-
- News
- Books
Featured Books
- pcb007 Magazine
Latest Issues
Current IssueInventing the Future with SEL
Two years after launching its state-of-the-art PCB facility, SEL shares lessons in vision, execution, and innovation, plus insights from industry icons and technology leaders shaping the future of PCB fabrication.
Sales: From Pitch to PO
From the first cold call to finally receiving that first purchase order, the July PCB007 Magazine breaks down some critical parts of the sales stack. To up your sales game, read on!
The Hole Truth: Via Integrity in an HDI World
From the drilled hole to registration across multiple sequential lamination cycles, to the quality of your copper plating, via reliability in an HDI world is becoming an ever-greater challenge. This month we look at “The Hole Truth,” from creating the “perfect” via to how you can assure via quality and reliability, the first time, every time.
- Articles
- Columns
- Links
- Media kit
||| MENU - pcb007 Magazine
Estimated reading time: 4 minutes
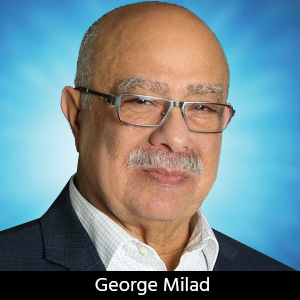
The Plating Forum: DIG—The Next Generation
DIG stands for “Direct Immersion Gold.” The acronym is used to specify direct deposition of gold on copper as a surface finish. It is a metallic solderable finish. At assembly, DIG forms a Cu/Sn intermetallic with the gold layer dissipating into the bulk solder. DIG has been around for at least 15 years.
Gold will readily immerse on copper based on their respective positions in the EMF series. The reaction is driven by +1.22 volts. As in all immersion reactions, the reaction will continue as long as the substrate is available to the displacement reaction. As the substrate is covered by the depositing species, it becomes less available, rendering the reaction self-limiting.
The original formulation of DIG produced a relatively thin gold layer that had a reddish hue to it from the partial diffusion of copper. Copper diffusion to the surface continued with time; after a year of storage at ambient conditions the deposit color became increasingly reddish, almost brown. Checking the solderability of the discolored surface using wetting balance methods showed excellent wetting and no signs of soldering degradation.
At that time, DIG did not seem to offer any breakthroughs as other established finishes like OSP, immersion silver, and immersion tin. These surface finishes were well-established, their limitations were well understood, and they were deployed extensively in PCB manufacturing. DIG was a more costly finish and created apprehension as it was clear that the copper would diffuse through the immersion grain boundaries into the gold, altering the as-received surface.
A new generation of DIG was developed to meet the needs for wire bonding and high frequency signal propagation. High frequency RF signal loss is associated with thicker nickel deposits. The new DIG process uses a reduction-assisted immersion gold (RAIG). The use of an RAIG gold allowed for the deposition of a thicker gold layer up to 0.3 µm (12 µins) that prevented the diffusion of copper to the surface.
During deposition the immersion gold initiates on the copper surface and that triggers the electroless deposition, which will continue to deposit as the copper substrate gets plated over and is no longer available to sustain the immersion reaction. The electroless reaction does not require substrate contribution as it is driven by a reducing agent in the electrolyte. The electroless deposit is non-granular and not porous. Unlike the original immersion DIG, this new mode of deposition can produce a thicker layer that is pore-free (no grain boundaries) thus limiting the migration of copper. The deposit has the lemon-yellow color that is expected of a gold deposit in contrast with the reddish yellow of the original DIG. At 0.2 to 0.3 µm, the deposit shows no signs of copper diffusion to the surface.
Hofstetter PCB AG in Küssnacht/Switzerland is a supplier of various coatings in microelectronics. Hofstetter supplies a complete spectrum of surface finish plating to the microelectronics industry. They offer some of the newer finishes like EPIG (electroless palladium immersion gold), ISIG (immersion silver immersion gold), and DIG (direct immersion gold). Their R&D department invests in studying the properties of some of the newer finishes coming to the market, exploring solutions to meet the ever-changing demands of their customers.
Hofstetter has conducted a comprehensive study on the gold wire bondability of the new DIG process.
They studied the consistency and strength of the gold wire bonds under different temperatures, namely 90–130oC for the wedge bond and 150oC for the first (ball) bond. They included room temperature bonding in the study. Room temperature bonding has a narrow operating window compared to a heated table. Success at room temperature bonding was achieved by the optimization of the DIG surface topography and the US (ultrasound) bonding force. The study concluded that the new DIG at 8-12 µins (0.2–0.3 µm) thickness is capable of producing wire bonds consistently and reproducibly with optimized bonding parameters.
The DIG surface at 8–12 µins exhibits a distinct fine roughness, which is very evenly formed over the entire surface. The new DIG surface requires minimum processing steps. Deposition requires a standard cleaner and micro-etch followed by the gold bath. This contrasts with ENEPIG which requires cleaner, micro-etch, catalyst, electroless nickel, electroless palladium, and immersion gold.
The new DIG is a surface finish that offers advantages over the traditional finishes like OSP, immersion silver, and immersion tin. OSP is a fragile, organic solderability preservative that cannot be used as a contacting surface. Immersion silver is a good contacting surface but was susceptible to creep corrosion and occasionally formed voids at the IMC surface. Immersion tin will form a Cu/Sn intermetallic during storage and may lose some of its wetting properties at assembly.
The new DIG, which is commercially available today, is solderable and aluminum and gold wire bondable, and it is ideally suited for plating small features with limited spacing. The absence of nickel in the surface finish makes it well-suited for high frequency applications.
This column originally appeared in the June 2021 issue of PCB007 Magazine.
More Columns from The Plating Forum
The Plating Forum: Reduction Assisted Immersion Gold for ENEPIG Surface FinishThe Plating Forum: Surface Finish Evolution from Conventional to Advanced
The Plating Forum: Plating in Electronic Applications
The Plating Forum: How the Pandemic Impacted PCB Manufacturing
The Plating Forum: The Significance of IPC ENIG Specification 4552 Revision B
The Plating Forum: The IPC Surface Finish Specifications
The Plating Forum: An Overview of Surface Finishes
The Plating Forum: RAIG (Reduction Assisted Immersion Gold) for Gold Surface Finishes