-
- News
- Books
Featured Books
- smt007 Magazine
Latest Issues
Current IssueWhat's Your Sweet Spot?
Are you in a niche that’s growing or shrinking? Is it time to reassess and refocus? We spotlight companies thriving by redefining or reinforcing their niche. What are their insights?
Moving Forward With Confidence
In this issue, we focus on sales and quoting, workforce training, new IPC leadership in the U.S. and Canada, the effects of tariffs, CFX standards, and much more—all designed to provide perspective as you move through the cloud bank of today's shifting economic market.
Intelligent Test and Inspection
Are you ready to explore the cutting-edge advancements shaping the electronics manufacturing industry? The May 2025 issue of SMT007 Magazine is packed with insights, innovations, and expert perspectives that you won’t want to miss.
- Articles
- Columns
- Links
- Media kit
||| MENU - smt007 Magazine
Alpha Assembly Solutions on Training, Education, and Low-Temperature Soldering
November 7, 2018 | I-Connect007 Editorial TeamEstimated reading time: 17 minutes
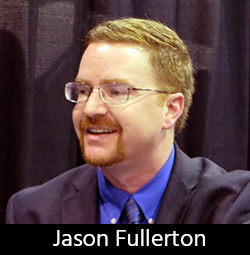
In this interview from SMTA International 2018, Jason Fullerton of Alpha Assembly Solutions discusses the benefits and challenges of low-temperature soldering. He also highlights the biggest concerns he’s currently seeing in the industry, including young engineers lacking hands-on manufacturing experience and training, voiding and head-in-pillow issues, and low-temperature soldering demands. Barry Matties and Happy Holden also spoke with Jason about the difficulties surrounding each of these trends and how Alpha is helping their customer base to best combat these issues.
Barry Matties: Jason, can you tell us a little about Alpha Assembly Solutions for our readers?
Jason Fullerton: We're one of the market’s leading providers of metals, chemicals, and materials for soldering and assembly. We specialize in metallurgy and alloys, solder pastes, fluxes, solder preforms, and core wires. We also have an advanced materials division that works more on semiconductor fabrication and solder alloys for those applications as well.
My title is a Customer Technical Support Engineer. I'm basically a field service engineer for Alpha and a soldering process engineer by trade. I spent 15 years working in factories using products from Alpha and other companies as an engineer running the assembly processes. Our role at Alpha is to help our customers use our products by providing a resource that's walked a mile in their shoes and can advocate for them within the organization. We understand the challenges they face because we used to meet the same challenges back when we were in engineers working for a living.
Matties: That's a great background to have in this particular role because as you said, you've been in their shoes. What are the most common issues that your customers come to you with that they need to be solved?
Fullerton: The biggest issue I see in the industry right now is an influx of younger engineers that don't have the background and training in techniques and technology that we use in electronics today. There's a large training issue now, especially with startup and smaller companies that don't have the budget to hire experienced engineers. They bring engineers in and expect them to learn on the job, and they make basic mistakes along the way. Then, people like me come in with their supply base to help them prevent those kinds of mistakes.
One of the things we like to do is provide training to our customers. I do a “solder paste 101” training on the very basics of the solder materials. There are other sessions on advanced printing, wave solder troubleshooting, and the importance of reflow technology. The lack of training and education in the United States to teach people how to solder and be process engineers in this industry is a big issue.
Matties: Is there a large interest for people to be in this role, or is it something that they stumble into?
Fullerton: A little bit of both. The people who have an interest in it gravitate towards universities that have programs for this.
Matties: That's what I was thinking, so you're dealing with people who stumbled into this career.
Fullerton: A lot of times, yes. I'm a manufacturing engineer by degree but I stumbled into electronics assembly at the start of my career. All throughout my career, I've worked with people who have a degree in electrical or mechanical engineering, and then one day they’re told to be a process engineer—"That's your new job. You're going to learn how to solder, coat, or use adhesives, and apply them in an advanced production process.” However, their educational background doesn't prepare them adequately for that, and so they have to learn on the job as they go. This lack of background knowledge usually leads to a lot of mistakes.
