-
- News
- Books
Featured Books
- design007 Magazine
Latest Issues
Current IssueProper Floor Planning
Floor planning decisions can make or break performance, manufacturability, and timelines. This month’s contributors weigh in with their best practices for proper floor planning and specific strategies to get it right.
Showing Some Constraint
A strong design constraint strategy carefully balances a wide range of electrical and manufacturing trade-offs. This month, we explore the key requirements, common challenges, and best practices behind building an effective constraint strategy.
All About That Route
Most designers favor manual routing, but today's interactive autorouters may be changing designers' minds by allowing users more direct control. In this issue, our expert contributors discuss a variety of manual and autorouting strategies.
- Articles
- Columns
- Links
- Media kit
||| MENU - design007 Magazine
Estimated reading time: 3 minutes
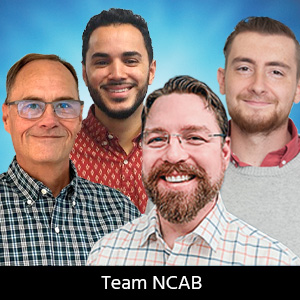
Fresh PCB Concepts: Create PCB Fabrication Notes for Success
One of the reasons I love being a field applications engineer for NCAB Group is that I’m able to interact with a large variety of customers who have different ideas and cool products to build. I’ve noticed that our clients increasingly understand that PCBs are the key component but still have challenges communicating to their PCB suppliers what they want to build. When we receive Gerber files for an order, there are times we cringe because we’re missing pieces of information necessary to make sure the PCB is made with zero defects. As we come back to work for the New Year, here are some key factors I wish customers would consider before they send their files.
One of the main things I wish customers would recognize is the need to update their documentation to match the Gerber data. As a PCB designer finishes routing their last trace, they’re so excited to send off the board that they omit the finishing touches. We call these finishing touches the fabrication notes, or fab notes, and they’re often overlooked. Have you checked if the revision is updated? Is a part number included to help differentiate? If you have generic notes for each board, do they apply to this one? While these checks won’t necessarily hold up a factory, it is a possibility. Don’t we want to be as precise as possible when designing such a complex product? All these factors impact the overall quality.
The fab notes are also important for details like the drill table, board stackup, and dimensions. If these don’t match the Gerber files or are inconsistent, the factory will hold the board until the questions are resolved. This could waste hours or even days when a simple update can avoid this problem completely. If you have a drill table (in addition to an NC drill file), make sure to update this so that it matches the Gerber data. Your design software will update this with a click of a button, and that small action will reduce confusion and additional questions. The same goes for the board stackup file if it’s embedded into a Gerber file. The added benefit of this is when you export the Gerber as a PDF, you can easily refer to the fab notes to understand how many layers and holes your design has.
Another thing I wish our customers would consider is the materials needed to build the specific PCB. While most boards default to FR-4 material, we deal with some that have a specific material callout. This is great for understanding the customer application, but the drawback is when those materials are uncommon, it will cause increased lead times to obtain the material, or a factory will refuse to build the board altogether. This is more common with companies that have many years of experience in designing and/or building PCBs, but we also see it with engineers that are designing their first high-speed or high-Tg board.
Keep in mind that the PCB manufacturing process is mostly chemical. There are so many steps that require proper chemical balances, and new laminate materials create uncertainties. If possible, indicate whether or not equivalents are acceptable. I also recommend specifying material per IPC specifications (i.e., IPC 4101-126). If a factory recommends another material and they have experience with it, you can ask for the board stackup or impedance calculations to make sure both the designer and factory feel comfortable with proposed changes.
A final thing I wish customers would do is to update their design rules. These design rules ensure the size of features like component pads, vias, and traces. They also help with spacing between different features across the entire PCB. We’re always pushed to make things smaller and closer together, but you could be setting yourself up for failure if you’re not working with a suitable factory from the beginning. To design a board that is easily manufactured, ask for the factory’s design rules. That way, the factory will know they can build a board with those specs under most conditions.
Creating a quality PCB on time with zero defects is a team effort. While there are standard specifications, there are almost always exceptions as well. Although a PCB is technical and precise, it is also a piece of art. Each one is unique and has variations to the rules. Helping your PCB supplier will save time that’s wasted clarifying information and asking additional questions. The actions I’ve mentioned should be implemented into your normal routine before releasing a board in order to obtain the best quality on time and at the lowest total cost.
Harry Kennedy is a field application engineer at NCAB Group.
More Columns from Fresh PCB Concepts
Fresh PCB Concepts: Designing for Success at the Rigid-flex Transition AreaFresh PCB Concepts: More Than Compliance—A Human-centered Sustainability Approach
Fresh PCB Concepts: Assembly Challenges with Micro Components and Standard Solder Mask Practices
Fresh PCB Concepts: The Power of a Lunch & Learn for PCB Professionals
Fresh PCB Concepts: Key Considerations for Reliability, Performance, and Compliance in PCBs
Fresh PCB Concepts: Traceability in PCB Design
Fresh PCB Concepts: Tariffs and the Importance of a Diverse Supply Chain
Fresh PCB Concepts: PCB Stackup Strategies—Minimizing Crosstalk and EMI for Signal Integrity