-
- News
- Books
Featured Books
- pcb007 Magazine
Latest Issues
Current IssueInventing the Future with SEL
Two years after launching its state-of-the-art PCB facility, SEL shares lessons in vision, execution, and innovation, plus insights from industry icons and technology leaders shaping the future of PCB fabrication.
Sales: From Pitch to PO
From the first cold call to finally receiving that first purchase order, the July PCB007 Magazine breaks down some critical parts of the sales stack. To up your sales game, read on!
The Hole Truth: Via Integrity in an HDI World
From the drilled hole to registration across multiple sequential lamination cycles, to the quality of your copper plating, via reliability in an HDI world is becoming an ever-greater challenge. This month we look at “The Hole Truth,” from creating the “perfect” via to how you can assure via quality and reliability, the first time, every time.
- Articles
- Columns
- Links
- Media kit
||| MENU - pcb007 Magazine
Estimated reading time: 9 minutes
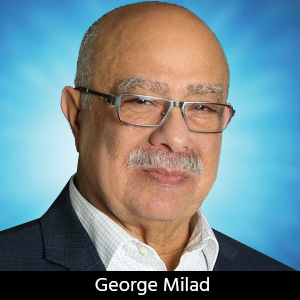
The Plating Forum: The IPC Surface Finish Specifications
Specifications are reference documents to be called out by OEM board designers in specifying the attributes of a surface finish. Designers may take exception to one or more items in the specification to ensure that the product meets the requirements of its intended use. The term “AAUBUS” (As Agreed Upon Between User and Supplier) is part of any specification.
Specifications are consensus documents. They are agreed upon by a panel of interested industry participants composed of end users (OEMs), manufacturers, assemblers, and suppliers. If there is consensus, then the committee documents it in a draft specification for peer review.
In cases where no consensus is readily arrived at, the committee undergoes its own testing in what is commonly referred to as a “Round Robin” (RR) study. In a RR investigation, an agreed-upon test vehicle (TV) is designed and manufactured. TVs are then sent around to the different suppliers who deposit the agreed upon thicknesses to be investigated. The TVs are collected, and the deposit thicknesses are verified and documented. The TVs are then coded and sent around again to the different testing sites that test for the desired attributes like soldering, contacting, and wire bonding capabilities of the different finish thicknesses. The data is then collected, sorted out, and documented. At this point, a new attempt at consensus is made and, when achieved, the thickness specification is set, and the specification is drafted.
The “Draft” is posted for “Peer Review.” Any IPC member can review the document and suggest technical or editorial changes. All comments are then reviewed, and all issues are resolved before the “Final Draft” is issued. At this time, the IPC takes on the task of publishing the document in its final format.
The IPC Plating Subcommittee 4-14 was active from 2001–2019. The committee was co-chaired by George Milad of Uyemura International Corp., and Gerard O’Brien, president and owner of ST and S Group, a consulting and testing facility. The IPC liaison was Tom Newton. The committee had an extensive member list composed of OEMs, assembly manufacturers, suppliers, labs, and consultants. Members participated on and off in conference calls that they were interested in and as their time allowed. Not all members were on all conference calls. Below is a listing of participant companies.
OEM and CM: Lockheed Martin, Raytheon, Oracle, Adtran, Rockwell Collins, Hewlett-Packard, Alcatel-Lucent, Dell, St. Jude Medical, Delphi, Schneider Electric, Continental Corporation, Panasonic, IBM, Northrop Grumman, BAE Systems, Honeywell, Boeing, Tyco Electronics, Peregrine Semiconductor, Space Systems /Loral, Amonix, Celestica, Winstron.
PCB manufacturing: TTM, I3, Molex, Bergquist, Superior Processing, Alternate Final Finishing.
Suppliers: MacDermid, Uyemura, Atotech, Technic Inc, MEC, ECI Technology, Kulick & Sofa, Metalor, Fischer Technology, Hesse-Mechatronics.
Labs and Consultants: ST and S Group, Sandia Laboratories, DFR Solutions, TAS Consulting.
The committee met every other week for a one-hour conference call. Those in attendance made decisions. The minutes of the meeting were documented and distributed to the members.
Since its inception, the IPC Plating Subcommittee 4-14 has issued the following:
- IPC-4552 ENIG Specification 2002
- IPC-4553 Immersion Silver specification 2005
- IPC-4554 Immersion Tin Specification 2007
- IPC-4553A Revised Immersion Silver 2009
- IPC-4554 Amended Tin Specification 2011
- IPC-4552 Amended ENIG Specification 2012
- IPC-4556 ENEPIG Specification 2013
- IPC-4556 ENEPIG Amended Specification 2015
- IPC-4552 Rev A ENIG Specification 2017
- IPC-4552 Rev B ENIG Specification 2021
The ENIG IPC-4552 Specification was issued in 2002. No lead-free (LF) solder was in use at that time.
