-
- News
- Books
Featured Books
- pcb007 Magazine
Latest Issues
Current IssueInventing the Future with SEL
Two years after launching its state-of-the-art PCB facility, SEL shares lessons in vision, execution, and innovation, plus insights from industry icons and technology leaders shaping the future of PCB fabrication.
Sales: From Pitch to PO
From the first cold call to finally receiving that first purchase order, the July PCB007 Magazine breaks down some critical parts of the sales stack. To up your sales game, read on!
The Hole Truth: Via Integrity in an HDI World
From the drilled hole to registration across multiple sequential lamination cycles, to the quality of your copper plating, via reliability in an HDI world is becoming an ever-greater challenge. This month we look at “The Hole Truth,” from creating the “perfect” via to how you can assure via quality and reliability, the first time, every time.
- Articles
- Columns
- Links
- Media kit
||| MENU - pcb007 Magazine
Estimated reading time: 4 minutes
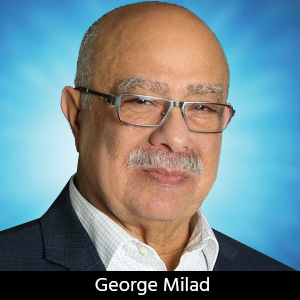
The Plating Forum: Plating in Electronic Applications
Plating is the deposition of a metal layer on a substrate to modify its properties. It occurs when the metal ion in an aqueous solution is reduced to the metal:
M+ metal ion + e- reducing electron = M0 deposited metal
Plating can achieve numerous functional and aesthetic goals, including:
- Improve solderability
- Inhibit corrosion
- Increase hardness/durability
- Decorate objects (jewelry)
- Reduce friction
- Alter conductivity
- Improve IR reflectivity
- Provide radiation shielding
The reducing electron e- can be supplied from these deposition reactions:
- Electroplating
- Electroless plating
- Immersion plating
Electroplating
This is a galvanic reaction that occurs when current is applied to an anode and a cathode immersed in the metal electrolyte. The anode is composed of the desired metal for deposition, typically copper, tin, or nickel. When voltage or current is applied, the metal at the anode will dissolve as a positive ion, leaving a negative charge at the anode.
At the cathode, the positive ion will be reduced to the metal, taking up electrons from the cathode which is rendered positive. The deposited weight depends on the current and the time, and is governed by Faraday’s law. Electroplating requires connectivity. It is used to plate metal alloys, and in dispersion plating. The latter involves the uniform dispersion of a non-conductive entity in the electroplated metal.
Electroless Plating
In electroless plating, the negative electron is supplied by a reducing agent present in the electrolyte. The reducing agent is oxidized, and the metallic target ion is reduced to the metal. Plating continues as long as the reducing agent and the target ion concentration are maintained through replenishment. Electroless plating is independent of connectivity. Examples are electroless copper and electroless nickel, electroless gold, and electroless palladium.
Immersion Plating
In immersion plating, the reducing electron is supplied by the substrate where the deposition is occurring. The substrate metal is oxidized to the metal ion giving up an electron. The electron reduces the target ion to the metal for deposition. Only metals higher in the EMF series can replace metals below them. Immersion deposition is a displacement reaction and is limited to the availability of the substrate being plated. Examples include immersion silver, immersion tin, immersion gold, and others.
The general principles of all three methods are well understood and have been used for decades in electronics manufacturing. Refining the plating process to meet specific electronics requirements is the challenge faced by chemical manufacturers as complexity and miniaturization continue to increase. The following examples demonstrate how plating processes are modified and adapted to meet specific design requirements.
Copper Plating
Copper is a highly conductive non-precious metal. It is the conduit that carries the flow of current through printed wiring boards and semiconductors (integrated circuits) devices. Electroplated copper is the dominant method for plating traces and through-holes.
The challenge for electroplated copper in electronics is achieving consistent quality and thickness distribution throughout the part. Controlling the quality of the deposited copper (tensile strength and elongation) ensures that the deposit will not crack or fracture with the thermal excursion the parts are exposed to during manufacture and throughout their life cycle. Thickness distribution is critical for controlling impedance throughout the device.
The use of additives (brightener, suppressor, and leveler) in the electrolyte, plating current density, and plating cell geometry are designed and manipulated to achieve a specific outcome, such as via filling, plating high aspect-ratio holes, and plating fine lines and spaces.
Surface Finishes
Surface finishing of electronic products is an integral part of manufacturing. It serves many functions, the most prominent of which is to create a solderable surface. It is also used as a corrosion barrier and an electrical contacting surface, as well as a wire bonding surface. One or more of the three methods of plating are used to create the desired surface. The layer may be a single component such as immersion silver, tin, gold, or palladium, or multiple consequential layers such as electroless nickel/immersion gold (ENIG), electroless nickel/electroless palladium/immersion gold (ENEPIG) and electroplated nickel/gold.
The choice of what thickness of metal to plate and what plating method to use is always based on meeting specific design requirements with the lowest cost. For example, solderable and gold wire-bondable finishes limit the choice of deposit. At the moment, the leading finish for this application is ENEPIG. However, if the part is used for high RF (>20 GHz) signal propagation, nickel must be eliminated to avoid signal loss. This makes electroless palladium/immersion gold (EPIG) the appropriate alternative.
Automotive
As electric vehicles continue to grow in popularity, there is great demand for EV surface finishes that provide:
- Wear resistance and corrosion resistance
- High number of plugging cycles (10K+…)
- High electrical and thermal conductivity
- Elimination of lubricant
- Long-term, stable hardness (1000h ? end of life)
- Temperature-stable hardness (150°C ? 180°C)
- Extended contact/connector life
Silver is fundamental for electronic components used in electric vehicles, charging stations, and power grids, but to deliver the capabilities required, silver must be modified. Studies of various alloys found none were able to meet the criteria listed above.
One of the ways to achieve the desired performance is dispersive plating, specifically with graphite as the dispersion element due to its availability and lower cost compared to alternatives. Dispersing graphite in the silver deposit produced the desired tribology attributes (wear friction and lubrication), hardness and conductivity.
Chemical suppliers to the electronics industry are continuously adapting the plating processes described to achieve the appropriate thickness of metal or metals (alloy or dispersion metal) in single or multiple consecutive layers. Meeting the design functionality at the lowest cost will always control the choice of plating material and plating options.
This column originally appeared in the June 2022 issue of PCB007 Magazine.
More Columns from The Plating Forum
The Plating Forum: Reduction Assisted Immersion Gold for ENEPIG Surface FinishThe Plating Forum: Surface Finish Evolution from Conventional to Advanced
The Plating Forum: How the Pandemic Impacted PCB Manufacturing
The Plating Forum: The Significance of IPC ENIG Specification 4552 Revision B
The Plating Forum: The IPC Surface Finish Specifications
The Plating Forum: An Overview of Surface Finishes
The Plating Forum: DIG—The Next Generation
The Plating Forum: RAIG (Reduction Assisted Immersion Gold) for Gold Surface Finishes