-
- News
- Books
Featured Books
- pcb007 Magazine
Latest Issues
Current IssueInventing the Future with SEL
Two years after launching its state-of-the-art PCB facility, SEL shares lessons in vision, execution, and innovation, plus insights from industry icons and technology leaders shaping the future of PCB fabrication.
Sales: From Pitch to PO
From the first cold call to finally receiving that first purchase order, the July PCB007 Magazine breaks down some critical parts of the sales stack. To up your sales game, read on!
The Hole Truth: Via Integrity in an HDI World
From the drilled hole to registration across multiple sequential lamination cycles, to the quality of your copper plating, via reliability in an HDI world is becoming an ever-greater challenge. This month we look at “The Hole Truth,” from creating the “perfect” via to how you can assure via quality and reliability, the first time, every time.
- Articles
- Columns
- Links
- Media kit
||| MENU - pcb007 Magazine
Estimated reading time: 4 minutes
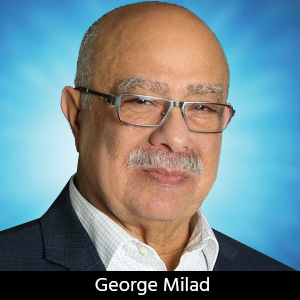
The Plating Forum: Update on IPC-4552 ENIG Specification Revisions
When the original IPC-4552 ENIG specification was issued in 2002, lead-free was not even on the horizon. The original document only mentioned hyper-corrosion (black pad) and recommended keeping the gold thickness to a minimum as a mitigation strategy. In addition, the thickness limit for the immersion gold was single-sided (only lower limit) and needed revision.
IPC ENIG Specification Rev A
IPC ENIG specification 4552 Rev A was issued in 2017. This revision highlighted specific areas based on current information and practices. The revision was a major change to the original document and encompassed intermediary changes in amendments 1 and 2, together with a fundamental change in the specification that pushed back on the suppliers, both PWB and chemistry.
IPC-4552 Rev A addressed:
- Thickness specification
- Thickness measurement
- Process monitoring and control
- Phosphorous content of nickel
- Gold stripping
- Solderability testing
- Copper wire bonding
- Selective annular ring de-wetting
- Nickel corrosion
1. Thickness Specification
A major change was that the thickness specification went from a single-sided specification for gold to a traditional lower and upper limit specification (1.6–4.0 µins) together with easing off on the standard deviation requirements from 4 to 3 sigma.
2. Thickness Measurement
When the original document was released in 2002, the committee explained the importance of correct thickness measurement as illustrated in an appendix but did not account for measurement capability, the uncertainty of measurement, measuring time requirements, etc.; plating distribution across panels; or plating variation panel to panel and tank to tank. For Rev A, it is a requirement to understand, document, and, as necessary, implement guard bands for the measurement capability for the XRF equipment in use. The increase in requirements may necessitate the upgrade of equipment to be able to fully utilize the thickness specification upper and lower limits.
3. Process Control
Once the measurement capability is defined, the process then needs to be evaluated across the entire life of both nickel and gold plating baths; if multiple plating tanks are used, this needs to be performed on all possible combinations of tanks. There is now a maximum allowable standard deviation value permitted for both gold and nickel thickness variability. Failure to meet these values is cause for rejection of the final product, but more importantly, it indicates whether a plating line and the XRF measurement capability are in or out of control.
4. Phosphorus Content
Another requirement added to Rev A was the measurement of the phosphorus content in the nickel across the life of the nickel bath four times a year evaluating at different MTOs. Some chemical suppliers routinely perform this analysis for larger customers, but it now needs to be evaluated for ENIG lines, whether large or small.
5. Gold Stripping
The impact of gold stripping solutions, sometimes used to evaluate for hyper-corrosion, is discussed with the impact of prolonged dwell times and/or different types of chemistry used.
6. Solderability Testing
Pass/fail criteria were inserted in Rev A when using a wetting balance to assess solderability, both as received and post stressing per the requirements of the IPC JSTD-003.
7. Wire Bonding
The suitability of ENIG for Cu and Pd clad Cu wire bonding was approved.
8. Selective Annular Ring De-wetting
The defect selective annular ring de-wetting (SAD) was introduced to the document.
9. Nickel Corrosion
The original document mentioned hyper-corrosion (black pad) and recommended keeping the gold thickness to a minimum as a mitigation strategy. For Rev A, a method for investigating nickel corrosion was introduced, and a hyper-corrosion chart was added with details on how to assess the level of corrosion. The method involves determining the level of corrosion by examining a cross-section at 1000X with a standard optical microscope and suggested a disposition (Table 1). Figure 1 shows examples of different levels of corrosion. Rev A stopped short of making “corrosion evaluation” a requirement for specification compliance.
IPC ENIG Specification Rev B
The committee has completed a new revision of the Rev A, now known as Rev B. It is in the final draft and has gone through one level of balloting. IPC is making sure that the requirements for balloting and the ballot group meet ANSI standards. A new ballot and balloting group are being assembled at this time. The following is a preview of that revision as it relates to nickel corrosion.
Nickel Corrosion Monitoring
Nickel corrosion monitoring is a requirement for compliance. Methods and sampling frequency are spelled out in the document.
Acceptance/Rejection Criteria
The new revision uses the same corrosion levels spelled out in Rev A. However, it has added a new method (namely product rating) for determining acceptability. The revision specifies a specific number of observation (7 for through-hole and 5 for pad only). Each observation point is given a corrosion level rating (Levels 1, 2, and 3). From the 7 or 5 corrosion level values, a product rating for acceptability is determined according to the following proposed Table 2. Using product rating criteria, the presence of an occasional Level 3 type corrosion observation does not necessarily condemn the product, as was suggested in Rev A.
IPC-4552 specification Rev B has not yet been formally issued. The committee’s objective is to eliminate nickel corrosion (also known as a black pad). By making nickel corrosion monitoring a requirement, it raises the awareness of the problem and will eventually eliminate it. The manufacturers will recognize the critical process steps that will keep the process corrosion-free, and the suppliers will have to come up with more corrosion-resistant processes. Stay tuned.
George Milad is the national accounts manager for technology at Uyemura.
More Columns from The Plating Forum
The Plating Forum: Reduction Assisted Immersion Gold for ENEPIG Surface FinishThe Plating Forum: Surface Finish Evolution from Conventional to Advanced
The Plating Forum: Plating in Electronic Applications
The Plating Forum: How the Pandemic Impacted PCB Manufacturing
The Plating Forum: The Significance of IPC ENIG Specification 4552 Revision B
The Plating Forum: The IPC Surface Finish Specifications
The Plating Forum: An Overview of Surface Finishes
The Plating Forum: DIG—The Next Generation