For thickness, IPC-4552 stated:
- The EN thickness shall be 3 to 6 µm (118.1 to 236.2 µin)
- The minimum IG thickness shall be 0.05 (1.97 µin) at four sigma (standard deviation) below the mean. The typical range is 0.075 to 0.125 µm (2.955 to 4.925 µin)
- No upper limit was set
Immersion Silver IPC-4553 issued in 2005. In 2005, there were two distinct types of commercialized immersion silver with different thickness recommendations, referred to as “Thin” and “Thick.” Each required its own thickness specification.
The initial 4553 specification stated the following for thickness of deposit.
Two thickness specification:
- Thin silver: 0.05 µm (2 µ”) minimum at -2? from process mean as measured on a pad of area 2.25² µm (3600² mils).Typical value 0.07 µm (3 µ”) to 0.1 2µm (5 µ”)
- Thick silver: 0.12 µm (5 µ”) minimum at -4? from process mean as measured on a pad of area 2.25 µm (3600² mils). Typical value of 0.2 µm (8 µ”) to 0.3 µm (12 µ”).
The immersion tin specification was issued in 2007. For immersion tin, the committee specified a lower limit for thickness. The relatively thick value of 1 micron was chosen to ensure that enough virgin tin would be available at the surface for soldering after storage. It is well understood that tin forms an intermetallic (IMC) layer with the underlying copper, and that this layer continues to grow in thickness over time.
The immersion tin thickness will be: 1.0 µm (40 µ”) minimum at -4? from process mean as measured on a pad of area 2.25² µm (3600² mils). Typical value of 1.15 µm (46 µ”) to 1.3 µm (52 µ”).
The Immersion Tin Specification IPC-4554 was amended in 2011. The amendment addressed solderability testing and specified the allowed stress testing conditions for the deposit and the type of fluxes to be used for both tin-lead and LF (lead-free) testing.
Specification IPC-4555 for OSP (organic solderabilty preservative) was attempted in 2008. After more than one year of struggling with Specification IPC-4555, nothing was specified. There was no consensus arrived at. This was mostly due to the wide assortment of organic products that were used for solderability preservation for the various applications, each with its own recommended thickness values.
In 2009, the Immersion Silver Specification IPC-4553 was revised and Immersion Silver IPC-4553A was issued in 2009. The original specification with a thin and a thick specification was confusing and hard to understand. In addition, the industry settled on one type of immersion silver, and it necessitated the issuance of a single thickness specification, with the addition of an upper spec limit: IPC-4553A specified a single thickness with an upper limit:
- 0.12 µm [5 µin] minimum to 0.4 µm [16 ?in] maximum at ± 4? from process mean as measured on a pad area approximately 2.25 mm², example; 1.5 mm X 1.5 mm (60 X 60 mil). Typical value between 0.2 µm [8 µin] to 0.3 µm [12 µin].
- An upper limit was set.
In 2012, IPC-4552 ENIG specification was amended to reduce the lower limit of immersion gold thickness. The lower limit for gold thickness was reduced from 0.05 µm to 0.04 µm (1.6 µin) with restrictions:
- Limited time from manufacturing to assembly
- Demonstrate the consistency of the plating process
- Ability to measure low gold thickness
IPC-4556 ENEPIG, 2013
The document produced is very comprehensive and includes a wealth of information from the RR studies that were conducted. The appendix contains a documentation of these studies, each authored by the person who conducted the testing. It also includes a section on the proper methods of equipment setup for a reliable measurement of very thin layers of metal deposits.
Appendices 1–9
- Chemical Definitions and Process Sequence; Martin Bayes, Dow Chemical Company
- Round Robin Test Summary; George Milad, Uyemura International Corporation
- ENEPIG PWB Surface Finish XRF Round Robin Testing; Gerard O’Brien, S T and S Group.
- Factors Affecting Measurement Accuracy of ENEPIG Coatings by XRF; Frank Ferrandino, Calmetrics Inc.
- ENEPIG PWB Surface Finish Wetting Balance Testing; Gerard O’Brien, S T and S Group.
- Solder Spread Testing; Brian Madsen, Continental
- ENEPIG PWB Surface Finish Shear Test Project; Dave Hillman et al., Rockwell Collins Inc.
