-
- News
- Books
Featured Books
- smt007 Magazine
Latest Issues
Current IssueWhat's Your Sweet Spot?
Are you in a niche that’s growing or shrinking? Is it time to reassess and refocus? We spotlight companies thriving by redefining or reinforcing their niche. What are their insights?
Moving Forward With Confidence
In this issue, we focus on sales and quoting, workforce training, new IPC leadership in the U.S. and Canada, the effects of tariffs, CFX standards, and much more—all designed to provide perspective as you move through the cloud bank of today's shifting economic market.
Intelligent Test and Inspection
Are you ready to explore the cutting-edge advancements shaping the electronics manufacturing industry? The May 2025 issue of SMT007 Magazine is packed with insights, innovations, and expert perspectives that you won’t want to miss.
- Articles
- Columns
- Links
- Media kit
||| MENU - smt007 Magazine
Electrolube Launches Next-Gen UV Cure Coatings at SMTConnect
April 2, 2019 | ElectrolubeEstimated reading time: 4 minutes
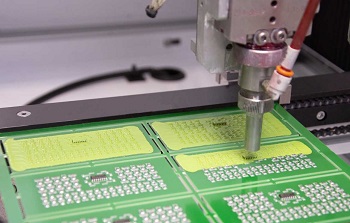
Seven next generation UV cure conformal coating products will be launched for the first time in Europe at the SMTConnect show In Nuremberg, hosted at the Nurnberg Messe from May 7-9, 2019. Electrolube developed the exciting new UVCL range to meet the various requirements of electronics, LED and automotive manufacturers, with the additional benefit of rapidly increasing production time and offering even higher levels of performance. The new UV Cure range will be showcased in Hall 4, stand 339, where Electrolube’s senior technical team will be available to discuss the advantages and specifications of the new UV cure coating range.
The UVCL range is solvent-free, VOC-free and provides unsurpassed performance in harsh environments, including resistance to cracking during thermal shock cycling. The main benefit of Electrolube’s UV Cure coatings is that boards can be handled immediately, with full cure guaranteed within 6-12 hours due to the chemical secondary cure mechanism. In comparison to existing UV cure systems on the market, the majority require minimum moisture secondary cure times of 8-14+ days, whereas the new UVCL range facilitates tremendous reductions in the amount of Work In Progress.
The range features UVCL, a single component, medium-low viscosity dual cure coating with secondary moisture cure, for complete cure in shadow areas. Available in 5L packaging, UVCL is VOC-free, non-flammable and demonstrates excellent electrical properties. The coating provides a wide operating temperature range and is ready to use for selective spray application.
UVCL-P is the Plus version of UVCL. It is a transparent, flexible coating which is extremely resistant to thermal shock. The main benefits of UVCL-P are the improved coverage and protection achieved, along with a guaranteed chemical cure in 6 hours thanks to its unique secondary cure mechanism. Selectively applied at 50-150 microns thickness, the plus version will always afford a higher level of condensation protection than UVCL when sprayed at the same thickness. UVCL-P has a higher maximum operating temperature of 150°C and meets the requirements of UL94V-0 at thicknesses below 150 microns and can be cured with either 365nm LED lamps or ‘D’ bulb microwave technology.
Electrolube have also developed an ‘xtra’ version of UVCL, called UVCL-X, which shares the benefits of UVCL-P with excellent resistance to thermal shock, immediate board handling with a guaranteed chemical cure in 6 hours thanks to the unique secondary chemical cure mechanism and exceptional coverage and protection. Reflecting its environmental credentials as well as increasing the ease of inspection, UVCL-X is a green-opaque coating that can be applied at up to 300 microns and has a higher maximum operating temperature of 150°C. It is a highly flexible coating that demonstrates excellent thermal conductivity 0.7 Wm-1K-1 for significantly improved heat dissipation. The coating is also UL746 qualified and meets the requirements of UL94V-0 at thicknesses below 300 microns.
Further UV Cure coating products will be launched at the show and include a brand new film coating product, UVCL-FC, which enables the application of even thinner coatings and faster curing line speeds. UVCL-FC is a low viscosity, fast-curing UV formulation for rapid processing. The company will also showcase a new UV cure coating specifically for LED applications. The UVCL-LED coating is also a low viscosity coating that enables rapid cure with low energy 365nm LED lamps.
