-
- News
- Books
Featured Books
- design007 Magazine
Latest Issues
Current IssueAll About That Route
Most designers favor manual routing, but today's interactive autorouters may be changing designers' minds by allowing users more direct control. In this issue, our expert contributors discuss a variety of manual and autorouting strategies.
Creating the Ideal Data Package
Why is it so difficult to create the ideal data package? Many of these simple errors can be alleviated by paying attention to detail—and knowing what issues to look out for. So, this month, our experts weigh in on the best practices for creating the ideal design data package for your design.
Designing Through the Noise
Our experts discuss the constantly evolving world of RF design, including the many tradeoffs, material considerations, and design tips and techniques that designers and design engineers need to know to succeed in this high-frequency realm.
- Articles
- Columns
- Links
- Media kit
||| MENU - design007 Magazine
Communication, Part 2: Design Data Packages
October 11, 2019 | Steve Williams, The Right Approach Consulting LLCEstimated reading time: 3 minutes
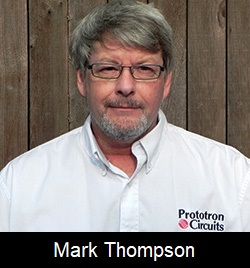
Editor’s note: Click here to read Part 1 and stay tuned for Parts 3–6 of this series.
In Part 2, Bob Chandler from CA Design and Mark Thompson from Prototron Circuits talk with Steve Williams about the importance of preparing, sending, and receiving comprehensive (and ideally, perfectly complete) design data packages.
Steve Williams: Today, we’re moving onto a new topic that I know is especially near and dear to Mark’s heart since he recently wrote a book on it; getting a complete data package. First, what makes a good data package coming from a customer?
Mark Thompson: I’ll try to keep my answer short and sweet. Typically, all we need is the image data for all of the layers: outer layers, inner layers, mask and IDs, any paste files that may be necessary, an IPC netlist, and an NC drill file for each drill scenario. If you had blinds from layers one to two, three to four, or whatever the case may be, it would have a separate drill file for each of the blind scenarios plus the through-hole file.
A good drawing description should denote the material type, stack-up, copper weights, and have a dimension feature that allows placement of the drill within the outline. Also, don’t mix numerical formats; keep them consistent and drill out those that come in anywhere between with leading, trailing, or no zero suppression. We spend a lot of time having to sort those out and figure out exactly what they are. Thus, consistent output of the numerical drill format is very helpful, including 2–4, and trailing and inch is the preferred format.
Williams: Thanks, Mark. Now, Bob, are the requirements for fabricators vastly different between each shop? Is that one of the reasons for incomplete packages, or is what fabricators look for pretty standard?
Bob Chandler: From what I’ve seen, it’s pretty standard; the problem lies with the designer. The tool has a wide variety of options, but not every designer has talked to their fabrication house to ask what outputs they want because we can output a thousand different reports in many ways. Some engineers have certain preferences on how to things while others have no clue; instead, they will randomly push buttons and give the shop whatever comes out. When I do my training, I spend a full day on the design package to make sure that they understand what is needed and why.
Williams: That’s very helpful. The whole purpose of the series is to get the two entities to talk and understand each other’s needs, and it sounds like the work you’re doing up front with people helps eliminate some of those incomplete or inaccurate data packages from reaching board shops.
Chandler: That’s correct. The other thing I would recommend is for the fabrication house to complain when they get the data in a bad format or with missing data. The only way the engineer will learn is when they know that there is an issue. Many companies don’t tell us when they have issues; they spend a little extra time fixing it, but they don’t go back to the designer and say, “If you send me the design data package in this format instead, it will save a lot of time and money.”
Williams: That’s a perfect example of why it’s so important that these two groups talk to one another.
Chandler: Exactly.
Steve Williams is the president of The Right Approach Consulting and an I-Connect007 columnist.
Bob Chandler is CTO of CA Design (cadesign.net) and a senior Allegro/OrCAD trainer and consultant.
Mark Thompson, CID+, is in engineering support at Prototron Circuits and an I-Connect007 columnist. Thompson is also the author of The Printed Circuit Designer's Guide to… Producing the Perfect Data Package. Visit I-007eBooks.com to download this book and other free, educational titles.
Suggested Items
Trouble in Your Tank: Can You Drill the Perfect Hole?
07/07/2025 | Michael Carano -- Column: Trouble in Your TankIn the movie “Friday Night Lights,” the head football coach (played by Billy Bob Thornton) addresses his high school football team on a hot day in August in West Texas. He asks his players one question: “Can you be perfect?” That is an interesting question, in football and the printed circuit board fabrication world, where being perfect is somewhat elusive. When it comes to mechanical drilling and via formation, can you drill the perfect hole time after time?
The Evolution of Picosecond Laser Drilling
06/19/2025 | Marcy LaRont, PCB007 MagazineIs it hard to imagine a single laser pulse reduced not only from nanoseconds to picoseconds in its pulse duration, but even to femtoseconds? Well, buckle up because it seems we are there. In this interview, Dr. Stefan Rung, technical director of laser machines at Schmoll Maschinen GmbH, traces the technology trajectory of the laser drill from the CO2 laser to cutting-edge picosecond and hybrid laser drilling systems, highlighting the benefits and limitations of each method, and demonstrating how laser innovations are shaping the future of PCB fabrication.
Day 2: More Cutting-edge Insights at the EIPC Summer Conference
06/18/2025 | Pete Starkey, I-Connect007The European Institute for the PCB Community (EIPC) summer conference took place this year in Edinburgh, Scotland, June 3-4. This is the third of three articles on the conference. The other two cover Day 1’s sessions and the opening keynote speech. Below is a recap of the second day’s sessions.
Day 1: Cutting Edge Insights at the EIPC Summer Conference
06/17/2025 | Pete Starkey, I-Connect007The European Institute for the PCB Community (EIPC) Summer Conference took place this year in Edinburgh, Scotland, June 3-4. This is the second of three articles on the conference. The other two cover the keynote speeches and Day 2 of the technical conference. Below is a recap of the first day’s sessions.
Preventing Surface Prep Defects and Ensuring Reliability
06/10/2025 | Marcy LaRont, PCB007 MagazineIn printed circuit board (PCB) fabrication, surface preparation is a critical process that ensures strong adhesion, reliable plating, and long-term product performance. Without proper surface treatment, manufacturers may encounter defects such as delamination, poor solder mask adhesion, and plating failures. This article examines key surface preparation techniques, common defects resulting from improper processes, and real-world case studies that illustrate best practices.