- Gold Wire Bonding; Stephen Meeks, St Jude Medical
- XRF Thickness Measurements of thin Au and Pd (ENEPIG): Recommendations for Instrumentation (Detectors) and their Limitations; Michael Haller, Fischer Technology
The thickness specification for ENEPIG states:
- Nickel: 3 to 6 µm [118.1 to 236.2 µin] at ± 4 sigma (standard deviations) from the mean
- Palladium: 0.05 to 0.30 µm [2 to 12 µin] at ± 4 sigma (standard deviations) from the mean
- Gold: minimum 0.030 µm [1.2 µin] at - 4 sigma (standard deviations) below the mean. No upper limit
- All measurements to be taken on a nominal pad size of 1.5 mm x 1.5 mm [0.060 in x 0.060 in] or equivalent area
The ENEPIG spec was amended in 2015. The amendment added an upper spec limit for immersion gold thickness. The thickness specification for ENEPIG states:
- Nickel: 3 to 6 µm [118.1 to 236.2 µin] at ± 4 sigma (standard deviations) from the mean
- Palladium: 0.05 to 0.30 µm [2 to 12 µin] at ± 4 sigma (standard deviations) from the mean
- Gold: minimum 0.030 µm [1.2 µin] at -4 sigma (standard deviations) below the mean, maximum 0.07 µm [2.8 µin]
If thicker gold is a design requirement, alternate gold deposition methods should be used, like:
- Electroless gold
- Reduction assisted immersion gold (RAIG)
All measurements to be taken on a nominal pad size of 1.5 mm x 1.5 mm [0.060 in x 0.060 in] or equivalent area.
IPC-4552 Rev A, ENIG
The IPC-4552 A, revised ENIG specification was issued in 2017. The revision added a new lower limit for the immersion gold and for the first time specified an upper limit. IPC 4552A also addressed nickel corrosion and specified a “Corrosion Chart.” It also included a method for qualifying XRF equipment.
The IPC-4552 A, ENIG Specification 2017:
- The gold thickness shall be 1.6 (0.04 µm) to 4.0 µin (0.1 µm)
- The upper limit of 4.0 µin must be strictly adhered to
Corrosion Chart
Examine the corrosion spikes (if any) on the ENIG surface with an optical microscope at 1000X magnification, for frequency and depth. Three classification levels:
- Level 1: Acceptable (less than 10 spike defects with a depth
- Level 2: Disputable (spikes and depth > than Level 1 and < Level 3)
- Level 3: Rejectable (>10 spike defects with >2 microns depth)
This was the first time that nickel corrosion was addressed and 4552A put a stake in the ground. It became clear that the way the corrosion evaluation was stated was problematic because it did not address frequency of occurrence.
IPC-4552B was initiated in 2017 to address this deficiency. 4552B maintained the levels set in 4552A but added a method to quantify frequency of occurrence. 4552B introduced the term “Product Rating.” Seven specified locations in a plated through-hole, or five specified locations on a surface pad were examined for defects and their frequency of occurrence:
- Product rating 0: Acceptable; No corrosion defects.
- Product Rating 1: Acceptable; >60% of locations examined show Level 1 or less.
- Product Rating 2: (Acceptable, provided that solderability requirements are met); defects and frequency greater than Product Rating 1 but less than Product Rating.
- Product Rating 3: (Non-conforming;) More than 40% of locations showing Level 3 defects.
With the issuance of 4552A and 4552B there is now a way to quantify nickel corrosion. It is the author’s experience that the availability of a quantifying method is already paying great dividends, as the occurrence of the defect is already showing signs of coming under control. OEMs or buyers can now specify acceptable levels of corrosion and the manufacturer and supplier have to make the required changes to meet those levels.
Presently, Subcommittee 4-14 is subdivided into subgroups, each with its own chair and vice-chair to address a single finish; for example, an OSP committee and an EPIG committee, etc.
All committee work is voluntary from participation in meetings to manufacturing test vehicles and testing. Companies allow their employees to spend time in committee work and these companies must be credited for the successful issuance of IPC specification. The author urges all industry personnel to sign up and participate in committee work in the areas of their interest. You will learn a lot by communicating and collaborating with other members and more importantly, you will give back to the industry and to the community at large.
This column originally appeared in the September 2021 issue of PCB007 Magazine.
George Milad is the national accounts manager for technology at Uyemura.
More Columns from The Plating Forum
The Plating Forum: Reduction Assisted Immersion Gold for ENEPIG Surface FinishThe Plating Forum: Surface Finish Evolution from Conventional to Advanced
The Plating Forum: Plating in Electronic Applications
The Plating Forum: How the Pandemic Impacted PCB Manufacturing
The Plating Forum: The Significance of IPC ENIG Specification 4552 Revision B
The Plating Forum: An Overview of Surface Finishes
The Plating Forum: DIG—The Next Generation
The Plating Forum: RAIG (Reduction Assisted Immersion Gold) for Gold Surface Finishes