-
- News
- Books
Featured Books
- design007 Magazine
Latest Issues
Current IssueAll About That Route
Most designers favor manual routing, but today's interactive autorouters may be changing designers' minds by allowing users more direct control. In this issue, our expert contributors discuss a variety of manual and autorouting strategies.
Creating the Ideal Data Package
Why is it so difficult to create the ideal data package? Many of these simple errors can be alleviated by paying attention to detail—and knowing what issues to look out for. So, this month, our experts weigh in on the best practices for creating the ideal design data package for your design.
Designing Through the Noise
Our experts discuss the constantly evolving world of RF design, including the many tradeoffs, material considerations, and design tips and techniques that designers and design engineers need to know to succeed in this high-frequency realm.
- Articles
- Columns
- Links
- Media kit
||| MENU - design007 Magazine
AltiumLive Frankfurt 2019: Carl Schattke Keynote
December 5, 2019 | Pete Starkey, I-Connect007Estimated reading time: 5 minutes
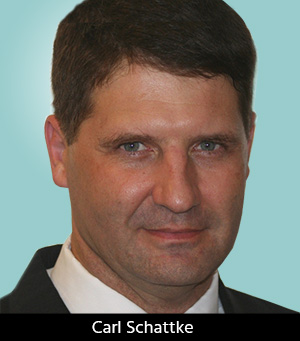
“How many here can remember manually taped artworks?” No more than three hands were raised in an audience of over 230 at the AltiumLive 2019 European PCB Design Summit in Frankfurt, Germany, as IPC Advanced Certified Interconnect Designer Carl Schattke introduced his keynote, entitled “Making and Breaking the Rules.”
Schattke had learned PCB layout as his father’s apprentice, hand-taping several hundred PCB designs in the 1970s and 1980s before becoming a CAD user with a Protel system—the precursor of Altium. He also ran a design bureaux , starting up a company designing acceleration systems for computer processing that was subsequently acquired by Intel. More recently, he has designed systems for advanced electric vehicles.
“If the design is possible, I can do it!” was Carl Schattke’s justifiable claim of capability, acknowledging that the manual experience gained in his early years gave him a positive advantage when tackling today’s complex designs. His objective had always been to achieve high reliability at low cost. Why rules? Schattke listed three points for discussion:
- Where have we been?
- What are the current issues with rules?
- Where do we see rules development going?
Tongue-in-cheek, he noted a quotation attributed to the Dalai Lama XIV: “Know the rules well, so you can break them effectively.”
So, where had he come from? What were the design rules that he had begun with? Schattke listed gridded Mylar, precision-slit tape (the choice of 15-mil, 30-mil, 50-mil, or 100-mil), photographic stickers for pads, working on the drawing board at 2x or 4x scale, followed by colour separation and camera reduction, measurement by ruler and monoscope, drill programming by bomb-sighting individual hole centres to produce NC tapes, fabrication drawings drafted manually and blueprinted, and design-rule checking by two people comparing the layout point-by-point with the schematic. Taping-up could take a couple of months. That all sounded familiar to PCB people of my generation, but most of us are retired or departed now, and that technology pre-dated most of the members of the audience.
“But then, this thing called CAD came along.” Schattke recounted some of the many shortcomings of crude-but-expensive early systems that had prompted him to revert to the traditional methods. “That was how we designed the computers that designed the computers that designed the computers we use now.”
It wasn’t until sometime later when Schattke tried the Protel system that he began to have any confidence in computer-aided design. That was 34 years ago. Protel developed into Altium Designer, and through several iterations, became the version in current use. Schattke commented that the company had always listened to the comments and suggestions of its users For example, Schattke had suggested automated the process of going from schematic to board, keeping track of everything along the way, and Altium did it.
One external factor that limited the scope of the early CAD systems was the capability of the available photoplotters—for example, the Gerber vector plotter with its D-codes, draws, flashes, and a 24-station physical aperture-wheel. But CAD succeeded in improving repeatability and reducing the skill level required to get a good result. And second-generation CAD tools were increasingly integrated, running on much faster computers, with more-complete libraries and interfaces to third-party tools, constraint rules, rules-driven routing, and software-driven rule writing, enabling increasingly complex design systems and enormous increases in design productivity.
What Schattke really came to talk about was rules. “How do we get our rules? How do we think about rules? How do we use rules? How does the software change with the rules that we use? And what kind of rules are we going to need in the future?” He reminisced about the days of making paper dolls to represent components, shuffling them around until the layout looked right and tacking them down while trying not to sneeze.
