-
- News
- Books
Featured Books
- pcb007 Magazine
Latest Issues
Current IssueInventing the Future with SEL
Two years after launching its state-of-the-art PCB facility, SEL shares lessons in vision, execution, and innovation, plus insights from industry icons and technology leaders shaping the future of PCB fabrication.
Sales: From Pitch to PO
From the first cold call to finally receiving that first purchase order, the July PCB007 Magazine breaks down some critical parts of the sales stack. To up your sales game, read on!
The Hole Truth: Via Integrity in an HDI World
From the drilled hole to registration across multiple sequential lamination cycles, to the quality of your copper plating, via reliability in an HDI world is becoming an ever-greater challenge. This month we look at “The Hole Truth,” from creating the “perfect” via to how you can assure via quality and reliability, the first time, every time.
- Articles
- Columns
- Links
- Media kit
||| MENU - pcb007 Magazine
Estimated reading time: 4 minutes
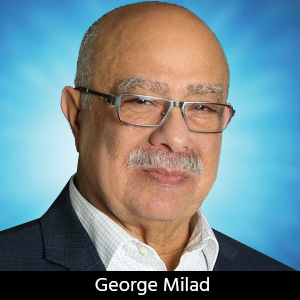
The Plating Forum: Reduction Assisted Immersion Gold for ENEPIG Surface Finish
RAIG was introduced a few years ago to meet the requirements of newer designs. Since its inception more gold finishes are finding RAIG to be a viable alternative to standard immersion gold. RAIG is a mixed reaction bath that functions as an immersion gold and, with the added reducing agent, it also functions as an electroless (autocatalytic) bath.
The immersion reaction initiates the gold plating with the introduction of the substrate (nickel, palladium, or copper) into the electrolyte. The deposited immersion gold layer will trigger the electroless reaction. Being a displacement reaction, the immersion reaction will diminish with time as the substrate becomes less available with deposition. The electroless reaction will continue, as it relies on the reducing agent present in the electrolyte and not on substrate availability. RAIG is limited on how much gold it can deposit, as compared to a pure electroless gold. It is ideally suited for thicknesses of 3–8 µins.
Limiting the immersion reaction and allowing gold thickness to build up autocatalytically opens the operating window by allowing thicker gold to deposit without nickel corrosion. A thicker gold layer (3–8 µins), which is beyond the capability of standard immersion gold electrolytes, is desirable as it widens the operating window for gold wire bonding.
Figure 1 shows the relationship between gold thickness and the strength of the wire bond. Two thicknesses of gold—0.05 mm (2.0 µins) and 0.2 mm (8.0 µins)—were bonded using a 0.25-mm gold wire at three different bonding forces (25, 50, and 75g force). Ultrasonic power (mW) and time (sec) were held constant. The wires were then pulled and the break point in the wire was recorded. Bond lifts (E) and brakes at the heel of the bond (D) were indicative of weak or non-reliable bonds. Break points (B and C) were indicative of a reliable bond.
The data shows that both thicknesses were capable of producing robust joints. However, the thinner (0.05 mm) gold required a higher gram force to make a reliable bond. The thicker gold (0.2 mm) produced reliable bonds at lower gram force, opening the operating window for the bonding parameter.
For gold wire bonding applications, designers prefer to specify a gold thickness of 3–5 µins. This thickness is beyond the capability of an immersion gold. Increasing dwell time in an immersion gold bath is the leading cause of nickel corrosion.
ENEPIG With RAIG
ENEPIG forms the most reliable solder joint with lead-free solder and is a gold wire-bondable surface. It is presently specified in cases where both soldering and gold wire bonding are the chosen methods of connectivity.
Immersion gold on palladium in ENEPIG deposits is limited in thickness, due to closeness of the Au and Pd in the EMF series. The driving force of the reaction is much lower than the driving force for the immersion of gold on a nickel surface, as in the case of ENIG. Achieving a thickness in excess of 1.2 µins of gold on Pd will require an extended time in the immersion gold bath which, in turn, would increase the probability of nickel corrosion under the palladium layer. If nickel is corroded under the Pd, the wire bond strength will be compromised, and this would lead to bond lift failure at the nickel palladium interface.
As ENEPIG gains market share, it has become evident that the gold wire bonding operating parameters are successful in a relatively narrow range. During assembly, the wire bonding parameters (heat, ultrasound frequency, and gram force) must be closely monitored for successful bonds to occur. “Wire pull” studies have shown that increasing the gold thickness would widen the window of operation and would statistically improve the yield and reliability of the of the bonds formed. Many designers now specify gold thickness in excess of the IPC 4566A specified range for gold thickness.
Nickel corrosion is mainly attributed to imperfections in the palladium layer coupled with an extended dwell time in a corrosive (low gold concentration) immersion gold electrolyte. Under such conditions the immersion gold ions in solution will have access to the underlying nickel and will be reduced to gold metal. The gold metal will deposit on top of the palladium layer and the nickel will corrode.
The ENEPIG data set in Figure 2 shows clearly that RAIG eliminated any possibility of nickel corrosion and maintained excellent wettability during soldering. Nickel corrosion was evaluated using the method specified in IPC-4552B. Wetting balance was used to evaluate wettability.
The data shows that the use of RAIG in place of immersion gold yielded a reproducible thickness of 8.0 µins of gold, on top of the palladium and nickel. Thickness data came from 20 different pads (60 x 176 mil). The added gold thickness enhances the gold wire bonding ability of the ENEPIG surface, as it widens the operating window of the bonding parameters.
Corrosion evaluation was done by following the method outlined in IPC-4552B, ENIG Specification. Cross-sections in Figure 3 from different locations were evaluated at 1000x magnification and were examined for any corrosion spikes. The micrographs show “zero” corrosion level.
Solderability was evaluated per JSTD-003C WAM 1&2 Specification.
Wetting balance Time (? 2.5 seconds) = Avg. is 2.25 seconds, Pass.
Wetting balance Force (> 0.17mN/mm) = Avg. is 0.22 mN/mm, Pass.
The thicker gold layer meets J-STD-003C WAM1&2 specification and shows no evidence of non-wetting or de-wetting.
The use of RAIG in place of standard immersion gold will allow for the deposition of a thicker gold layer, thus overcoming the limitations of immersion gold on palladium. The RAIG thicker gold layer had no adverse effects on solderability. An added benefit to the use of RAIG is that the probability of nickel corrosion under the palladium layer is eliminated.
This column originally appeared in the June 2023 issue of PCB007 Magazine.
More Columns from The Plating Forum
The Plating Forum: Surface Finish Evolution from Conventional to AdvancedThe Plating Forum: Plating in Electronic Applications
The Plating Forum: How the Pandemic Impacted PCB Manufacturing
The Plating Forum: The Significance of IPC ENIG Specification 4552 Revision B
The Plating Forum: The IPC Surface Finish Specifications
The Plating Forum: An Overview of Surface Finishes
The Plating Forum: DIG—The Next Generation
The Plating Forum: RAIG (Reduction Assisted Immersion Gold) for Gold Surface Finishes