-
-
News
News Highlights
- Books
Featured Books
- smt007 Magazine
Latest Issues
Current IssueWhat's Your Sweet Spot?
Are you in a niche that’s growing or shrinking? Is it time to reassess and refocus? We spotlight companies thriving by redefining or reinforcing their niche. What are their insights?
Moving Forward With Confidence
In this issue, we focus on sales and quoting, workforce training, new IPC leadership in the U.S. and Canada, the effects of tariffs, CFX standards, and much more—all designed to provide perspective as you move through the cloud bank of today's shifting economic market.
Intelligent Test and Inspection
Are you ready to explore the cutting-edge advancements shaping the electronics manufacturing industry? The May 2025 issue of SMT007 Magazine is packed with insights, innovations, and expert perspectives that you won’t want to miss.
- Articles
- Columns
- Links
- Media kit
||| MENU - smt007 Magazine
A New Standard for Standards – From Data to Information
September 7, 2018 | Dr. Glen Thomas, Creative ElectronEstimated reading time: 3 minutes
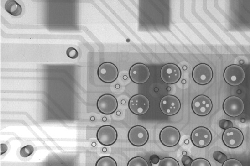
The main challenge we have today with our manufacturing standards is that they are deterministic. For example, for X-ray inspection of BGAs, the standard is a 30% maximum void per ball. This standard determines if a BGA assembly passes or fails. Now, there's nothing to say that a ball with 29% void could not fail and there's also nothing to say that a 31% void in a single ball could not work. It's understandable that for a manufacturing process you need to set some clear parameters to define what's a pass and what's a fail, otherwise it becomes very complicated to set quality standards for a manufacturing process.
Now, it's important to keep in mind that these deterministic thresholds, for example 30% maximum void per ball on BGAs, were developed in a time when collecting data from instruments in a manufacturing line was very costly. And further, contextualization of that data, meaning the process to input all the data that's collected from the individual instruments and inserting that into context, was even more expensive. In some cases, it was technically infeasible.
So, what has changed with Industry 4.0 and other initiatives from equipment manufacturers? The answer is simple: data is more available. Individual instruments are already collecting a lot of data. But that data has not been used or contextualized. Data is getting cheaper. However, data out of context has another name, it’s called noise. Contextualized data, on the other hand, is called information.
At Creative Electron, we're proposing a new perspective on setting pass and fail thresholds in the manufacturing line, based on actual performance and test data, rather than an arbitrarily set number. Instead of setting deterministic numbers, like the 30% void, we would collect data and determine what's a pass and what's a failure. Thus, scrap is minimized, since you only rework or scrap the parts you really need to reject because you know they're likely to fail. What’s more, you gain a greater understanding of where to set the pass or fail parameters.
This, in a way, is what is being done now for QFNs. There's no clear directive for voiding on QFN. So, when asked by our customers, we advise they follow the guidelines of the component manufacturer, based on what works for that specific component and application.
How Does this New Solution Work?
Take the example of a new board with a BGA. With the normal NPI (New Product Introduction) process, you would assemble several boards and would X-ray the BGAs and measure the voids on each one of the balls and check if you are below the 25% or 30% void in each of the balls, depending on the class of product that you are developing.
We propose still collecting the data, but instead of using a simple pass or fail threshold, we suggest testing and using the test data to determine the threshold. So, we collect more and more data to set a dynamic threshold that can move up or down depending on the results we have from real tests. This way we use the actual test data that's available to fine tune our manufacturing thresholds.
There are several test parameters we can use to determine pass or fail in high volume. Going back to our QFN example, if there's a temperature band that the component is supposed to work at, we can place the component and measure with an X-ray system how much voiding we have on the QFM, and using an infrared or laser thermometer, we can determine if the temperature guidance is being followed.
Smart factory solutions are not just about collecting data, they are about using that data intelligently to make faster and better decisions. We think this is a great example of using the data derived throughout the line to create a more efficient and more effective use of X-ray and rework resources.
About Dr. Glen Thomas
Dr. Glen Thomas is a proven veteran in the inspection market with over two decades of experience developing and marketing X-ray systems. Dr. Thomas leads Creative Electron’s lead generation and branding strategy. He also manages the company’s relationship with our domestic and international sales channels. He has been instrumental in helping the company create the best X-ray inspection systems in the world by providing its customers with unrivaled value. Dr. Thomas has held executive leadership positions and was instrument at the growth of companies like Faxitron, Micro Focus Imaging, Radsource Technologies, X-Ray Imaging Solutions, and Lixi.
Dr. Thomas holds a BS in Electrical Engineering and a PhD from the University of Wisconsin in Madison.
Suggested Items
I-Connect007’s Editor’s Choice: Five Must-Reads for the Week
07/04/2025 | Marcy LaRont, I-Connect007For our industry, we have seen several bullish market announcements over the past few weeks, including one this week by IDC on the massive growth in the global server market. We’re also closely watching global trade and nearshoring. One good example of successful nearshoring is Rehm Thermal Systems, which celebrates its 10th anniversary in Mexico and the official opening of its new building in Guadalajara.
Driving Innovation: Direct Imaging vs. Conventional Exposure
07/01/2025 | Simon Khesin -- Column: Driving InnovationMy first camera used Kodak film. I even experimented with developing photos in the bathroom, though I usually dropped the film off at a Kodak center and received the prints two weeks later, only to discover that some images were out of focus or poorly framed. Today, every smartphone contains a high-quality camera capable of producing stunning images instantly.
United Electronics Corporation Advances Manufacturing Capabilities with Schmoll MDI-ST Imaging Equipment
06/24/2025 | United Electronics CorporationUnited Electronics Corporation has successfully installed the advanced Schmoll MDI-ST (XL) imaging equipment at their advanced printed circuit board facility. This significant technology investment represents a continued commitment to delivering superior products and maintaining their position as an industry leader in precision PCB manufacturing.
Orbel Corporation Integrates Schmoll Direct Imaging
06/04/2025 | Schmoll AmericaOrbel Corporation in Easton, PA, proudly becomes the first PCM facility in the U.S. equipped with Schmoll’s MDI Direct Imaging system. This installation empowers Orbel to support customers with greater precision and quality.
Key Insights on Photoresist for Defect Reduction
05/21/2025 | I-Connect007 Editorial TeamIn PCB manufacturing, understanding the intricacies of the photoresist process is crucial for achieving high-quality results. Industry experts Josh Krick, a technical service engineer at IEC, and Tim Blair, a PCB imaging specialist at Tim Blair LLC, share their knowledge on the essential stages of photoresist application, highlight critical advancements in materials, and discuss common defects encountered during production. They share best practices and innovative solutions to enhance the manufacturing process, reduce defects, and ensure efficiency and reliability in high-tech applications.