-
- News
- Books
Featured Books
- design007 Magazine
Latest Issues
Current IssueAll About That Route
Most designers favor manual routing, but today's interactive autorouters may be changing designers' minds by allowing users more direct control. In this issue, our expert contributors discuss a variety of manual and autorouting strategies.
Creating the Ideal Data Package
Why is it so difficult to create the ideal data package? Many of these simple errors can be alleviated by paying attention to detail—and knowing what issues to look out for. So, this month, our experts weigh in on the best practices for creating the ideal design data package for your design.
Designing Through the Noise
Our experts discuss the constantly evolving world of RF design, including the many tradeoffs, material considerations, and design tips and techniques that designers and design engineers need to know to succeed in this high-frequency realm.
- Articles
- Columns
- Links
- Media kit
||| MENU - design007 Magazine
Solder Paste Printing From the Stencil’s Perspective
February 19, 2020 | I-Connect007 Editorial TeamEstimated reading time: 22 minutes
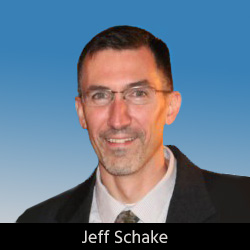
Jeff Schake of ASM Assembly Systems discusses the complications surrounding printing and solder paste that he sees from his perspective as a stencil expert.
Barry Matties: Let’s start with some of your background.
Jeff Schake: The division I work for is what was formerly DEK Printing Machines. I work on the printing end, and I’ve been with them for 21 years. My role has been the same since I was hired. I’ve worked in a research and development role. I report to ASM’s Product Line Innovation Center in the Weymouth, U.K., factory where our printers are designed, engineered, and manufactured. I specialize in conducting R&D process projects focused on printing and expanding our knowledge of the behaviors of the printing process. I report that back into the factory to improve our products and knowledge.
I also participate in standards groups and publish the research in proceedings at IPC APEX EXPO, SMTAI, and other conferences. I’m based in the U.S., and for the past few years, I’ve been stationed at the Rochester Institute of Technology CEMA Lab to conduct my projects. Professor Martin Anselm of RIT is the director of this world-class electronics manufacturing laboratory, and ASM has kindly contributed state-of-the-art printing and placement machines into the SMT assembly line there. In that facility, we have the full capability of assembly, inspection, various reliability testing tools, and failure analysis equipment. I enjoy spending time in there doing my projects and interacting with students.
Matties: One of your specialties is also statistical analysis.
Schake: Yes. Anytime you run an experiment, you have to analyze the data.
Matties: In this issue, we are focusing on finer pitch dimensions. We’ve done some research, and everything keeps coming back to printing and getting the stencils and solder paste on the board right. What trends do you see in the printing process?
Schake: The fundamental challenges haven’t changed from where we were 10–20 years ago, but what’s different now is the measurement scale associated with these challenges. Instead of working in a scale of millimeters, we’re down to microns now. We’re trying to assemble metric 0201 passives instead of 0402s. As you would expect, the stencil design is significantly impacted by this miniaturization trend. Aperture sizes are smaller, and stencil foils are thinner. The tough part with stencils and printing comes when miniaturization mixes in with larger legacy components designed on the same board.
In this scenario, designing the stencil with intent to print the smallest pads optimally, which is the typical strategy, may fall short of printing enough solder paste volume on the largest pads because the stencil foil is so thin. To boost the print volume printed on those larger pads, a thicker stencil foil may be required, but in doing so, this may compromise the ability to print controlled paste volume on the smallest pads. We refer to this as the “heterogeneous assembly challenge” within our in-house discussions, but I’ve also heard this referred to as “broadband assembly,” too. Call it what you want, but the main trend to highlight here is the range of component sizes continuing to expand, which is making it harder to design and implement uniform thickness stencils that will work in these scenarios.
