-
- News
- Books
Featured Books
- design007 Magazine
Latest Issues
Current IssueShowing Some Constraint
A strong design constraint strategy carefully balances a wide range of electrical and manufacturing trade-offs. This month, we explore the key requirements, common challenges, and best practices behind building an effective constraint strategy.
All About That Route
Most designers favor manual routing, but today's interactive autorouters may be changing designers' minds by allowing users more direct control. In this issue, our expert contributors discuss a variety of manual and autorouting strategies.
Creating the Ideal Data Package
Why is it so difficult to create the ideal data package? Many of these simple errors can be alleviated by paying attention to detail—and knowing what issues to look out for. So, this month, our experts weigh in on the best practices for creating the ideal design data package for your design.
- Articles
- Columns
- Links
- Media kit
||| MENU - design007 Magazine
Karl-Heinz Fritz on Cicor’s DenciTec Technology
October 24, 2018 | Nolan Johnson, I-Connect007Estimated reading time: 8 minutes
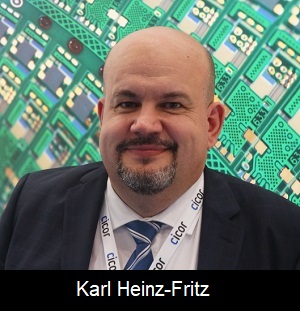
In a recent interview, Karl-Heinz Fritz, VP of technology at Cicor, discusses the business, DenciTec technology, the impact of tariffs on trade, and applications for 3D printing and additive manufacturing, including potential new opportunities for PCB designers.
Nolan Johnson: I am here at PCB West with Karl-Heinz Fritz from Cicor. Can you give us an overview of the company and its role in the PCB industry?
Karl-Heinz Fritz: Cicor is an electronic service company based out of Switzerland. We have two areas of competence. One is electronic services, including plastics, and the other is our Advanced Microelectronics and Substrate (AMS) Division where we do different circuits—high-end PCBs, and thin- and thick-film circuits. Another part of this division is microelectronic assembly, where we do wire and die bonding, and high-precision assembly. We have one of these sites with a clean room assembly line that has been installed to serve the medical market primarily.
Cicor has approximately 2,000 employees and ten manufacturing sites worldwide—four of which are located in Asia (Singapore, China, Vietnam, and Indonesia). The other six are located in Europe, including three in Switzerland, two in Germany, and one in Romania. We mainly serve the industrial, medical, and aerospace markets. However, a small part still works in the Swiss watch industry, which was the root of Cicor when we were founded in 1966.
Johnson: What is your background and role within the company?
Fritz: I'm responsible for technology in the Cicor Group. I have 25 years of experience in electronics manufacturing. I spent most of the time in the PCB business working for several well-known companies in Europe and Asia.
Johnson: Has Cicor been working on any new developments?
Fritz: We have spent a lot of our efforts in development. One thing we did is develop DenciTec technology in the PCB field, which is an ultra-HDI board technology that enables us to produce circuit boards with line widths and spacings down to 25 microns without sacrificing flexibility on interconnections. This means we are still able to achieve copper thicknesses in the range of 20 microns and enables us to use the whole range of interconnection technologies without making any concessions to part reliability and integrity. We also have a technology allowing us to go further into miniaturization and produce line widths and spacings down to less than 10 microns. This is on a much smaller manufacturing unit and panel size using thin-film technology.
Johnson: Are the dimensions starting to decrease where they used to be for semiconductors?
Fritz: Yes. You can say it is a semiconductor process from 20 or 30 years ago.
Johnson: You said you’re getting dimensions around 25 microns with DenciTec. Is that with a rectangular cross-section on the traces?
Fritz: Yes, that's one of the advantages, which is providing proper signaling techniques. We have rectangular traces, not trapezoid-shaped traces.
Johnson: Since you're working in medical and military areas at those sorts of dimensions, do high-speed and impedance factors become an integral part of customers’ designs?
Fritz: Yes. We are very flexible in material selection and adaptive to customers' needs. High-frequency materials have a big range. We are trying to adapt to our customers' needs in that field as well.
