-
-
News
News Highlights
- Books
Featured Books
- smt007 Magazine
Latest Issues
Current IssueWhat's Your Sweet Spot?
Are you in a niche that’s growing or shrinking? Is it time to reassess and refocus? We spotlight companies thriving by redefining or reinforcing their niche. What are their insights?
Moving Forward With Confidence
In this issue, we focus on sales and quoting, workforce training, new IPC leadership in the U.S. and Canada, the effects of tariffs, CFX standards, and much more—all designed to provide perspective as you move through the cloud bank of today's shifting economic market.
Intelligent Test and Inspection
Are you ready to explore the cutting-edge advancements shaping the electronics manufacturing industry? The May 2025 issue of SMT007 Magazine is packed with insights, innovations, and expert perspectives that you won’t want to miss.
- Articles
- Columns
- Links
- Media kit
||| MENU - smt007 Magazine
Estimated reading time: 13 minutes
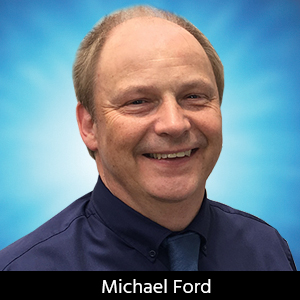
Resolving the Productivity Paradox
Many overlooked this as the focus on machine program optimization had changed once the effects of higher mix came in; it became all about the changeover time. However, in many scenarios, as time went on, the losses in the programs exceeded those avoided in the changeover process. This lost productivity due to reduced program efficiency was almost never included in the productivity reports. Throughput performance was simply measured against the machine program time. Invisible losses like these started to become an increasingly common part of the regular high-mix production paradigm.Production planning is another black hole example of lost productivity where fixed production configuration assignment rules for product allocation to line configurations by engineers have to be followed due to the sheer time and effort needed to prepare product data, thereby significantly restricting the optimization process. Generic legacy scheduling tools are useless in this environment. In reality, production is mainly scheduled utilizing Excel as a just-in-time (JIT) planning tool; no one has time to think about whether more optimized production allocation plans could be made.
The associated losses of opportunity continue to increase due to these kinds of problems, many of which are hidden and not reported due to the narrow focus of individual operations and lack of overall visibility. Productivity reports made from each perspective look good on the shop floor and everyone is making an excellent effort, but if you step back and look at the bigger picture, the overall result is going in the wrong direction, which is exactly what the German reports are highlighting. The realization of this is a good thing because even if the numbers themselves are very poor, without this information, there is no opportunity to investigate and improve. In the meantime, it is fine to continue to measure the internal performance of each element within manufacturing with the current metrics and key performance indicators (KPIs); one should not replace the other.
However, what the German reports don’t offer is a solution to this issue. From a high-level perspective, the situation is complex and bewildering with numerous variables and barriers, many of which are buried in the technical detail of operations. Discovery of hidden issues—as well as the consequences of actions taken—are very difficult to understand, never mind quantify. To start to gain a sense of it all, there are two main things to address.
The first is to understand the real need of the business—both current and future. For example, in Germany, the most active sector of the industry is automotive. The pride of German automotive assembly lines has a final production assembly line running at a fixed takt rate like a heartbeat delivering cars reliably and on time every time. The line is also fully flexible and capable of making any of the millions of combinations of options and features that any customer could require. It all sounds good and appears to be a supreme achievement of automation, which includes human activity.
However, if you focus away from the final line operation, it is possible to see the damage that the assembly-line operation is causing. Looking downstream, we see that the factory still has to make sure that the total demand for the family of cars that each line produces exactly meets the customer demand, so as not to create a buildup of finished goods stock. There is no scope for the line to make any model changeover. Sales and marketing will create campaigns and incentives in the market to drive a constant factory demand, but even so, making to customer order has to be mixed with some standard builds to keep the line running continuously, which are often sold at a discount.
One would imagine that if you ordered a new car in this situation—even with a bespoke set of features—it could be made quite rapidly, as it is clearly shown that just a couple of days lead time in the factory is all that is required. Instead, the reality of the situation is that the waiting time for a production slot can be many months. People tend to want to look elsewhere for their cars when faced with this ordering lead time. The reason for the long lead time is the planning that goes into the final assembly line.
To ensure that it never stops, there is a buffer of orders upfront. This is needed JIT to give the forecast of demand for subassembly options and configurations to be supplied to the factory. The cost of flexibility is simply being passed upstream. Suppliers to automotive final assembly lines receive a somewhat variable production demand, often volatile, with which they have to comply. Delivery must occur within a specific window—no sooner, and certainly no later. Optimization of the subassembly factory operations represents the worst-case scenario in the industry. Safety-critical assemblies require in-depth quality, process, and engineering management. With a high mix and often small work-order quantities, changes are continuously required in the factory flow with each configuration change needing to be qualified against the required standards. There is little compensation for this, as the pricing in automotive is very sensitive indeed.
Page 2 of 3
More Columns from Smart Factory Insights
Smart Factory Insights: Making Rework a Smart Business OpportunitySmart Factory Insights: The Sustainability Gold Rush
Smart Factory Insights: Today’s Manufacturing Jobs Require a New Skill Set
Smart Factory Insights: Compose Yourself, Mr. Ford
Smart Factory Insights: The Smart Business Case for Local PCB Manufacturing
Smart Factory Insights: Manufacturing Digital Twin—Spanners in the Works
Smart Factory Insights: Machines, People, and AI
Smart Factory Insights: Is Sustainability in Manufacturing a Benefit or Burden?