-
- News
- Books
Featured Books
- smt007 Magazine
Latest Issues
Current IssueSupply Chain Strategies
A successful brand is built on strong customer relationships—anchored by a well-orchestrated supply chain at its core. This month, we look at how managing your supply chain directly influences customer perception.
What's Your Sweet Spot?
Are you in a niche that’s growing or shrinking? Is it time to reassess and refocus? We spotlight companies thriving by redefining or reinforcing their niche. What are their insights?
Moving Forward With Confidence
In this issue, we focus on sales and quoting, workforce training, new IPC leadership in the U.S. and Canada, the effects of tariffs, CFX standards, and much more—all designed to provide perspective as you move through the cloud bank of today's shifting economic market.
- Articles
- Columns
- Links
- Media kit
||| MENU - smt007 Magazine
Estimated reading time: 5 minutes
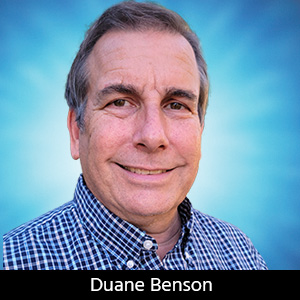
Powerful Prototypes: Manufacturing in an Uncertain World
In the best of times, electronics manufacturing is an exercise in taking chaos (in the form of data and information of multiple non-aligned forms and formats) and creating order (in the form of a working PCB). As I write this, it is not the best of times. The coronavirus has been declared a global pandemic, and the primary theme of the day is uncertainty.
Still, the world machine grinds on. As with any set of challenges, fear and doubt can be broken into parts and examined and responded to separately. You have your health concerns, as well as those of your friends, family members, neighbors, and coworkers. Then, you have your overall well-being, including food and shelter. Somewhere a bit further in the list comes your job and the projects you are trying your best to finish up and get built. I can’t advise on the former set, but I can on the last one.
I’m in the business of helping people get their boards built, and I’ve been doing it long enough to have been through recessions, wars, and natural disasters. The wise words of my brother always come to mind: “Do what you did the last time the world came to an end.” With that in mind, here are four things you can do to better ensure that your projects can be built and improve your habits.
1. Minimize Chaos
Remember how I started this column by talking about chaos? That wasn’t hyperbole. Around 70% or more of the file sets we get require some sort of clarification before we proceed to manufacturing. I would assume that what is true for us is true for most manufacturers.
Spend some extra time to ensure that all of those files are accurate and complete. The less time we spend clarifying, the more time we have to process and build.
Double-check your reference designators. It’s pretty common to add or subtract a bypass cap or resistor in the latter stages of design. Some designers also try to resequence the reference designators for clarity. Whether you resequence or not, it’s also pretty easy to end up duplicating a reference designator or causing a mismatch between the BOM and the PCB.
I did that on the last design I sent through our factory. The result was a phone call at the airport from our customer service folks, asking why I had two each of R20 and R21.
Create a checklist early on in the design phase and keep adding to it as you go. Anything that is referenced in more than one file is subject to this type of error. Before hitting “send,” go grab a coffee, donut, or maybe a carrot stick. Then, come back and slowly walk through the checklist.
2. Take Extra Care With All of Your Component Footprints
This is another common way to introduce error and chaos into the process. It’s also another error that I’m pretty familiar with, unfortunately. With so many variations in components and so many new components coming out, it’s just not reasonable to assume that your PCB design CAD software will have all of the footprints you need.
Some companies have dedicated librarians, and their job is to create and or manage all of the company footprints, but few of us in practice have that luxury. Sometimes, that librarian is busy enough that we need to go ahead and make our own footprints or be forced to wait a week.
If you have a big connector, 2.5 mm is not the same as 2.54 mm or 0.1 in. We see this way too often. For a 2 x 6 pin connector, it is usually close enough, but beyond that, through-hole connectors don’t fit, and surface-mount connectors risk bridging.
For super small parts, all of the layers in the footprint are critical. It’s common to let your CAD footprint editor just duplicate the copper layer for the solder paste layer. Don’t do this. Go to the component datasheet and use the exact dimensions and position specified for the paste layer. You may need to get out your calculator because of the way they often specify dimensions.
The copper layer is also critical with small parts. Some people will duplicate the pad on the bottom of the component. Again, that will likely not allow for proper paste spread. Take a look at my previous column titled “Powerful Prototypes: An Open-source Adventure” to see an example of what can happen when the copper pad is the wrong size.
3. Do Not Assume: Communicate and Eliminate Ambiguity
This one seems a little pedantic, but it is really important and is a cause of many issues. As a designer, you have all of the details of your design in your head (“your” is the watchword here). You know all of the subtleties, nuances, and details of your design. Even things that seem obvious to you are not obvious to others.
A good example would be the humble 0.1-uF, 6-volt bypass capacitor. In most cases, any 0.1-uF capacitor of the same package between 6 volts and 50 volts would work fine as a substitute. That may seem obvious. However, while many components land in that “close is close enough” realm, others do not. In a highly tuned RF design, the ESR, ISR, or other ratings may be critical design parameters. A manufacturer has no way of knowing that. Add a couple of alternates to your BOM so that no one in purchasing needs to guess.
Also, be available. We—and many other EMS companies—work 24 hours, 6 or 7 days a week. If we have questions, we may need to contact you at 3:00 a.m. on a Saturday. The sooner we can get an answer, the sooner we can get back to building your boards.
4. Don’t Panic
Always know where your towel is (and your hand sanitizer). Crises come and go. They are not good, nor should they be taken lightly—hence the word “crisis” —but we can come out of them stronger. Any work practices that you improve to get through this period will still apply long after the world is back to normal.
Duane Benson is marketing manager and CTO at Screaming Circuits.
More Columns from Powerful Prototypes
Powerful Prototypes: Small Computer ModulesPowerful Prototypes: A Trip Back to the Basics
Powerful Prototypes: The Work World in 2021
Powerful Prototypes: Why Datasheets Matter
Powerful Prototypes: An Open-Source Adventure
Powerful Prototypes: Five Technological Shifts in the New Decade
Powerful Prototypes: Cost Reduction in Design
Powerful Prototypes: New PCB Fab Technology—What You Need to Know