Johnson: Concerning thin-film, are your customers primarily driving it or are you ahead of your customers?
Fritz: The pure technology is probably ahead of what the customers need now. Given the size of the manufacturing units, the price is high. What is putting Cicor in a unique position is that we have several different technologies under one roof.
We have specialist sites for each of the technologies, but we are working on merging these technologies. We are talking about making thin-film technology on bigger panel sizes. Even DenciTec will not be good enough at a certain point regarding line width, spacing, and circuit density. We have the knowledge and capability for both technologies in our company.
Further, we are doing bio-compatible circuits on thin-film substrates where we use PCB technologies to laminate, cut, plate, and drill it. This is ongoing, and we’ve found great success. We can also do fully bio-compatible metal systems—such as titanium, gold, and platinum—and deliver a metal system that can be directly in contact with body fluids and tissues.
Johnson: Sounds like a lot of options. With these new technologies and capabilities, what is the profile of the new customers Cicor is targeting?
Fritz: We are targeting big names in the medical industry who have been established in this field for many years. Meanwhile, we are also working with starter companies to help them on their way to launching a product into the market.
Johnson: What design parameters or capabilities would be ideal for DenciTec?
Fritz: To be competitive, given our footprint, our PCB manufacturing site is in Switzerland. We must have specific technical content in or on the circuit boards that we handle. We look at this very carefully. In cases where the technical content is not there, we have to stop very early in the process. Being honest with our customer about if it’s not something we can do out of Switzerland is very important to us. Our sweet spot in PCB manufacturing is flex multilayer circuits. Anything less than four-mils line width and spacing.
Johnson: I presume that ties back to medical applications, correct?
Fritz: Yes, this includes several medical applications, such as permanent and temporary implants, sensors, and catheters. That's one of our sweet spots. The majority of our thin- and thick-film circuits is done on ceramic materials for aerospace and bionic applications.
Page 1 of 2
Suggested Items
Copper Price Surge Raises Alarms for Electronics
07/15/2025 | Global Electronics Association Advocacy and Government Relations TeamThe copper market is experiencing major turbulence in the wake of U.S. President Donald Trump’s announcement of a 50% tariff on imported copper effective Aug. 1. Recent news reports, including from the New York Times, sent U.S. copper futures soaring to record highs, climbing nearly 13% in a single day as manufacturers braced for supply shocks and surging costs.
I-Connect007 Editor’s Choice: Five Must-Reads for the Week
07/11/2025 | Andy Shaughnessy, Design007 MagazineThis week, we have quite a variety of news items and articles for you. News continues to stream out of Washington, D.C., with tariffs rearing their controversial head again. Because these tariffs are targeted at overseas copper manufacturers, this news has a direct effect on our industry.I-Connect007 Editor’s Choice: Five Must-Reads for the Week
Digital Twin Concept in Copper Electroplating Process Performance
07/11/2025 | Aga Franczak, Robrecht Belis, Elsyca N.V.PCB manufacturing involves transforming a design into a physical board while meeting specific requirements. Understanding these design specifications is crucial, as they directly impact the PCB's fabrication process, performance, and yield rate. One key design specification is copper thieving—the addition of “dummy” pads across the surface that are plated along with the features designed on the outer layers. The purpose of the process is to provide a uniform distribution of copper across the outer layers to make the plating current density and plating in the holes more uniform.
Trump Copper Tariffs Spark Concern
07/10/2025 | I-Connect007 Editorial TeamPresident Donald Trump stated on July 8 that he plans to impose a 50% tariff on copper imports, sparking concern in a global industry whose output is critical to electric vehicles, military hardware, semiconductors, and a wide range of consumer goods. According to Yahoo Finance, copper futures climbed over 2% following tariff confirmation.
Happy’s Tech Talk #40: Factors in PTH Reliability—Hole Voids
07/09/2025 | Happy Holden -- Column: Happy’s Tech TalkWhen we consider via reliability, the major contributing factors are typically processing deviations. These can be subtle and not always visible. One particularly insightful column was by Mike Carano, “Causes of Plating Voids, Pre-electroless Copper,” where he outlined some of the possible causes of hole defects for both plated through-hole (PTH) and blind vias.