-
- News
- Books
Featured Books
- smt007 Magazine
Latest Issues
Current IssueWhat's Your Sweet Spot?
Are you in a niche that’s growing or shrinking? Is it time to reassess and refocus? We spotlight companies thriving by redefining or reinforcing their niche. What are their insights?
Moving Forward With Confidence
In this issue, we focus on sales and quoting, workforce training, new IPC leadership in the U.S. and Canada, the effects of tariffs, CFX standards, and much more—all designed to provide perspective as you move through the cloud bank of today's shifting economic market.
Intelligent Test and Inspection
Are you ready to explore the cutting-edge advancements shaping the electronics manufacturing industry? The May 2025 issue of SMT007 Magazine is packed with insights, innovations, and expert perspectives that you won’t want to miss.
- Articles
- Columns
- Links
- Media kit
||| MENU - smt007 Magazine
Estimated reading time: 3 minutes
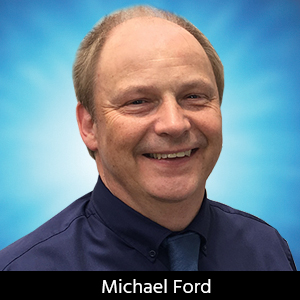
Smart Factory Insights: Recognizing the Need for Change
As you are reading this, there is something significant in your eyeline, that you are not actually seeing—your nose. The human brain is programmed to ignore things that it already recognizes to reduce the load on the analytical side of the brain responsible for visual recognition of objects and events. Only if you really try to focus on your nose, perhaps open one eye at a time, will it come into view. This example of optimization of processing resource is not unique to humans; to some extent, it applies to everything that we do, especially when we grow tired. What are people working every day for many years in manufacturing not seeing?
We Are Only Human, Mostly
We are reminded many times in manufacturing, that "you cannot fix what you cannot see" and "you cannot improve what you cannot measure." These annoying aphorisms are all very well as a motivational quip for gaining better visibility of the operation. However, the reality is that there is a lot going on that no-one is seeing. Many operations and practices have become a part of the background—the canvas on which we perform our daily tasks.
Proof of this has been painful for some when dealing with challenges. Consultants come in from outside to help identify and resolve problems. The frustration is the thought that people within the factory should know what is going on and how to improve. To many, it seems quite unrealistic that external people, who know a great deal less than incumbent factory members about their specific operation, are able to come in and genuinely add considerable value. Consultants see things with “fresh eyes.” In other words, their brains are not blocking out the familiar. They raise questions about everything, including practices, processes, and flows, and challenge every assumption. However, consultants can eventually suffer the same issues as the factory members when they start to believe that they have seen everything.
The same is true for software systems. When evaluating different solutions, each will provide a different set of functions and features that need to be mapped into the process flows and practices of the factory. Any change to the status quo will be met with resistance, even if the change suggested is potentially very valuable. People will immediately try to mold the software to support existing operations that they are comfortable with rather than moving forward. The best software will bring innovative opportunity to break established paradigms and evolve new best practices.
One simple example is the replacement of the push-driven material kitting system with a Lean material management pull-system. Looking honestly and openly at both practices, the difference is enough to clearly differentiate it as a step-change improvement to any factory operation. Yet to date, Lean material management remains a niche technology. As with consultants who have seen everything, most of the old MES software solutions have also become less effective and compelling as time goes on. Most have not been keeping up with the ever-evolving market trends, software architecture, and machine connection technologies, such as IIoT. Thus, their messages become jaded and limited. The “nose effect” is everywhere.
However, there are other surprises in store when humans in the manufacturing operation begin to utilize a modern IIoT-based MES solution and see real data coming from the operation as a whole. The IPC Connected Factory Exchange (CFX) has now become established as the favored method to extract high-quality, detailed, and timely data, natively from machines, all adhering to a single common standard content definition—a true plug-and-play environment. But the limitation of any form of communication from single-machine entities is the need for the derivation of context from all of the many sources of information. Approximately 80% of the data from each individual machine only has significant meaning when set into the context of, for example, the line configuration, the product profile, material logistics, and most of all, the history of what has already happened. Only the latest IIoT-driven MES solution specifically intended to work in this environment with CFX IIoT technology is able to take, format, and present genuine information of value, and then utilize such information for critical decision-making support.
To read the full article, which appeared in the September 2019 issue of SMT007 Magazine, click here.
More Columns from Smart Factory Insights
Smart Factory Insights: Making Rework a Smart Business OpportunitySmart Factory Insights: The Sustainability Gold Rush
Smart Factory Insights: Today’s Manufacturing Jobs Require a New Skill Set
Smart Factory Insights: Compose Yourself, Mr. Ford
Smart Factory Insights: The Smart Business Case for Local PCB Manufacturing
Smart Factory Insights: Manufacturing Digital Twin—Spanners in the Works
Smart Factory Insights: Machines, People, and AI
Smart Factory Insights: Is Sustainability in Manufacturing a Benefit or Burden?