-
- News
- Books
Featured Books
- smt007 Magazine
Latest Issues
Current IssueSupply Chain Strategies
A successful brand is built on strong customer relationships—anchored by a well-orchestrated supply chain at its core. This month, we look at how managing your supply chain directly influences customer perception.
What's Your Sweet Spot?
Are you in a niche that’s growing or shrinking? Is it time to reassess and refocus? We spotlight companies thriving by redefining or reinforcing their niche. What are their insights?
Moving Forward With Confidence
In this issue, we focus on sales and quoting, workforce training, new IPC leadership in the U.S. and Canada, the effects of tariffs, CFX standards, and much more—all designed to provide perspective as you move through the cloud bank of today's shifting economic market.
- Articles
- Columns
- Links
- Media kit
||| MENU - smt007 Magazine
Estimated reading time: 1 minute
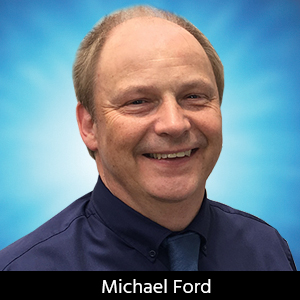
Smart Factory Insights: Dromology—Time-space Compression in Manufacturing
Dromology is a new word for most of us, I expect; it certainly is for me (and Microsoft Word). Dromology resonates as an interesting way to describe changes in the manufacturing process due to technical and business innovation over the last few years, leading us towards Industry 4.0. It is easy to lose track of the many changes that are happening, as our experience of the compression of time and space has taken place over many years. Paradigm shifts that new technologies enable today should not be surprises if the trends and direction of business needs are understood. Best practices going forward should be based on achievable goals, edge towards expected future business needs, and be driven by the opportunities that technologies bring. Let’s look at dromology in the assembly factory today.
Digital Manufacturing Engineering
We started with what was once industrial engineering. For many, the earliest applications of computer system technology in manufacturing were related to electronic product design and the entry of data into manufacturing. Previously, data was created through reverse engineering, taking measurements and paper drawings to feed the need for automation. What took weeks, if not months, could now be done in days using computers.
Though the use of engineering systems helped, it was not enough to change the paradigm. Production configurations continued to be defined and decided by engineering and driven through the singular assignment of product to line configuration. Best practices today, enabled by digital manufacturing engineering tools, have broken through to support the business need for flexibility, allowing products to be made on any configuration whenever needed as determined by the capability to deliver closest-to-completion requirements.
To read this entire column, which appeared in the November 2019 issue of SMT007 Magazine, click here.
More Columns from Smart Factory Insights
Smart Factory Insights: Making Rework a Smart Business OpportunitySmart Factory Insights: The Sustainability Gold Rush
Smart Factory Insights: Today’s Manufacturing Jobs Require a New Skill Set
Smart Factory Insights: Compose Yourself, Mr. Ford
Smart Factory Insights: The Smart Business Case for Local PCB Manufacturing
Smart Factory Insights: Manufacturing Digital Twin—Spanners in the Works
Smart Factory Insights: Machines, People, and AI
Smart Factory Insights: Is Sustainability in Manufacturing a Benefit or Burden?