-
- News
- Books
Featured Books
- design007 Magazine
Latest Issues
Current IssueProper Floor Planning
Floor planning decisions can make or break performance, manufacturability, and timelines. This month’s contributors weigh in with their best practices for proper floor planning and specific strategies to get it right.
Showing Some Constraint
A strong design constraint strategy carefully balances a wide range of electrical and manufacturing trade-offs. This month, we explore the key requirements, common challenges, and best practices behind building an effective constraint strategy.
All About That Route
Most designers favor manual routing, but today's interactive autorouters may be changing designers' minds by allowing users more direct control. In this issue, our expert contributors discuss a variety of manual and autorouting strategies.
- Articles
- Columns
- Links
- Media kit
||| MENU - design007 Magazine
Estimated reading time: 2 minutes
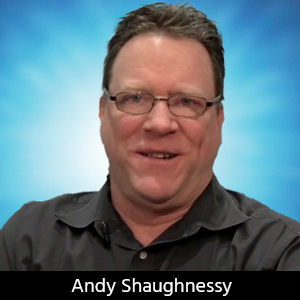
The Shaughnessy Report: Everything Starts with the Designer
Once upon a time in the not-too-distant past, PCB designers were the Rodney Dangerfields of the electronics industry. They didn’t get no respect, and in some cases, not much of a salary either. But times have changed. Now, many designers are starting to realize the power they wield over the whole electronics process.
The folks downstream in fabrication and assembly understood this sentiment long ago, usually expressing it as “It’s the designer’s fault.” But recently, a variety of manufacturers have told me, “Everything starts with design.”
That’s certainly a more positive spin! Everything does start with design—the positive outcomes as well as the negative. The designer can control much of the development of the PCB, and often the final product, with a little planning during the earliest part of the design cycle. It’s a designer’s responsibility to do everything possible to avoid getting that call from the CAM department at 5:30 pm on a Friday.
We surveyed our designer readers in preparation for this issue. Here’s one of the more pertinent questions: What steps do you take to make the job easier for your fabrication and assembly providers? Here are a few of the replies:
- Communicate directly with them, especially if you want to try something new.
- Follow proven design methodologies and rules.
- Get feedback on previous builds to improve upcoming projects.
- Try to insist that the fab house runs Valor DFM.
- Minimize layer count.
- Use the largest trace widths, via sizes, and clearances we can.
- Don’t use more demanding fab technology than absolutely necessary.
- Plan your stack-up with your fabricator.
- Reduce the drill count.
- Follow IPC standards.
A lot of the replies were variations on these themes: Communicate. Don’t throw your downstream partners any technological curve balls. Go big if at all possible, except for layer count. Follow the IPC guidelines.
All of this might make us think that the days of throwing the design “over the wall” are just about over. But there are still flies in the proverbial oatmeal. We know that communication is still a big problem; many designers never speak to their fabricator until they get that Friday evening phone call. But many designers say that they have no earthly idea where their boards are going to be manufactured. They just design each board so that it can, hopefully, be fabricated anywhere.
To read this entire column, which appeared in the June 2019 issue of Design007 Magazine, click here.
More Columns from The Shaughnessy Report
The Shaughnessy Report: A Plan for Floor PlanningThe Shaughnessy Report: Showing Some Constraint
The Shaughnessy Report: Planning Your Best Route
The Shaughnessy Report: Solving the Data Package Puzzle
The Shaughnessy Report: Always With the Negative Waves
The Shaughnessy Report: Breaking Down the Language Barrier
The Shaughnessy Report: Back to the Future
The Shaughnessy Report: The Designer of Tomorrow