-
-
News
News Highlights
- Books
Featured Books
- smt007 Magazine
Latest Issues
Current IssueMoving Forward With Confidence
In this issue, we focus on sales and quoting, workforce training, new IPC leadership in the U.S. and Canada, the effects of tariffs, CFX standards, and much more—all designed to provide perspective as you move through the cloud bank of today's shifting economic market.
Intelligent Test and Inspection
Are you ready to explore the cutting-edge advancements shaping the electronics manufacturing industry? The May 2025 issue of SMT007 Magazine is packed with insights, innovations, and expert perspectives that you won’t want to miss.
Do You Have X-ray Vision?
Has X-ray’s time finally come in electronics manufacturing? Join us in this issue of SMT007 Magazine, where we answer this question and others to bring more efficiency to your bottom line.
- Articles
- Columns
Search Console
- Links
- Media kit
||| MENU - smt007 Magazine
Estimated reading time: 13 minutes
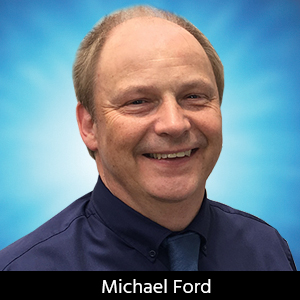
Resolving the Productivity Paradox
A typical automotive subassembly provider needs to be aware of these constraints of doing business and create a production model that is optimized and developed in a way that all of the hidden losses are exposed and addressed as a part of the model. The same process applies to all types and sectors of electronics and assembly manufacturing in general. However, creating the optimum operation is not as simple as it used to be. Industry 4.0 was created to address these new operational paradigms, the software-based automation layer above the increasing number of automated processes that the older Industry 3.0 represents. The German reports are looking for Industry 4.0 results, but are based on Industry 3.0 activities. It is time to create some real tools for Industry 4.0, which is the second thing that needs to be addressed.Industry 4.0 is the optimization of every aspect of the manufacturing process through the use of live data. The solution for each factory taking Industry 4.0 on board is going to be a little different depending on the business need, whether this is lines of machines talking to each other, managing Lean materials, adaptive planning, assignment of products to line configurations, or digital twin-based assembly process engineering. However, it is not practical to develop individual bespoke Industry 4.0 software that would drive these factory processes because the cost quickly becomes prohibitive and non-sustainable.
Standardization needs to happen at a level that promotes the use of standard digital platforms that deliver values based on the use of Industrial Internet of Things (IIoT) technology specifically for manufacturing. This technology is a distinct paradigm shift from legacy data collection. Through the inclusion of data flow between every operational process, a live, digital, and detailed holistic view of the shop floor, with a scope that is inclusive of every manufacturing and dependent event and has a deep and well-defined level of detail is available at all times. Unacknowledged losses are no longer out of sight and can be included in any activity related to performance improvement, optimization, and operational decision-making all in line with the goals of Industry 4.0. Effects of decisions made and changes executed can be seen, measured, and continuously refined, and in this case, directly contribute to the overall productivity of the factory.
At IPC APEX EXPO 2018, we saw the world’s first demonstration of the Connected Factory Exchange (CFX). Though machine communication is nothing new, the fact that key metrics and data from any type of machine from any vendor could be viewed on demand by visitors on their mobile phones without any installation or configuration of software was an eye-opener. The barriers of having different communication methods—as well as different levels of data content from machines—had been eliminated.
One year later at IPC APEX EXPO 2019, we look forward to seeing the published CFX standard in action in terms of the scope and depth of communication now supported, gathering data for use in dashboards, AI decision-making, and factory optimization. Whatever the software tools of choice are for manufacturing, the ability to have visibility of the status and performance of every event that takes place on the factory floor provides the opportunity to see and understand exactly where time and opportunities are being lost.
Software tools at the factory level can then utilize this information to optimize the entire factory in real time. Machine vendors also have the opportunity to get significantly more data about the environment in which their machines are working through seeing materials and planning information with which to further automatically optimize their machine operations. As a standard based on true industry consensus, CFX has been designed to provide information about all areas of opportunity, control, and management in the factory.
CFX is the definition of how data is exchanged and the exact language and meaning of that data. The adoption of CFX is now being made into software tools provided by machine vendors on the machine or line level, as well as by solution providers across the whole factory. The paradigm of manufacturing execution systems (MES) changes as a result. Legacy MES systems that simply gather data save it into a series of databases and then provide reports are not going to be up to the challenge of processing IIoT data in real time; thus, they will be limited when it comes to live optimization and decision-making support.
A new breed of digital MES systems specifically designed for the IIoT and CFX environment deliver the most value, spanning the whole gamut of factory operations and offering a single standard digital platform. For example, bespoke extensions to the platform to support specialized reporting and monitoring—as well as the inclusion of product-specific processes such as functional test—can easily be added by local IT developers by creating the required CFX interface and utilizing the free IPC CFX software development kit (SDK).
The technology shown by the many participating vendors at IPC APEX EXPO 2019 represents the key turning point to reverse the productivity paradox and enable new automation management techniques and digital best practices that address the long-standing hidden, ignored, or unavoidable causes of lost productivity. Full visibility and control of even the most complex of factory operations for engineers and managers are restored, providing the intelligence with which to identify and eliminate causes of losses. This provides an opportunity for increased flexibility whilst also increasing productivity, quality, on-time delivery, and a reduction of material-related costs.
Though the demonstration of CFX—together with the IPC Hermes Standard (which replaces SMEMA)—at IPC APEX EXPO 2019 is limited in scope due to the nature of an unconnected manufacturing line working live in a trade show environment, the fundamentals will be on display from machine vendors. The latest CFX-enabled MES software tools and experts will be on hand to demonstrate and explain how the use of CFX technology can bring an end to this productivity paradox. I look forward to meeting you there.
Page 3 of 3More Columns from Smart Factory Insights
Smart Factory Insights: Making Rework a Smart Business OpportunitySmart Factory Insights: The Sustainability Gold Rush
Smart Factory Insights: Today’s Manufacturing Jobs Require a New Skill Set
Smart Factory Insights: Compose Yourself, Mr. Ford
Smart Factory Insights: The Smart Business Case for Local PCB Manufacturing
Smart Factory Insights: Manufacturing Digital Twin—Spanners in the Works
Smart Factory Insights: Machines, People, and AI
Smart Factory Insights: Is Sustainability in Manufacturing a Benefit or Burden?