-
- News
- Books
Featured Books
- design007 Magazine
Latest Issues
Current IssueAll About That Route
Most designers favor manual routing, but today's interactive autorouters may be changing designers' minds by allowing users more direct control. In this issue, our expert contributors discuss a variety of manual and autorouting strategies.
Creating the Ideal Data Package
Why is it so difficult to create the ideal data package? Many of these simple errors can be alleviated by paying attention to detail—and knowing what issues to look out for. So, this month, our experts weigh in on the best practices for creating the ideal design data package for your design.
Designing Through the Noise
Our experts discuss the constantly evolving world of RF design, including the many tradeoffs, material considerations, and design tips and techniques that designers and design engineers need to know to succeed in this high-frequency realm.
- Articles
- Columns
- Links
- Media kit
||| MENU - design007 Magazine
Altium’s Craig Arcuri on Design Rules: Past, Present, and Future
May 28, 2019 | Andy Shaughnessy, Design007 MagazineEstimated reading time: 3 minutes
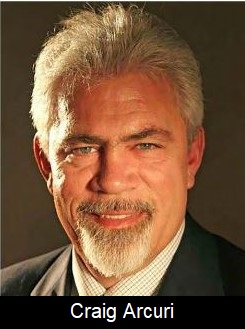
We recently spoke with Altium’s Craig Arcuri about his views on design and manufacturing rules. Craig has experience running both design and manufacturing companies, so he has a fairly circumspect view of constraints from both sides of the product realization process. In this interview, Craig details some of the challenges with setting and managing hundreds of often divergent design and manufacturing rules, and how both design and manufacturing constraints need to evolve to better serve all of the stakeholders in PCB design.
Andy Shaughnessy: Craig, there seems to be a lot of disagreement about design and manufacturing rules, and it seems that there’s not much agreement on best practices. It’s very fragmented, and everyone does design rules their own way. As an EDA tool company guy, what are users asking you all for regarding design rules?
Craig Arcuri: Let me give you a different perspective. Of the last three companies I ran, one was a design company that did engineering design and used CAD tools to create data that was then passed on to manufacturing. Although we tried to care, and said we cared, we really didn’t worry about what happened after we sent the data out because that was somebody else’s problem. Then it was poetic justice that my last two companies were manufacturing companies that had to deal with those folks who didn’t really worry about what happened after the handoff to manufacturing!
You know the phrase “poop rolls downhill.” Well, the manufacturing folks are pretty close to the bottom. At the end of the day, the engineer and layout person have done their job, and a big pile of data comes down and lands on manufacturing. My job is to make a physical thing in less time with less money at a higher quality than is probably reasonably possible given the pile of poop that I was given. Over the course of the last 10 years, I’ve seen 200–300 unique customers per quarter send the data to the manufacturing people, from the perspective of being close to the bottom.
Some of the data comes from companies like Google, Tesla, Intel, and Microsoft. You might think that those companies would provide pristine data and that the design rules would be absolutely well-defined, followed, and implemented in the design EDA tool, and translated through the software into a package where I would think, “This is going to be a piece of cake. What am I going to do with all the money I’m going to make?”
You might also assume that the little guys come across with data out of CAD tools like Eagle and KiCad where a consistent database is a thing of dreams, and it’s a bunch of disconnected data that may or may not have any sanity to it. But you would be sadly mistaken. Across the board, manufacturers rarely receive a data package where manufacturing rules have been considered, adhered to, or worked around, and where the data has been presented in a way that shows that. The instructions are almost never clear and the board can’t always be built.
Now, I won’t put all of the blame on the designer or engineer. If you look at companies like Apple or Samsung, they expect most of the products they design to go into volume production very quickly. Regardless of their size, companies that expect a product to go in volume production clearly consider design rules and manufacturing issues during the design process. They "design for manufacturing," as opposed to "design with manufacturing."
To read this entire interview, which appeared in the May 2019 issue of Design007 Magazine, click here.
Suggested Items
Inside Aimtron’s Cross-border EMS Strategy
07/08/2025 | Nolan Johnson, SMT007 MagazineMukesh Vasani immigrated from a very small farming village in India to the U.S. in 1995 as a civil engineer. After shifting into electronics, Mukesh built his Chicago-based company, Aimtron, into a successful enterprise by combining quality with competitive pricing. He leveraged his roots in India to expand manufacturing without compromising on quality.
Be the Partner Engineers Can Rely On
07/08/2025 | Nolan Johnson, SMT007 MagazineGreen Circuits’ unique niche in the electronics manufacturing industry comes partly from its location in Silicon Valley, but also from its specialty of serving up quick-turn prototypes and low-volume work with high-complexity production. In this conversation, CEO Michael Hinshaw emphasizes the value of end-to-end services, especially while the pace of R&D development is accelerating amidst a growing demand for complexity across industries.
Electronics Industry Wrestles with Cost Pressures and Weaker Profitability
07/07/2025 | Global Electronics AssociationElectronics manufacturers are facing rising material and labor costs according to the Global Electronics Association’s June Sentiment of the Global Electronics Manufacturing Supply Chain Report.
Naprotek Appoints James Eisenhaure as Chief Financial Officer
07/07/2025 | Naprotek LLCNaprotek, LLC, a leading provider of mission-critical electronics technology solutions, today announced that James Eisenhaure has been appointed Chief Financial Officer, effective June 30. Eisenhaure has been serving as interim CFO since earlier this year and now formally steps into the role.
Yannick Green Joins Technica USA as Business Development/Account Manager for Northern California and Northern Nevada
07/07/2025 | Technica USATechnica USA is proud to announce that industry veteran Yannick Green has rejoined Team Technica as Business Development/Account Manager, supporting both supply partners and PCBA customers across Northern California and Northern Nevada.