-
- News
- Books
Featured Books
- smt007 Magazine
Latest Issues
Current IssueWhat's Your Sweet Spot?
Are you in a niche that’s growing or shrinking? Is it time to reassess and refocus? We spotlight companies thriving by redefining or reinforcing their niche. What are their insights?
Moving Forward With Confidence
In this issue, we focus on sales and quoting, workforce training, new IPC leadership in the U.S. and Canada, the effects of tariffs, CFX standards, and much more—all designed to provide perspective as you move through the cloud bank of today's shifting economic market.
Intelligent Test and Inspection
Are you ready to explore the cutting-edge advancements shaping the electronics manufacturing industry? The May 2025 issue of SMT007 Magazine is packed with insights, innovations, and expert perspectives that you won’t want to miss.
- Articles
- Columns
- Links
- Media kit
||| MENU - smt007 Magazine
Estimated reading time: 2 minutes
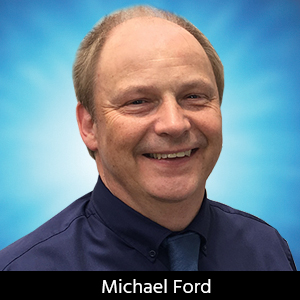
Advanced Digitalization Makes Best Practice, Part 2: Adaptive Planning
In the first part of this series, I examined digital remastering, as it refers to the process of creating the digital product model from design and bill of materials (BOM) information, with conversion then, by digital engineering tools, into execution-ready engineering data. In our new digital MES environment, this process is not just to create a single execution instance for a pre-designated line configuration as was mandated in the past, but for all capable configurations, to provide choice at actual run-time. We now look towards the next step in our new digital factory best practices that digital remastering of engineering data has made possible: the software known as Adaptive Planning, created by Adaptive Insights.
The Challenge of Factory Planning
The dedication of production lines to products, or more recently, groups of products, has become a rather comfortable environment, with just one set of engineering data to support, a single supply-chain of materials, lined up hours in advance, so no concerns for production at all. The flaw in this plan is best illustrated by considering the simplest form of production and having a product running at high-volume on one such dedicated line. Many operations dream about the good ol’ days where such high-volume lines were common and have forgotten that even the operation of those lines were hiding significant losses to the business overall.
Take the case where such a line would make 1,000 products per day, over many days. This is the most efficient example of how SMT equipment automation could be used. It consisted of extremely welloptimized machine programs and carefully balanced lines, where work was split as equally as possible over all machines to get to a single consistent takt time with no losses in between. The 1,000 products would be made, and then disappear into the warehouse. Job done, for SMT. From the business perspective however, unnecessary costs then start to accumulate. It is extremely unlikely that the optimal capacity of the line was exactly meeting the delivery need of the customer. If the customer would take only 900 per day, then 100 additional pieces would have to remain in stock in the factory warehouse. Without careful finished-goods management, the warehouse could soon fill to capacity. The 1,000 per day line capacity was necessary however, as the customer could take the full 1,000 per day or even slightly more. Whenever the assigned warehouse locations became overloaded, the SMT line would be told to stop. Though triggered by a physical threshold, the cost of storage of this “dead” inventory was the significant factor. Often, the SMT line had to stop for just a couple of hours here or there, when the time could be taken advantage of, performing routine maintenance for example, but often, the line would stop for a shift or even longer, getting progressively worse as the fluctuation in customer demand increased.
More Columns from Smart Factory Insights
Smart Factory Insights: Making Rework a Smart Business OpportunitySmart Factory Insights: The Sustainability Gold Rush
Smart Factory Insights: Today’s Manufacturing Jobs Require a New Skill Set
Smart Factory Insights: Compose Yourself, Mr. Ford
Smart Factory Insights: The Smart Business Case for Local PCB Manufacturing
Smart Factory Insights: Manufacturing Digital Twin—Spanners in the Works
Smart Factory Insights: Machines, People, and AI
Smart Factory Insights: Is Sustainability in Manufacturing a Benefit or Burden?