-
- News
- Books
Featured Books
- design007 Magazine
Latest Issues
Current IssueShowing Some Constraint
A strong design constraint strategy carefully balances a wide range of electrical and manufacturing trade-offs. This month, we explore the key requirements, common challenges, and best practices behind building an effective constraint strategy.
All About That Route
Most designers favor manual routing, but today's interactive autorouters may be changing designers' minds by allowing users more direct control. In this issue, our expert contributors discuss a variety of manual and autorouting strategies.
Creating the Ideal Data Package
Why is it so difficult to create the ideal data package? Many of these simple errors can be alleviated by paying attention to detail—and knowing what issues to look out for. So, this month, our experts weigh in on the best practices for creating the ideal design data package for your design.
- Articles
- Columns
- Links
- Media kit
||| MENU - design007 Magazine
3DEM Modeling: Influence of Metal Plating on PCB Channel Loss and Impedance
March 21, 2019 | Chang Fei Yee, Keysight TechnologiesEstimated reading time: 1 minute
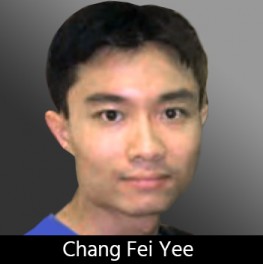
This article briefly introduces different types of metal plating commonly used in PCB fabrication. Subsequently, the influence of metal plating on PCB channel loss (i.e., insertion loss or S21) and impedance (i.e., time domain reflectometry or TDR) is studied with 3DEM modeling using Keysight EMPro.
Introduction
Metal plating that serves as a protective layer is applied on top of the copper traces during PCB fabrication, thus alleviating the oxidation process of the copper. Common finishes include immersion silver (IAg), electroless nickel immersion gold (ENIG), etc. With immersion silver, nearly pure silver (i.e., ~0.02 mils in thickness) is coated over the copper traces on a PCB. Meanwhile, with ENIG, nickel (i.e., ~0.2 mils in thickness) is deposited on the copper trace followed by a coating of gold (i.e., ~0.01 mils in thickness) on top. Nickel serves as a barrier layer to prevent the migration of gold into the base copper.
However, metal plating comes with disadvantages. On a PCB, the current of the signal tends to propagate more closely to the surface of the trace when the frequency of the signal becomes higher. Skin depth is the parameter that determines how extensive the current of signal travels with reference to the surface of the transmission channel. The relationship between skin depth and signal frequency is governed by Equation 1. For instance, at frequency 10 GHz, skin depth becomes 0.026 mils.
Equations 2, 3, and 4 indicate that attenuation of the signal is inversely proportional to the metal conductivity. Once metal with lower conductivity is coated over a copper trace, the signal experiences a larger amount of attenuation. For instance, skin depth becomes 0.026 mils at a signal frequency of 10 GHz. If ENIG plating (i.e., base copper 1.09 mils, nickel 0.2 mils in the mid layer, and gold 0.01 mils on top) is applied, the high-frequency signal will propagate on the gold and nickel-plated layers. This signal will encounter a larger magnitude of attenuation due to the lower conductivity of nickel.
To read this entire article, which appeared in the February 2019 issue of Design007 Magazine, click here.
Suggested Items
Copper Price Surge Raises Alarms for Electronics
07/15/2025 | Global Electronics Association Advocacy and Government Relations TeamThe copper market is experiencing major turbulence in the wake of U.S. President Donald Trump’s announcement of a 50% tariff on imported copper effective Aug. 1. Recent news reports, including from the New York Times, sent U.S. copper futures soaring to record highs, climbing nearly 13% in a single day as manufacturers braced for supply shocks and surging costs.
I-Connect007 Editor’s Choice: Five Must-Reads for the Week
07/11/2025 | Andy Shaughnessy, Design007 MagazineThis week, we have quite a variety of news items and articles for you. News continues to stream out of Washington, D.C., with tariffs rearing their controversial head again. Because these tariffs are targeted at overseas copper manufacturers, this news has a direct effect on our industry.I-Connect007 Editor’s Choice: Five Must-Reads for the Week
Digital Twin Concept in Copper Electroplating Process Performance
07/11/2025 | Aga Franczak, Robrecht Belis, Elsyca N.V.PCB manufacturing involves transforming a design into a physical board while meeting specific requirements. Understanding these design specifications is crucial, as they directly impact the PCB's fabrication process, performance, and yield rate. One key design specification is copper thieving—the addition of “dummy” pads across the surface that are plated along with the features designed on the outer layers. The purpose of the process is to provide a uniform distribution of copper across the outer layers to make the plating current density and plating in the holes more uniform.
Trump Copper Tariffs Spark Concern
07/10/2025 | I-Connect007 Editorial TeamPresident Donald Trump stated on July 8 that he plans to impose a 50% tariff on copper imports, sparking concern in a global industry whose output is critical to electric vehicles, military hardware, semiconductors, and a wide range of consumer goods. According to Yahoo Finance, copper futures climbed over 2% following tariff confirmation.
Happy’s Tech Talk #40: Factors in PTH Reliability—Hole Voids
07/09/2025 | Happy Holden -- Column: Happy’s Tech TalkWhen we consider via reliability, the major contributing factors are typically processing deviations. These can be subtle and not always visible. One particularly insightful column was by Mike Carano, “Causes of Plating Voids, Pre-electroless Copper,” where he outlined some of the possible causes of hole defects for both plated through-hole (PTH) and blind vias.