-
- News
- Books
Featured Books
- design007 Magazine
Latest Issues
Current IssueAll About That Route
Most designers favor manual routing, but today's interactive autorouters may be changing designers' minds by allowing users more direct control. In this issue, our expert contributors discuss a variety of manual and autorouting strategies.
Creating the Ideal Data Package
Why is it so difficult to create the ideal data package? Many of these simple errors can be alleviated by paying attention to detail—and knowing what issues to look out for. So, this month, our experts weigh in on the best practices for creating the ideal design data package for your design.
Designing Through the Noise
Our experts discuss the constantly evolving world of RF design, including the many tradeoffs, material considerations, and design tips and techniques that designers and design engineers need to know to succeed in this high-frequency realm.
- Articles
- Columns
- Links
- Media kit
||| MENU - design007 Magazine
Joe Clark Says DownStream Is Ready for More Growth in 2020
February 20, 2020 | Kelly Dack, CID+, EPTACEstimated reading time: 8 minutes
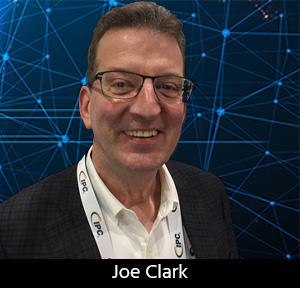
Joe Clark, co-founder of DownStream Technologies, gives Kelly Dack an overview of the company and their innovative product line, which serves to smooth the bumps that can occur between source design output and manufacturing line input. As Joe explains, 2019 was a great year for the company, and he expects that trend to hold through 2020.
Kelly Dack: Here we are, the first day of IPC APEX EXPO in San Diego. Beautiful weather. And with me is a beautiful gentleman, Joe Clark from Downstream Technologies.
Joe Clark: Thank you very much, Kelly. Always good to talk with you.
Dack: Welcome, Joe. At Downstream, I hear you’ve had a wonderful year and I want Joe to tell us about it and give us an inkling why. Things are on the way up…
Clark: And it continues to be strong. Kelly, 2019 was a record year for us. We achieved over 25% growth and a lot of that in what we like to call “new logos,” new customers. And the majority of it was in America, which is our backyard. Why that growth?
I think there are several factors. We've talked before about our vision when we created Downstream Technologies and our name describes where we fit into the process. We like to call ourselves the PCB post-processing company and our vision, this is now 20 years ago, was that companies would look to improve their hand-off, their integration between design and manufacturing. And indeed that's what is happening. And as companies look to improve that hand-off, the tools need to go mainstream, and they're now going to be rolled out to the designers.
So what you want is a high-functionality tool that is of high ease-of-use and low cost of ownership. And that's always been our niche. So I think we’ve seen a lot of talk and papers about what I'll call the NPI process, new product introduction, and in fact it's accelerated in the past few years, especially this past year with our new release enabled by the acceptance of the intelligent design exchange form. That's like IPC-2581, which has been the vehicle that's propelled and enabled companies to actually improve that hand-off.
Dack: Yes. You're known for being early in the game, so to speak, for supporting that intelligent data format and you’ve supported IPC-2581 ever since. And how is that working with all of your products now? Tell us about your products.
Clark: All of our products read and write IPC-2581 as well as ODB++, the Mentor intelligent format. And again, we don't look at that phase between the design space and the manufacturing space as a series of steps. It's really one step. It's taking that virtual design and analyzing it and preparing it to be manufactured. And that's what companies care about today. Whether the manufacturing facility is captive or external. So all of our tools work in that environment to take the virtual design, analyze it, compare it to the capabilities of the fabricator, the contract manufacturer and produce the files and formats and information so I can actually build the board. Including documentation, which has been…
Dack: Neglected?
Clark: Yes. It's the neglected un-sexy part of the process. But we all have to do it.
Dack: It’s so important. For instance, raw data by itself. I don't think there's any data in the world that's going to tell you what color to make your printer circuit board. I don't think that's part of ODB++ yet, is it? The color of your solder mask?
Clark: Well, it can be an attribute in the intelligent database.
Dack: I guess you could.
Clark: I can say “I want my solder mask green.”
Dack: And a legend. You could do that too?
Clark: Absolutely. More is coming and one of the things we're working on here at the show is the Rev C of 2581 which completes the support for rigid-flex, which is becoming a real design challenge for all companies. And with the success we've had, the companies that we're dealing with are dealing with rigid-flex designs.
Dack: So for our designers out there, it's not as much as just pressing a button and exporting ODB++ data that will put everything into a database output. There are more things that could be added.
Clark: Absolutely. Here's a classic example. I do my design and now I'm going to manufacture it, but I'm going to a manufacture it four-up. So there's another phase here of the design process, which is that I need to take the one-up PCB design in an assembly panel and I want to take that assembly panel and include that in the manufacturing design data that I'm going to send out to my fabricator. So there's more being defined as the committee gets together and takes input from the IPC community. And so we're just on the tip of the iceberg. A lot of possibilities.
Dack: Great. So, tell us how DFMStream works. Let's take a 10,000-foot flyover.
Clark: I can set up my rules for my particular fabricator or fabricators. I bring in my design, load it into DFMStream and I run all my checks, spacing checks, copper pour checks, and on and on and on, against that particular fabricator. I get a thumbs up or thumbs down if there are errors, and the errors are highlighted in the actual design, which is based on the ODB or the 2581, for me to make corrections. Not in the ODB or the 2581. Just like we never edited Gerbers, right?
Page 1 of 2
Suggested Items
Driving Innovation: Direct Imaging vs. Conventional Exposure
07/01/2025 | Simon Khesin -- Column: Driving InnovationMy first camera used Kodak film. I even experimented with developing photos in the bathroom, though I usually dropped the film off at a Kodak center and received the prints two weeks later, only to discover that some images were out of focus or poorly framed. Today, every smartphone contains a high-quality camera capable of producing stunning images instantly.
Hands-On Demos Now Available for Apollo Seiko’s EF and AF Selective Soldering Lines
06/30/2025 | Apollo SeikoApollo Seiko, a leading innovator in soldering technology, is excited to spotlight its expanded lineup of EF and AF Series Selective Soldering Systems, now available for live demonstrations in its newly dedicated demo room.
Indium Corporation Expert to Present on Automotive and Industrial Solder Bonding Solutions at Global Electronics Association Workshop
06/26/2025 | IndiumIndium Corporation Principal Engineer, Advanced Materials, Andy Mackie, Ph.D., MSc, will deliver a technical presentation on innovative solder bonding solutions for automotive and industrial applications at the Global Electronics A
Fresh PCB Concepts: Assembly Challenges with Micro Components and Standard Solder Mask Practices
06/26/2025 | Team NCAB -- Column: Fresh PCB ConceptsMicro components have redefined what is possible in PCB design. With package sizes like 01005 and 0201 becoming more common in high-density layouts, designers are now expected to pack more performance into smaller spaces than ever before. While these advancements support miniaturization and functionality, they introduce new assembly challenges, particularly with traditional solder mask and legend application processes.
Knocking Down the Bone Pile: Tin Whisker Mitigation in Aerospace Applications, Part 3
06/25/2025 | Nash Bell -- Column: Knocking Down the Bone PileTin whiskers are slender, hair-like metallic growths that can develop on the surface of tin-plated electronic components. Typically measuring a few micrometers in diameter and growing several millimeters in length, they form through an electrochemical process influenced by environmental factors such as temperature variations, mechanical or compressive stress, and the aging of solder alloys.