Of course, there are tricks that you can play to enhance the print performance of the stencil, like adding nano-coatings to them. Nano-coatings represent a class of proprietary chemistries engineered to repel flux. These materials are applied to the bottom side of the stencil and were originally intended to inhibit paste and flux residue from bleeding out the bottom of the aperture holes and contaminating the stencil foil. But most of the technical papers you’ll find that address the benefits of nano-coatings will feature their claimed influence to improve solder paste transfer and print volume repeatability, which is helpful for challenging heterogenous applications.
We also see an increase in the use of dual-thickness or stepped stencils as a means to achieve printing a wider range of print volumes. A relatively new technology to fabricate stepped stencils utilizes the laser cutting machine that, in addition to cutting aperture holes, can be used to laser weld thinner or thicker foil pieces into the stencil foil. It’s so convenient, and with the programmability aspect of using the laser tool to do this, it lends itself nicely towards improved step resolution not achievable by traditional wet chemistry etch stepping techniques.
As we strive to push the limits of printing to finer dimensions, we see research published on details of the stencil, you wouldn’t have paid much attention to a decade ago. Take, for instance, the surface roughness of laser cut aperture walls and how this impacts solder paste transfer. Not only is the cutting equipment being improved to produce more uniform holes, but new foil material options exist today we didn’t have available before that have been identified to contain unique properties that allow them to be cut better. A higher class of stainless steel stencil foil material, which we generically call “fine grain,” has emerged claiming to offer cleaner cut and smoother aperture holes. Yes, this is a very subtle detail, but taken alone, this may not by itself produce a significant leap in printing capability improvement. However, all these details working collectively together—like fine-grain foils, nano-coatings, higher-quality laser cutting tools, advancements in solder paste formulations in use today, along with the print performance improvements achievable by modern-day printing machines—can achieve impressive printing capability gains to accommodate heterogeneous assembly challenges.
In reference to my involvement on the IPC 5-21E committee addressing the IPC 7525 stencil design guideline standard, we recognize the challenge of heterogeneous printing compels people today to use stencil designs containing aperture sizes smaller than our standard recommends. What I’m getting at here is the minimum area ratio stencil design guideline, which is currently prescribed in the standard as a value of 0.66. This figure is outdated and doesn’t reflect the print process capability that is achievable today using modern materials and equipment, so one of the changes that you’ll see in the next Rev C document will be a reduction to the minimum prescribed aperture area ratio.
Nolan Johnson: You’re saying we’re getting down to dimensions where you start to pay attention to things like the metal grain.
Schake: Sure! If you’ve seen all the items listed on the infamous printing process fishbone chart, you know there are so many variables that can impact printing. As the saying goes, “leave no stone unturned.” In fact, there are a handful of conference papers out there documenting printing capability as a function of stencil foil material grain size. The published papers on this topic typically support the use of fine-grain stencils as a means of achieving improved print performance. I believe there’s a correlation between the cosmetic quality of the cut stencil to its capability to print, and fine grain does play into this logic. Apertures cut using a finer grain material probably tend to have less of a wall texture, and the influence of this offers the possibility to benefit printing control. But, as I mentioned before, it’s more likely that it will take a collection of such incremental improvements working in harmony to realize the significant print performance boost we’re all looking for.
Holden: The interesting thing about where you are is that the whole assembly process starts with the solder paste printing. If it doesn’t go exactly right, it can’t get any better going down the assembly line. I’m familiar with DEK printers that we used in Hewlett-Packard. Regarding laser-cutting stencils, do they still do photochemical machining of stencils and stainless steel stencils?
Schake: Chemically etched stencil technology has pretty much dropped away except for the purpose of still using it for creating steps in stencils. Machine-drilled stencils are uncommon except for niche glue and adhesive print applications where thick plastic masks are used. Stainless steel laser-cut stencils account for the majority of stencils currently produced.
Holden: Is there a need for multiple thickness stencils? It’s a dilemma when you’re trying to do mixed parts that are fine and big because you only have a certain pad size and stencil thickness. Is there some flashy way now to get more paste than the thickness of your stencil determines?
