-
- News
- Books
Featured Books
- smt007 Magazine
Latest Issues
Current IssueSupply Chain Strategies
A successful brand is built on strong customer relationships—anchored by a well-orchestrated supply chain at its core. This month, we look at how managing your supply chain directly influences customer perception.
What's Your Sweet Spot?
Are you in a niche that’s growing or shrinking? Is it time to reassess and refocus? We spotlight companies thriving by redefining or reinforcing their niche. What are their insights?
Moving Forward With Confidence
In this issue, we focus on sales and quoting, workforce training, new IPC leadership in the U.S. and Canada, the effects of tariffs, CFX standards, and much more—all designed to provide perspective as you move through the cloud bank of today's shifting economic market.
- Articles
- Columns
- Links
- Media kit
||| MENU - smt007 Magazine
Estimated reading time: 4 minutes
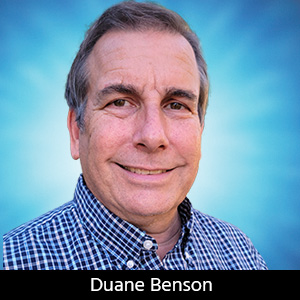
Top 5 Things to Know When Moving from Hand Assembly to Robotic Assembly
A lot of factors go into the decision to hand build or outsource circuit boards. I hand-build my own sometimes simply because I enjoy the challenge. Of course, most of the projects I design are for my own use, so timeliness isn’t that important.
When I do design something that will go out to a customer—like my electronic business card holder—I will send the board through our shop. In those cases, quality and delivery are critical, and the quantity is often too high to hand-build. Machine building also allows me to use smaller and more complex parts.
That same decision—to hand-build or outsource—takes place in the heads of designers all over the country. When the decision is to outsource, there are a few important things to consider. Some things that work fine when hand soldering may stand in the way of quality, repeatability, and reliability when machine assembling.
Here are five of the most important considerations when changing from hand-build to outsourced:
1. Use Solder Mask and Silkscreen
A good solder joint needs the correct amount of solder in the right place. Solder will tend to flow down bare copper, bleeding outside of the area it belongs, and down exposed copper traces and vias. The main purpose of solder mask is to keep the solder where it belongs. It also protects the traces, but that’s a longevity issue. Solder bleeding is a manufacturing and reliability issue, which isn’t a problem when hand soldering. In fact, it can even work to your advantage when hand soldering very small parts. It gives you more room for your soldering iron to hit metal, but not so with solder paste and machine assembly. Use solder mask.
2. Avoid the Pseudo Panel
Keeping small boards in a panel is the recommended best practice in the manufacturing industry. We appreciate it, and while not always necessary, can reduce your costs. We sometimes see what we call a “pseudo panel.” This is a board where multiples of the board are put in the same PCB—like a panel—but unlike a panel, the boards don’t have routing or V-score between them. Sometimes, the designer will put a bunch of vias to outline the board, or just ask that we use a bandsaw to separate them. That’s a time consuming, expensive, and a potentially damaging process. The vibration of the saw can crack solder joints, and you’re unlikely to get boards that are all the same size. Have small boards panelized by your board house.
3. Family Panel—Pseudo or Not
Similar to the pseudo panel is the family panel. A family panel is a case where a project is made up of several different PCBs, and they are all laid out together as though they are one design. If the board is not routed between the designs, you’ll have the pseudo-panel problem as previously described.
However, the bigger problem comes with reference designators. We typically see family panels with duplicate reference designators. For example, each design will have its own C1, R1, Q1, etc. We use the reference designators as position identifiers. If you have three different parts labeled R5, our machine programmers will have a problem with it. It’s even worse if the values differ; on one design, C1 is a 0.1-µF capacitor, while on another design, it's a 22-pF capacitor.
If you’re making a family panel, give every placement a different reference designator. One way is to use extra digits. For example, one design on the family panel could have C100, C101, C102, etc. The next would be C200, C201, C203, and so on. Also, don’t forget the routing or V-score between the designs.
4. Quad-flat No-leads (QFN)—Hole in the Middle
A common technique in the hand soldering world for soldering QFNs and other parts with thermal pads underneath is to put a big via in the middle of the center pad. By doing so, you can stick a soldering iron and some solder down through the hole and get a good solder connection on the bottom pad. However, this doesn’t work with machine assembly. The solder paste will flow down and out the hole in the reflow oven. You’ll end up with a poor connection—or no connection—to the thermal pad, and solder will slop on the back side of the board.
5. Parts and the Bill of Materials (BOM)
When I build my hobby projects, I often get a bit carefree with the BOM. It’s not good practice, but I do. I’ll put a part in the BOM that I used before and not check to see if it’s still in stock. I’ll put parts in the BOM with just the values and not any part numbers. Things of that sort require tribal knowledge, which only the designer has.
When building, sometimes I’ll just grab a part that’s close. If I need a 0805 1-µF 10-V capacitor, I can grab one that’s 16 V, 25 V, etc. I can even make a 0603 part work. As the designer, you may know that something close will work, but an outside house might not. You need to tell them exactly what the part is.
Before sending anything through our shop, I clean up the BOM. In order for us, or any manufacturer, to build the boards, the BOM needs:
- A unique reference designator for each part placement
- The quantity of each part used on the board
- The manufacturer
- The manufacturer’s part number (DigiKey part numbers can be used as well)
The transition from hand-built to outsourced machine building can be an intimidating one. But, with a few considerations, it can be an easy and rewarding transition.
Duane Benson is chief technology champion at Screaming Circuits. To read past columns or contact Benson, click here.
More Columns from Powerful Prototypes
Powerful Prototypes: Small Computer ModulesPowerful Prototypes: A Trip Back to the Basics
Powerful Prototypes: The Work World in 2021
Powerful Prototypes: Why Datasheets Matter
Powerful Prototypes: Manufacturing in an Uncertain World
Powerful Prototypes: An Open-Source Adventure
Powerful Prototypes: Five Technological Shifts in the New Decade
Powerful Prototypes: Cost Reduction in Design