UVCL-HV is a high viscosity UV curable material, designed to provide better coverage of component leads and exposed metal surfaces during dispensing applications and Electrolube’s UVCL-Gel is a no-flow gel version of UVCL, designed for sealing connectors and other areas that must not be coated.
Ron Jakeman, Managing Director of Electrolube, comments, “The new UV cure coating range is an unbeatable range of conformal coating materials and we are very excited about launching the new range to the European market.”
About Electrolube
Electrolube, a division of H.K. Wentworth Limited, is a leading manufacturer of specialist chemicals for electronics, automotive and industrial manufacturing. Core product groups include conformal coatings, contact lubricants, thermal management materials, cleaning solutions, encapsulation resins and maintenance and service aids.
The extensive range of electro-chemicals at Electrolube enables the company to offer a ‘complete solution’ to leading manufacturers of electronic, industrial and domestic devices, at all levels of the production process. Through collaboration and research, the company is continually developing new and environmentally friendly products for customers around the world and their commitment to developing ‘greener’ products has been endorsed by the ISO 14001 standard for the highly efficient Environmental Management System in place at the company.
Winners of the Queen’s award for Enterprise 2016, Electrolube is represented in over 55 countries with an established network of subsidiaries and distributors. By offering genuine security of scale and a reliable supply chain, the company is able to deliver a truly tailored service.
For further information visit www.electrolube.com.
Visit I-007eBooks to download your copy of Electrolube micro eBook today:
The Printed Circuit Assembler's Guide to...Conformal Coatings for Harsh Environments
Testimonial
"We’re proud to call I-Connect007 a trusted partner. Their innovative approach and industry insight made our podcast collaboration a success by connecting us with the right audience and delivering real results."
Julia McCaffrey - NCAB GroupSuggested Items
KYZEN Cleaning Experts to Provide Insights at SMTA High Reliability Cleaning and Coating Conference
07/29/2025 | KYZEN'KYZEN, the global leader in innovative environmentally responsible cleaning chemistries, announced today that three members of the KYZEN team of cleaning experts will present technical presentations as part of KYZEN’s participation at the 2025 SMTA High Reliability Cleaning and Conformal Coating Conference scheduled to take place Aug. 12-14, 2025 at the Westin DFW Airport.
The Knowledge Base: A Conference for Cleaning and Coating of Mission-critical Electronics
07/08/2025 | Mike Konrad -- Column: The Knowledge BaseIn electronics manufacturing, there’s a dangerous misconception that cleaning and coating are standalone options, that they operate in different lanes, and that one can compensate for the other. Let’s clear that up now. Cleaning and conformal coating are not separate decisions. They are two chapters in the same story—the story of reliability.
KYZEN Focuses on Aqueous Cleaning and Stencil Cleaning at SMTA Ontario
06/09/2025 | KYZEN'KYZEN, the global leader in innovative environmentally responsible cleaning chemistries, will exhibit at the SMTA Ontario Expo and Tech Forum, scheduled to take place Tuesday, June 17 at the Venu Event Space in Vaughan, Ontario, Canada. KYZEN will be on-site to provide information about aqueous cleaning chemistry AQUANOX A4618 and the full line of AQUANOX products.
Key Insights on Photoresist for Defect Reduction
05/21/2025 | I-Connect007 Editorial TeamIn PCB manufacturing, understanding the intricacies of the photoresist process is crucial for achieving high-quality results. Industry experts Josh Krick, a technical service engineer at IEC, and Tim Blair, a PCB imaging specialist at Tim Blair LLC, share their knowledge on the essential stages of photoresist application, highlight critical advancements in materials, and discuss common defects encountered during production. They share best practices and innovative solutions to enhance the manufacturing process, reduce defects, and ensure efficiency and reliability in high-tech applications.
KYZEN to Focus on Aqueous Cleaning and Stencil Cleaning at SMTA Juarez
05/20/2025 | KYZEN'KYZEN, the global leader in innovative environmentally responsible cleaning chemistries, will exhibit at the SMTA Juarez Expo and Tech Forum, scheduled to take place Thursday, June 5 at the Injectronics Convention Center in Ciudad Jarez, Chihuahua.