Where did the rules come from? Schattke referred to Altium’s constraint-based system and explained that rules could be either “unary,” which defined the required behavior of an object, or “binary,” which defined the interaction between two objects. He explained Altium’s set-up process, with examples of schematic-driven rules and PCB-driven rules, and asked the following questions: “What rules do we want to use, and what rules don’t we care about? When do we use rules, and when don’t we? How do we set the right rules, manage them, and validate them?”
Schattke discussed complicated clearance rules for high voltage and high current, special cases where clearances could be less than the rule, rules anomalies that caused occasional design-rule-ckeck failures, and rules not currently available that it would be nice to have, such as the distance to the return-path via for differential-pair transitions. The objective was always to achieve a clean design, free of design-rule-check violations.
Schattke listed some features of next-generation CAD tools: rapid integration of PCB and 3D mechanical design, rules-based routing, intelligent automation, intelligent peer-to-peer interchanges, rules-driven advanced library control and automation, seamless integration with task-specific design and checking tools—signal integrity, power integrity, design for manufacturing, design for assembly, electromagnetic compatitibility, in-circuit test, 3D CAD, layer stackup, high-density interconnect, antenna modelling, mechanical stress-analysis tools, and automated reliability modelling—as well as material-science integration for 3D-printed circuits, 3D-printing integration, and wearable circuit fabrics. The list went on. It was obviously incomplete, but the progession of CAD tools would continue as a combination of small continuous improvements and the occasional Eureka moment. Schattke quoted Stewart Brand’s advice on accepting, adapting to, and becoming part of big changes: “Once a new technology rolls over you, if you’re not part of the steamroller, you’re part of the road.”
One of the designer’s most important tools was the opportunity to communicate with manufacturers and engineers. Carl Schattke had already demonstrated his communication skills through a long and successful career in design. His philosophy was summarised in his final slide: “Position yourself to contribute by asking for the tool improvements to enable next-generation design and production, working on the hard problems that serve humanity in unique ways, improving your network to help you solve problems and be a problem solver, and teaching and training the next generation.”
Schattke’s concluding words of wisdom were, “A true legacy doesn’t just solve today’s problems; it positions others to solve tomorrow’s problems.” This comment rounded off a valuable and meaningful lesson on the no-nonsense realities of PCB design.
Suggested Items
DownStream Acquisition Fits Siemens’ ‘Left-Shift’ Model
06/26/2025 | Andy Shaughnessy, I-Connect007I recently spoke to DownStream Technologies founder Joe Clark about the company’s acquisition by Siemens. We were later joined by A.J. Incorvaia, Siemens’ senior VP of electronic board systems. Joe discussed how he, Rick Almeida, and Ken Tepper launched the company in the months after 9/11 and how the acquisition came about. A.J. provides some background on the acquisition and explains why the companies’ tools are complementary.
Elementary Mr. Watson: Retro Routers vs. Modern Boards—The Silent Struggle on Your Screen
06/26/2025 | John Watson -- Column: Elementary, Mr. WatsonThere's a story about a young woman preparing a holiday ham. Before putting it in the pan, she cuts off the ends. When asked why, she shrugs and says, "That's how my mom always did it." She asks her mother, who gives the same answer. Eventually, the question reaches Grandma, who laughs and says, "Oh, I only cut the ends off because my pan was too small." This story is a powerful analogy for how many PCB designers approach routing today.
Connect the Dots: The Future of PCB Design and Manufacturing
07/02/2025 | Matt Stevenson -- Column: Connect the DotsFor some time, I have been discussing the increasing complexity of PCBs and how designers can address the constantly evolving design requirements associated with them. My book, "The Printed Circuit Designer’s Guide to… Designing for Reality," details best practices for creating manufacturable boards in a modern production environment.
Siemens Turbocharges Semiconductor and PCB Design Portfolio with Generative and Agentic AI
06/24/2025 | SiemensAt the 2025 Design Automation Conference, Siemens Digital Industries Software today unveiled its AI-enhanced toolset for the EDA design flow.
Cadence AI Autorouter May Transform the Landscape
06/19/2025 | Andy Shaughnessy, Design007 MagazinePatrick Davis, product management director with Cadence Design Systems, discusses advancements in autorouting technology, including AI. He emphasizes a holistic approach that enhances placement and power distribution before routing. He points out that younger engineers seem more likely to embrace autorouting, while the veteran designers are still wary of giving up too much control. Will AI help autorouters finally gain industry-wide acceptance?