-
- News
- Books
Featured Books
- smt007 Magazine
Latest Issues
Current IssueSpotlight on India
We invite you on a virtual tour of India’s thriving ecosystem, guided by the Global Electronics Association’s India office staff, who share their insights into the region’s growth and opportunities.
Supply Chain Strategies
A successful brand is built on strong customer relationships—anchored by a well-orchestrated supply chain at its core. This month, we look at how managing your supply chain directly influences customer perception.
What's Your Sweet Spot?
Are you in a niche that’s growing or shrinking? Is it time to reassess and refocus? We spotlight companies thriving by redefining or reinforcing their niche. What are their insights?
- Articles
- Columns
- Links
- Media kit
||| MENU - smt007 Magazine
Estimated reading time: 5 minutes
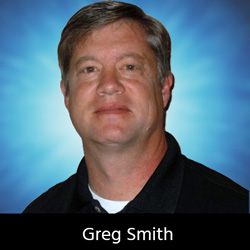
SMT Stencils 101: Root-cause Stencil Design, Part 3—Tearing Down Bridges
One thing that’s certain is that there are no guarantees for good board design. Many times, contract manufacturers are expected to successfully assemble components onto boards where the design is not optimized. This can be the case on pitch-type components, such as QFPs, BTCs, TSOPs, and many others.
One issue that commonly occurs is that the width of the copper land pad is larger than it should be; if the stencil is not designed properly, bridging can occur. If bridging at print occurs, the primary areas to address are aperture width and area ratio. The area ratio will determine what foil thickness should be used if that is in question.
Through many years and thousands of stencil designs, I feel the best design for pitch components is to set the width of the aperture to half of the pitch of the component leads. For instance, if the pitch is 15.7 (0.4 mm), the stencil aperture width should be 7.85 mils. Many stencil manufacturers will round up a 15.7-mil (0.4-mm) pitch component and call it 16-mil pitch when calculating the aperture width and will recommend or design the aperture to be 8 mils wide; the same is true for 19.7-mil pitch (0.5-mm) devices. Many stencil suppliers will make the aperture widths for these apertures 10 mils wide.
For land pad aperture length, I always recommend making them the length of the copper land pad on the PCB. Very rarely have there been bridging issues at print when this half-pitch rule is followed (Figure 1). The only caveat is that, if the copper pad is less than half of the pitch, you would design the stencil aperture to be the same width as the copper pad.
There are times the stencil is designed using the half-pitch rule, and yet customers still have bridging after print. In this case, the first question to ask is, “Are there solder dams between the copper land pads?” If there are no solder mask dams between apertures, the possibility for shorts exists. When this is the case, an additional 1-mil width reduction should be applied to reduce the possibility of bridging.
After calculating half the pitch to determine the width of the aperture and designing it so that the length is the same as the copper pad, the area ratio can then be determined. In general, area ratios should be greater than 0.60 for the material thickness required to obtain 80–100% of the theoretical volume of the stencil apertures when a ceramic nano-coating is not used.
Bridging at SMT Reflow: Causes for Bridging After Reflow When It Is Not Present After Print
When bridging occurs after reflowing but isn’t present after print, most often, that will happen on gull-wing, QFP-type devices (Figure 2).
Before beginning a root-cause analysis process for this type of defect, it is necessary to have a component datasheet (Figure 3) for the device being placed.
To identify a solution for this defect, one must look at the foot dimension (Lp) on the component datasheet (Figure 3) and compare it to the land pad on the copper layer of the PCB. In most cases, when the foot is much shorter than the land pad, bridging can occur. An example of this is shown in Figure 4.
The shoulder of the gull-wing lead is exposed to the convective heat of the oven and can heat up faster than the PCB land pad and foot of the component lead. As the component lead heats up, solder paste can become molten and wick up the lead. Once the solder reaches the top of the lead shoulder, there is no place for the liquid solder to travel. At this point, it can pool around the foot. If this happens to two leads next to each other, shorts or bridges can occur.
Here’s another way to describe it: If the gull-wing foot is 25% shorter or more than the length of the land pad of the board, thermal differences allow the foot of the lead to heat faster than the solder paste on the land pad of the board. As this occurs, the solder paste becomes liquidus at the foot first, and paste tends to wet up the lead, typically stopping close to the shoulder. At this point, because no more solder can wet up the lead, the liquid solder starts pooling around the foot of the component until the rest of the land pad heats and paste wets to the entire pad. On fine-pitch components, this pooling can spill out across the lead and bridge or short to the next lead. This phenomenon commonly occurs when the land pad is designed for a specific component, and the component is replaced by another similar component where the foot is too short for the length of the land pad on the PWB.
Reducing the paste volume printed on the land pad is necessary to prevent paste from pooling during reflow and causing bridges or shorts. The process to identify and correct this defect includes determining the length of the foot and comparing it to the length of the copper SMT pad on the PWB. If the foot of the component lead is 25% shorter than the length of the pad, the volume of paste deposited should be reduced by 10%. If the length of the lead is 50% shorter than the land pad, a 25% volume reduction should be made. Finally, if it is 70% shorter, then the volume should be reduced by 40%.
In addition to reducing the volume of paste printed on the land pad, it is also necessary to center the new, modified stencil aperture on the component foot. This process involves looking at the component drawing (Figure 3) and identifying the dimension HE and HD for the component being analyzed to determine the outer extents of the component feet to create a Gerber layer of the component feet centered according to the drawing. The new stencil apertures created to reflect the reduction in volume should be centered on this pattern (Figure 5). When the new apertures are used, the reduced paste volume will flow up to the aperture shoulder as it wets the land pad. The pooling will be eliminated, and bridging prevented with this new aperture design.
Next Column
In my next column, I will discuss stencil designs to reduce voiding on bottom-terminated components.
Greg Smith is manager of stencil technology at BlueRing Stencils.
More Columns from SMT Stencils 101
SMT Stencils 101: Root-cause Stencil Design, Part 2—TombstonesSMT Stencils 101: Root-cause Stencil Design, Part 1—Solder Balls
SMT Stencils 101: What Are Industry-standard Stencil Designs?
Overcoming the Challenges of Miniaturization with New Stencil Technologies–Solder Paste Release, Pt. 2
Overcoming the Challenges of Miniaturization with New Stencil Technologies, Part 1: Solder Paste Release
A Brief History of Solder Stencil Manufacturing