Schake: Yes, there is a growing demand for multiple thickness stencils. This is yet another example of how heterogeneous assembly designs are influencing stencil design solutions, which may use step-downs arranged to print smaller deposits on the pads of critical fine pitch components. Step-up stencils are also a possibility and use selectively thicker stencil foil to increase the print volume required on large pads and connector-type parts, for example.
As for getting more paste than the thickness of the stencil permits, the laws of physics still apply, and the thickness of the printed paste brick is ultimately defined by this. That being said, I do recall an academic paper published many years ago out of Germany that did report printing solder paste deposits thicker than the physical stencil foil. The stencil foil used was produced with a matrix of highly co-planar micro-standoffs attached on its bottom side, so the printing that was demonstrated was essentially off contact extrusion printing.
Holden: Earlier today, I watched videos on 3D printing, especially 3D printing of metal and stainless steel. I thought, “Why not selectively print a stainless steel stencil with various thickness of the stencil? If you need more precision afterward, you can refine it with laser cutting or trimming of the stencil.” They put it upside down, so the squeegee side would be flat, but the other side would have various thicknesses in the stencil.
Schake: In my view, the logic is reversed. The flat side of the stencil needs to contact the board you’re printing onto to maintain a sufficient gasket so that you’re not going to bridge. The apertures on the contact side of the stencil need to be sealed against the board to prevent solder paste particles and flux from escaping; ideally, to achieve this, you have two flat surfaces in contact. In the scenario you described, it would be better to present the topographical side of the stencil foil that has different thicknesses levels to the squeegee side. Metal squeegees may not work the best, though, if you have multiple thickness levels or significant step displacements to deal with, but maybe that’s an application better suited to an old-fashioned polyurethane squeegee. It’s an interesting possibility!
Page 1 of 3
Suggested Items
Driving Innovation: Direct Imaging vs. Conventional Exposure
07/01/2025 | Simon Khesin -- Column: Driving InnovationMy first camera used Kodak film. I even experimented with developing photos in the bathroom, though I usually dropped the film off at a Kodak center and received the prints two weeks later, only to discover that some images were out of focus or poorly framed. Today, every smartphone contains a high-quality camera capable of producing stunning images instantly.
Hands-On Demos Now Available for Apollo Seiko’s EF and AF Selective Soldering Lines
06/30/2025 | Apollo SeikoApollo Seiko, a leading innovator in soldering technology, is excited to spotlight its expanded lineup of EF and AF Series Selective Soldering Systems, now available for live demonstrations in its newly dedicated demo room.
Indium Corporation Expert to Present on Automotive and Industrial Solder Bonding Solutions at Global Electronics Association Workshop
06/26/2025 | IndiumIndium Corporation Principal Engineer, Advanced Materials, Andy Mackie, Ph.D., MSc, will deliver a technical presentation on innovative solder bonding solutions for automotive and industrial applications at the Global Electronics A
Fresh PCB Concepts: Assembly Challenges with Micro Components and Standard Solder Mask Practices
06/26/2025 | Team NCAB -- Column: Fresh PCB ConceptsMicro components have redefined what is possible in PCB design. With package sizes like 01005 and 0201 becoming more common in high-density layouts, designers are now expected to pack more performance into smaller spaces than ever before. While these advancements support miniaturization and functionality, they introduce new assembly challenges, particularly with traditional solder mask and legend application processes.
Knocking Down the Bone Pile: Tin Whisker Mitigation in Aerospace Applications, Part 3
06/25/2025 | Nash Bell -- Column: Knocking Down the Bone PileTin whiskers are slender, hair-like metallic growths that can develop on the surface of tin-plated electronic components. Typically measuring a few micrometers in diameter and growing several millimeters in length, they form through an electrochemical process influenced by environmental factors such as temperature variations, mechanical or compressive stress, and the aging of solder alloys.