-
- News
- Books
Featured Books
- smt007 Magazine
Latest Issues
Current IssueSupply Chain Strategies
A successful brand is built on strong customer relationships—anchored by a well-orchestrated supply chain at its core. This month, we look at how managing your supply chain directly influences customer perception.
What's Your Sweet Spot?
Are you in a niche that’s growing or shrinking? Is it time to reassess and refocus? We spotlight companies thriving by redefining or reinforcing their niche. What are their insights?
Moving Forward With Confidence
In this issue, we focus on sales and quoting, workforce training, new IPC leadership in the U.S. and Canada, the effects of tariffs, CFX standards, and much more—all designed to provide perspective as you move through the cloud bank of today's shifting economic market.
- Articles
- Columns
- Links
- Media kit
||| MENU - smt007 Magazine
LPKF Introduces New Depaneling Laser Systems at IPC APEX EXPO 2020
January 31, 2020 | LPKF Laser & ElectronicsEstimated reading time: 3 minutes
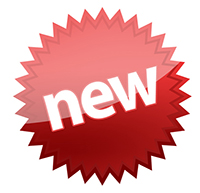
LPKF Laser & Electronics is introducing the LPKF CuttingMaster family of laser depaneling systems for rigid and flex PCBs at IPC APEX EXPO. Available with different laser sources, power levels and two different working areas, the CuttingMaster 2000 and CuttingMaster 3000 systems are suited to achieve the highest quality results for nearly every depaneling task. LPKF’s proprietary CleanCut Technology allows for even the most demanding applications which require absolute cleanliness of the cutting edges to be processed with lasers.
The CuttingMaster 2000 series is a highly cost-effective laser depaneling system. Its very compact footprint saves valuable space on the production floor while it still provides an effective working area to handle panels up to 350 mm x 350 mm (13.8” x 13.8”). It is available either as a stand-alone system or as an in-line configuration with integrated conveyor system. The high-throughput and clean cutting quality is comparable to mechanical depaneling methods, but with none of the dust or debris, while the low investment cost allows for a very attractive ROI.
The CuttingMaster 3000 series provides a larger working area to handle panels up to 500 mm x 350 mm (19.7” x 13.8”) and high speed and high precision linear motor drive system with a rigid granite construction that provides exceptional positioning accuracy for high-end-applications. The CuttingMaster 3000 is also available in a stand-alone configuration or in-line integration for SMT lines. The ability to integrate a wide range of different laser sources with different wave lengths and pulse durations in both the nanosecond and picosecond range allows these systems to be deployed for a wide range applications and materials, including drilling applications.
The systems come with powerful LPKF CircuitPro system software, which is perfectly matched to the hardware and designed for easy-to-use operation without expert knowledge. CircuitPro is compatible with all standard data formats and standard interfaces used in PCB production. Custom MES connectivity, multi-fiducial detection, bad-board recognition and full product traceability are also available to optimize the production efficiency of the LPKF CuttingMaster system in the SMT assembly process. All LPKF CuttingMaster systems are available as a stand-alone or inline solution. (Fig. 2) They are prepared for 24/7 production. In addition to these systems, LPKF will also be demonstrating its laser plastic welding systems and rapid PCB prototyping technology at the show. For more information on LPKF’s latest laser-based solutions, visit LPKF in booth 3653 at the 2020 IPC APEX EXPO or visit www.lpkfusa.com.
Why considering Laser Depaneling at all?
Laser depaneling has numerous advantages compared to conventional depaneling processes: The contactless processing is a completely stress-free method for the workpiece. As the surrounding material is not affected, cutting edges can be made directly next to components, which increases the usable space on the circuit board and saves material, especially in the case of full cuts. Laser depaneling also avoids any airborne dust and debris contamination of the work piece, which completely eliminates any post-processing or cleaning, and improves both production yield and long-term product reliability. LPKF’s CleanCut technology mitigates carbonization and produces clean, sealed sidewalls without any chipping or frayed glass fibers that are often seen with mechanical depaneling methods.
The laser produces very narrow cutting channels with very high precision and no limitation to the shape or design of the cut. It can process a wide variety of flexible and rigid materials. The laser-beam-guided process requires no tooling and does not wear, which can result in considerable savings in consumable expenses.
LPKF laser depaneling systems are designed and built for 24/7 production and are perfectly suited to sensitive applications in a wide variety of industries such as medical technology, automotive, and consumer electronics.
About LPKF
Established in 1976, LPKF Laser & Electronics manufactures cutting, welding and prototyping systems used in circuit board and microelectronics fabrication, medical technology, and the automotive sector. LPKF’s worldwide headquarters is located in Hannover, Germany and its North American headquarters resides near Portland, OR.
Testimonial
"Advertising in PCB007 Magazine has been a great way to showcase our bare board testers to the right audience. The I-Connect007 team makes the process smooth and professional. We’re proud to be featured in such a trusted publication."
Klaus Koziol - atgSuggested Items
Nordson Reports Q3 Fiscal 2025 Results and Updates Full Year Guidance
08/21/2025 | BUSINESS WIRENordson Corporation reported results for the fiscal third quarter ended July 31, 2025. Sales were $742 million compared to the prior year’s third quarter sales of $662 million.
Haylo Labs Acquires Plessey Semiconductors
08/20/2025 | Haylo LabsHaylo Labs has acquired Plessey Semiconductors, the UK’s leading innovator in microLED display technology.
SoftBank Group and Intel Corporation Sign $2B Investment Agreement
08/19/2025 | Intel CorporationSoftBank Group Corp. and Intel Corporation today announced their signing of a definitive securities purchase agreement, under which SoftBank will make a $2 billion investment in Intel common stock.
20 Years of Center Nanoelectronic Technologies (CNT) – Backbone of German Semiconductor Research Celebrates Anniversary
08/14/2025 | Fraunhofer IPMSThe Center Nanoelectronic Technologies (CNT) of the Fraunhofer Institute for Photonic Microsystems (IPMS) is celebrating its 20th anniversary this year. Since its founding in 2005, it has developed into a pillar of applied semiconductor research in Germany and Europe. With its unique research cleanroom and equipment adhering to the 300-mm wafer industry standard, CNT is unparalleled in Germany and serves as a central innovation driver for the microelectronics industry.
A.R.T. Ltd. Nominated in Four Categories at 2025 Instrumentation and Electronics Industry Awards
08/11/2025 | A.R.T. Ltd.Advanced Rework Technology Ltd. (A.R.T. Ltd.), a leading provider of electronics training and consultancy, has been shortlisted in four categories at the 2025 Instrumentation and Electronics Industry Awards, including Industry Personality, Academic Support, Rising Star, and Best Customer Service.