-
- News
- Books
Featured Books
- design007 Magazine
Latest Issues
Current IssueAll About That Route
Most designers favor manual routing, but today's interactive autorouters may be changing designers' minds by allowing users more direct control. In this issue, our expert contributors discuss a variety of manual and autorouting strategies.
Creating the Ideal Data Package
Why is it so difficult to create the ideal data package? Many of these simple errors can be alleviated by paying attention to detail—and knowing what issues to look out for. So, this month, our experts weigh in on the best practices for creating the ideal design data package for your design.
Designing Through the Noise
Our experts discuss the constantly evolving world of RF design, including the many tradeoffs, material considerations, and design tips and techniques that designers and design engineers need to know to succeed in this high-frequency realm.
- Articles
- Columns
- Links
- Media kit
||| MENU - design007 Magazine
Managing the Challenges of Flex and Rigid-Flex Design
September 12, 2018 | Dave Wiens, Mentor, a Siemens BusinessEstimated reading time: 1 minute
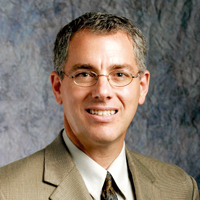
PCB designers working with flex or rigid-flex technology face many potential risks that can derail a project and cause costly design failures. As the name implies, flex and rigid-flex designs comprise a combination of rigid and flexible board technologies made up of multiple layers of flexible circuit substrates, attached internally and/or externally to one or more rigid boards. These combinations provide flexibility for the PCB designer working on dense designs that require a specific form factor. Rigid-flex allows the PCB design team to cost-efficiently apply greater functionality to a smaller volume of space, while providing the mechanical stability required by most applications.
Rigid-flex technology is usually applied when a product needs to be compact, lightweight and/or flexible. Examples of end products where flex and rigid-flex systems are found include smart phones, modern televisions, digital cameras and laptops. As flex and rigid-flex boards are becoming more complex, modern design tools must be able to understand the unique design constructs and rules that surround these designs.
The Key Benefits of Flex and Rigid-Flex
The major benefits of flex and rigid-flex technology implementation and why design teams need to adopt this methodology include:
- Reduced cost and increased reliability by eliminating physical connectors used in the traditional “design-separately-then-assemble” approach to systems design.
- Improved signal integrity through the removal of cross-sectional changes to the conductors (eliminating physical connectors and their associated solder connections).
- Physical space requirement reduction since parts can be placed, and traces can be routed, in three dimensions.
- Improved electromechanical functionality including dynamic bending, vibration and shock tolerance, heat resistance, and weight reduction.
To read this entire article, which appeared in the recent issue of Flex007 Magazine, click here.
Suggested Items
Driving Innovation: Direct Imaging vs. Conventional Exposure
07/01/2025 | Simon Khesin -- Column: Driving InnovationMy first camera used Kodak film. I even experimented with developing photos in the bathroom, though I usually dropped the film off at a Kodak center and received the prints two weeks later, only to discover that some images were out of focus or poorly framed. Today, every smartphone contains a high-quality camera capable of producing stunning images instantly.
Hands-On Demos Now Available for Apollo Seiko’s EF and AF Selective Soldering Lines
06/30/2025 | Apollo SeikoApollo Seiko, a leading innovator in soldering technology, is excited to spotlight its expanded lineup of EF and AF Series Selective Soldering Systems, now available for live demonstrations in its newly dedicated demo room.
Indium Corporation Expert to Present on Automotive and Industrial Solder Bonding Solutions at Global Electronics Association Workshop
06/26/2025 | IndiumIndium Corporation Principal Engineer, Advanced Materials, Andy Mackie, Ph.D., MSc, will deliver a technical presentation on innovative solder bonding solutions for automotive and industrial applications at the Global Electronics A
Fresh PCB Concepts: Assembly Challenges with Micro Components and Standard Solder Mask Practices
06/26/2025 | Team NCAB -- Column: Fresh PCB ConceptsMicro components have redefined what is possible in PCB design. With package sizes like 01005 and 0201 becoming more common in high-density layouts, designers are now expected to pack more performance into smaller spaces than ever before. While these advancements support miniaturization and functionality, they introduce new assembly challenges, particularly with traditional solder mask and legend application processes.
Knocking Down the Bone Pile: Tin Whisker Mitigation in Aerospace Applications, Part 3
06/25/2025 | Nash Bell -- Column: Knocking Down the Bone PileTin whiskers are slender, hair-like metallic growths that can develop on the surface of tin-plated electronic components. Typically measuring a few micrometers in diameter and growing several millimeters in length, they form through an electrochemical process influenced by environmental factors such as temperature variations, mechanical or compressive stress, and the aging of solder alloys.