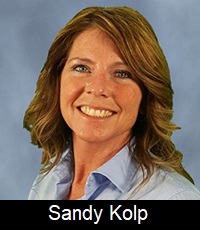
The term CFT (cross-functional team) is used widely in the EMS industry to define the program team that interfaces with each customer. Normally, that term translates to customer-focused team and is a small group comprised of a program manager, customer engineer and buyer/planner. Firstronic's management team felt customers needed the breadth of a traditional cross-functional team approach, defining their CFT model as a much larger group, which includes a tactically focused program manager, a strategically focused account director, a buyer, a product engineer, a process engineer, a test engineer, a quality engineer, a production supervisor or lead person, and a customer service representative focused on materials and scheduling.
The goal was to create a team that was broad-based enough to govern all the necessary outputs associated with each customer. Many of the company’s programs involve production in multiple regions of the world, so the division of labor among a program manager and an account director ensures an internal tactical focus via the program manager, while the account director focuses on strategic and commercial issues and has accountability for global program performance.
Figure 1: Firstronic's CFTs analyze both product and process metrics.
The power of this approach was evident in the company’s transition to the latest revision of the automotive quality standard IATF 16949. The International Standards Organization (ISO) was previously the governing body for ISO/TS 16949, and the current IATF 16949:2016 revision passes that responsibility to the International Automotive Task Force (IATF). Under the new standard, there is greater focus on risk management and definition of stakeholders whose interests must be considered in those assessments.
Firstronic’s facility in Juarez, Mexico, recently received its certification to the revised IATF standard, while its Grand Rapids, Michigan facility will be certified later this year. In implementation, the quality management team found the IATF revision required stronger identification of the scope of the quality management system and customer-specific requirements. A key goal of the implementation process was to integrate risk management analysis into the organization at all levels. This required process definition, analysis of the links with interested parties for each process, and identification of the associated risks.
Figure 2: CFTs encompass a broad range of disciplines overseeing everything from project launch through continuous improvement activities.
One of the first steps was defining process owners and their responsibilities. Process owners included program management, quality engineering, purchasing, sales, customer service, production operators, quality inspectors, shipping, quality management, process engineers, product engineers and supervisors. This aligned well with the CFT team concept already in place since CFTs are catalysts in driving risk mitigation for customer and company, managing product launch, changing management and continuous improvement.
The training program for CFTs is rigorous and includes training on process failure mode effects and analysis (PFMEA); 8D problem solving; corrective and preventative action; statistical process control (SPC); control plans; change management; understanding IATF processes and procedures; advanced product quality planning (APQP); installation, process installation, process qualification and operational qualification; the purchased part approval process (PPAP); and control plans. Six Sigma Green Belt training will be added later in 2018. The goal is to ensure all team members have a strong foundation in the core tools necessary to carry out their defined responsibilities in managing project launch, corrective actions and continuous improvement activities.
Firstronic’s Plex Online ERP system enhances each team’s abilities to manage and mitigate risk. Plex allows searching for process and product risk. As part of every new customer transition, the team looks at the top ten product risks for that customer. Plex gives real-time visibility into all aspects of project activity to top management at all facets of the organization. Supply chain management and new product introduction (NPI) are two of the areas that have been most enhanced in terms of additional risk management tools.
Figure 3: Firstronic's projects often ramp in multiple facilities across the globe simultaneously.
The CFTs are key drivers of continuous improvement and a process one team identifies as necessary for a specific customer may be replicated with additional customers, if warranted. For example, as component availability issues started to become more frequent in one customer’s products last year, the CFT recommended taking a more holistic approach to the problem. In the original model, component availability issues were addressed whenever the lead time on a specific component began to stretch out. The relevant team members would identify alternates and seek approval on those parts from the customer. As component shortages increased, this process was being used more frequently. The team did a complete bill of material (BOM) analysis for the products and gave the customer two to three alternates for every line item, even those without known availability issues. Documentation was provided for all recommendations along with descriptions of whether the alternate parts were drop-in replacements or needed a qualification process. The team then worked with the customer to get all feasible alternates added, managing qualification builds for end customer validation efforts. The process has now been replicated with all customers, particularly on new products.
CFTs are a front-line resource in ensuring that what is delivered to customers meets their requirements. They provide the rest of the organization clear focus on what resources are needed to support the customer. The broad-based nature of this team structure ensures that each customer has a complete set of subject matter experts focused on project execution and continuous improvement. The teams measure a number of metrics including process and specific product yield relative to key performance indicators (KPIs), customer and product line gross margin, forecast accuracy, revenue to project budget, on-time delivery performance, customer satisfaction, corrective actions and inventory turns. If issues arise in the metrics, the team analyses the root cause and recommends appropriate corrective action.
The result is a responsive, coordinated approach that mitigates risk, provides responsive solutions to any issues that develop in the project, and ensures lessons learned are propagated throughout the organization.
This article was originally published in the July 2018 issue of SMT007 Magazine.
Testimonial
"We’re proud to call I-Connect007 a trusted partner. Their innovative approach and industry insight made our podcast collaboration a success by connecting us with the right audience and delivering real results."
Julia McCaffrey - NCAB GroupSuggested Items
LACROIX: Closing of the FIRSTRONIC Acquisition
01/11/2022 | GlobeNewswireLACROIX announces the closing of the acquisition of a majority stake in FIRSTRONIC in the US. This follows the announcement of the signing of an exclusive agreement dated December 16, 20211.
LACROIX Announces Acquisition of Firstronic in the U.S.
12/20/2021 | LACROIXLACROIX announces that it has signed an exclusive agreement for the acquisition of a majority stake in the capital of the US company Firstronic with its main shareholders.
Firstronic Pair Named as Entrepreneur of the Year 2020 Michigan and Northwest Ohio Award Finalists
08/29/2020 | FirstronicErnst & Young LLP (EY US) announced that John Sammut and Jochen Lipp of Firstronic were named Entrepreneur Of The Year® 2020 Michigan and Northwest Ohio Award finalists.
Firstronic Grand Rapids Facility Recertified to ISO 13485:2016
04/08/2019 | Firstronic LLCElectronics manufacturing services (EMS) provider Firstronic LLC’s Grand Rapids, Michigan facility passed its surveillance audit for ISO 13485:2016, the medical quality standard, and was recertified by Intertek on March 16.
Firstronic Adds Two New Industrial Customers
03/28/2019 | Firstronic LLCFirstronic has been awarded an industrial LED lighting project that involves three power supplies each comprised of a two-PCBA set, potting and a housing, and a PCBA-level industrial control product, comprised of several product families.