-
- News
- Books
Featured Books
- smt007 Magazine
Latest Issues
Current IssueSupply Chain Strategies
A successful brand is built on strong customer relationships—anchored by a well-orchestrated supply chain at its core. This month, we look at how managing your supply chain directly influences customer perception.
What's Your Sweet Spot?
Are you in a niche that’s growing or shrinking? Is it time to reassess and refocus? We spotlight companies thriving by redefining or reinforcing their niche. What are their insights?
Moving Forward With Confidence
In this issue, we focus on sales and quoting, workforce training, new IPC leadership in the U.S. and Canada, the effects of tariffs, CFX standards, and much more—all designed to provide perspective as you move through the cloud bank of today's shifting economic market.
- Articles
- Columns
- Links
- Media kit
||| MENU - smt007 Magazine
Estimated reading time: 4 minutes
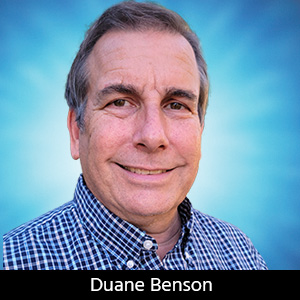
Powerful Prototypes: An Open-Source Adventure
I’m a marketer in my day job, but I’ve fully never let go of the technical aspects of this industry that I have such passion for. I still design electronics in my off-hours. Designing things as a part-time avocation is my version of “gardening to relax.” It also conveniently keeps me connected with customers and gives me some additional perspective on what engineers need when getting boards into an assembly factory and back out in working order.
The other quite handy aspect of me designing boards part-time is that I make mistakes. I've been at this job for nearly 15 years, and I have worked with electronics for considerably longer. I should know how to do this without errors, and yet I still always make some sort of mistake. Perhaps that is part of why I’m a marketing person rather than a full-time engineer, or perhaps not; the world may never know.
On the one hand, those mistakes are frustrating for me and the folks processing my orders. On the other hand, it gives us a close up look at how difficult getting things built really is out in the real world.
The Latest Project
My latest project is a motion-sensitive lapel pin for the Open Source Hardware Summit in New York City on March 13, 2020. The final version uses a Microchip PIC18F46K22 microcontroller (MCU) and an NXP MMA8452 accelerometer (both in small QFN packages) and will be 1.3” x 1.6” powered by a single CR2023 coin cell. I used 0402 LEDs and 0201 passives wherever possible.
Design Compromise
I wanted to make it as small as possible. I picked a CR2032 coin cell because, at 20 mm wide, I could keep the board width to one inch and still have a bit of clearance on each side. Unfortunately, the CR2032 surface mount battery holder uses two little wings out each side for soldering. The dimension with wings dictated the minimum width of the board of 1.3”. On the plus side, I used the extra space created on the front of the board to put my logo and that of Sunstone Circuits, who made the blank PCBs for me (Figure 1).
Figure 1: Wider than an inch.
I have used most of this design before. It came from an electronic business card holder I made a while back. The accelerometer senses motion, waking up the MCU. The MCU flashes a pattern on the LEDs and then goes back to sleep. In this case, I decided to add a small MOSFET so that I could brighten and dim all of the LEDs at the same time wiring a pulse width modulation signal from the MCU. That would give me more options with the pattern, and I would be able to dim the 21 LEDs to save on battery power (Figure 2).
Figure 2: MOSFET with footprint.
I had used the MCU and accelerometer before, so I had good footprints for both of those. I needed a footprint for the super tiny SMT switch. Sometimes, I make my own footprints, but I try not to if at all possible. It’s too easy to introduce errors in a footprint that will cause problems down the line. In this case, I downloaded the switch symbol and footprint from SnapEDA.
The First Mistake
Remember the MOSFET I mentioned earlier? I set up all of the LEDs with a common cathode and ran the cathode through the MOSFET to ground. As with everything else, I wanted to use the smallest parts possible. I used 5-mA LEDs and would be driving them at a partial duty cycle, so a really small MOSFET would do the trick. At 100% duty cycle, they would only be drawing 105 mA.
I found a logic level part by On Semiconductor—NTNS3193NZT5G with 224 mA drain-to-source current—which was plenty enough to do what I want with more than 50% headroom. It’s a very tiny part at just 0.62 x 0.62 mm in a three-pin land grid array (LGA) package.
Three pads can’t be too difficult, right? Well, it isn't difficult, but I ended up introducing one of those errors I mentioned. Fortunately, it still operates, but any of you who attend the conference and pick one up will be able to see my mistake. You’ll need a high-powered loupe or a microscope (as I said, the part is only 0.62 mm square).
The pads for the gate and source are each about ? the side of the drain pad. Whenever you have a pad that is significantly larger or smaller than the other pad(s), expect trouble—especially at such small geometries. I made the large drain pad too small, so when in the reflow oven, there wasn’t enough area for the solder to spread out. The parts ended up tilted on one side. As I said, it still worked, but it looks ugly in a very miniature way.
The Second Mistake
That was with the 10 prototype boards. It caused even more problems when I had the 400 built to give away. I noticed the problem after I had sent in the higher volume order, but before it had been built. I assumed that since all 10 of the prototypes worked fine, it would be okay in production too. Not a good assumption.
Building 10 is not the same as building 400. On a high-speed, high-volume pick-and-place machine, the solder deposition is even more critical than on a slower prototype pick and place. The boards will all work in the end, but I caused a lot of unnecessary rework by making a mistake on that one small footprint. The smaller the part, the more critical it is to get all of the details right.
Conclusion
Those were not my only misadventures with this board, but the rest are stories for another day. Suffice it to say that, as a maker, I’m pretty lucky to have a professional electronics assembly factory (and a very friendly board fabrication company) at my disposal.
Duane Benson is marketing manager and CTO at Screaming Circuits.
More Columns from Powerful Prototypes
Powerful Prototypes: Small Computer ModulesPowerful Prototypes: A Trip Back to the Basics
Powerful Prototypes: The Work World in 2021
Powerful Prototypes: Why Datasheets Matter
Powerful Prototypes: Manufacturing in an Uncertain World
Powerful Prototypes: Five Technological Shifts in the New Decade
Powerful Prototypes: Cost Reduction in Design
Powerful Prototypes: New PCB Fab Technology—What You Need to Know