Matties: When you say you're shifting your effort around education, are training sessions offered online or do you visit in person?
Fullerton: Typically, in person because we want to observe their processes and ensure the training is relevant to their specific needs. Part of my methodology is to do what I call the “book learning” to start. We go in with a PowerPoint, talk about the technology, and then take the group out to the production line and apply that hands-on experiential learning so we can reinforce what we address in training.
Matties: Is this something that you're formalizing or is it more on a case-by-case basis?
Fullerton: It's semi-formalized. We have standard PowerPoint presentations and programs we offer to our customers. Many times, these meet their needs, but if a customer—especially a key customer—comes to us with a specific need for education, we'll develop new materials around that particular question or set of topics that they're interested in.
Matties: This is a value-add that you bring to your customers.
Fullerton: You took the words out my mouth. Our role in the company is not to charge our customers to do new things; our customers get access to this level of support and expertise for being an Alpha customer.
Matties: Aside from the training, what other sorts of problems does your team encounter most frequently?
Fullerton: One of the most popular ones we see nowadays is voiding. If you walk around this show, you'll see every soldering company has a voiding display, panel, or marketing representation because that's a big challenge in the industry—both how to prevent and mitigate the effects of voiding solder joints, and how to better understand the impact of those voids on the reliability of the solder joints themselves.
Matties: It's an ongoing issue with no solution?
Fullerton: There are solutions, but they are not easy or obvious. The answer isn’t to simply change your solder paste or modify your reflow profile; it's more complicated than that. Thus, voiding solutions aren't just a single product. As a company, we offer a service to our customers called “Void Reduction Solutions” where we essentially form a cross-functional engineering consulting team within our organization to assess the current efforts that the customer has made toward their voiding problems—where they have gotten to at this point, their objectives, and holistically looking at the entire system from stencil design, to the interaction of board surface finish materials, solder pastes, and the actual solder paste application process. These are the kinds of things we will take and try to identify what can be improved in their operation to reduce the impact of voiding on the solder paste they need.
Page 1 of 3
Suggested Items
Driving Innovation: Direct Imaging vs. Conventional Exposure
07/01/2025 | Simon Khesin -- Column: Driving InnovationMy first camera used Kodak film. I even experimented with developing photos in the bathroom, though I usually dropped the film off at a Kodak center and received the prints two weeks later, only to discover that some images were out of focus or poorly framed. Today, every smartphone contains a high-quality camera capable of producing stunning images instantly.
Hands-On Demos Now Available for Apollo Seiko’s EF and AF Selective Soldering Lines
06/30/2025 | Apollo SeikoApollo Seiko, a leading innovator in soldering technology, is excited to spotlight its expanded lineup of EF and AF Series Selective Soldering Systems, now available for live demonstrations in its newly dedicated demo room.
Indium Corporation Expert to Present on Automotive and Industrial Solder Bonding Solutions at Global Electronics Association Workshop
06/26/2025 | IndiumIndium Corporation Principal Engineer, Advanced Materials, Andy Mackie, Ph.D., MSc, will deliver a technical presentation on innovative solder bonding solutions for automotive and industrial applications at the Global Electronics A
Fresh PCB Concepts: Assembly Challenges with Micro Components and Standard Solder Mask Practices
06/26/2025 | Team NCAB -- Column: Fresh PCB ConceptsMicro components have redefined what is possible in PCB design. With package sizes like 01005 and 0201 becoming more common in high-density layouts, designers are now expected to pack more performance into smaller spaces than ever before. While these advancements support miniaturization and functionality, they introduce new assembly challenges, particularly with traditional solder mask and legend application processes.
Knocking Down the Bone Pile: Tin Whisker Mitigation in Aerospace Applications, Part 3
06/25/2025 | Nash Bell -- Column: Knocking Down the Bone PileTin whiskers are slender, hair-like metallic growths that can develop on the surface of tin-plated electronic components. Typically measuring a few micrometers in diameter and growing several millimeters in length, they form through an electrochemical process influenced by environmental factors such as temperature variations, mechanical or compressive stress, and the aging of solder alloys.