-
- News
- Books
Featured Books
- smt007 Magazine
Latest Issues
Current IssueSupply Chain Strategies
A successful brand is built on strong customer relationships—anchored by a well-orchestrated supply chain at its core. This month, we look at how managing your supply chain directly influences customer perception.
What's Your Sweet Spot?
Are you in a niche that’s growing or shrinking? Is it time to reassess and refocus? We spotlight companies thriving by redefining or reinforcing their niche. What are their insights?
Moving Forward With Confidence
In this issue, we focus on sales and quoting, workforce training, new IPC leadership in the U.S. and Canada, the effects of tariffs, CFX standards, and much more—all designed to provide perspective as you move through the cloud bank of today's shifting economic market.
- Articles
- Columns
- Links
- Media kit
||| MENU - smt007 Magazine
Estimated reading time: 7 minutes
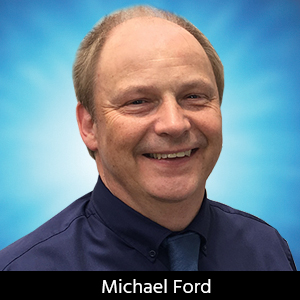
Smart Factory Insights: Size Matters—The Digital Twin
In the electronics manufacturing space, at least, less is more. There are a whole plethora of reasons that have been driving down the size of electronic assemblies for many years—a trend which shows no sign of diminishing. The price we all have to pay as electronics manufacturers is not trivial, as existing paradigms of assembly, inspection, test, and quality control are challenged to the extreme. The digital twin is supposedly the new paradigm, yet—as with many things these days—the term has already been abused by various marketing teams to promote many disparate products and bespoke technologies, causing confusion, which stifles progress. Let’s consider what the true digital twin is really all about—including the components, uses, and benefits—and see that it is not just an excuse to show some cool 3D graphics.
Size Matters
Miniaturization, in one form or another, has led the way competitively between OEMs of key consumer devices—a phenomenon that has now stretched across the whole industry. The trend started back in the 1980s when portable consumer devices first appeared, and rivalries between the giant consumer device manufacturers became public. One great example was the launch in Tokyo by Sharp, who launched their smallest ever mini-disc player to huge media accolades. Attending the event was Sony’s president at the time, Norio Ohga, who—when asked about his reaction to Sharp having the smallest player in the world—took out of his shirt pocket what appeared to be a prototype of a player half the size, and said, “I don’t think so.”
Though with less fanfare, perhaps, the reducing size of electronics has been a continuous pursuit. It is not just a matter of being stylish and easy to carry. Sophisticated electronic controllers are now being integrated and embedded into the majority of everything that we own or use, including phones, energy meters, automotive intelligence, and military and space technology. There are many other factors apart from size itself that are important, including the weight; the space required for storage and transportation related to packaging; the amount of material consumption, especially for key materials for which there is a finite supply; the energy consumption of the device, including the safety of power supplies—especially batteries; and the physical strength of the device in terms of protection for example of an automotive module involved in a collision.
Size matters are clearly not a new challenge, but we do appear to have reached the point of diminishing return where the refinement of existing processes for the manufacturing and assembly of electronics-based devices—as well as integration of electronic assemblies into more mechanical products—when dealing with the practical aspects of size. Rather than further incremental change, the industry needs to take a step forward.
It Starts With Design
In the design world, the issue of reducing the size of designs is really not an issue of their domain. In any design work being performed, the designer can simply zoom in, and everything looks the same as before. The physical world does not allow such luxury, as there are some very specific constraints, which the designer later experiences as they run their design for manufacturing (DFM) tests. Many assumptions and decisions are typically made in the virtual world of design that either need extensive re-evaluation or could be missed, the ramifications of which come to light only during the physical realization of the product. The problems then translate into production issues, where test points cannot be physically accessed, for example, such that assembly confirmation cannot be done completely, representing a risk of defects appearing in the market.
There are so many well-known examples of challenges within manufacturing as the size of products decreases, and hence the density of components increases, including stencil creation, component placement, soldering, as well as test and inspection. Most issues in manufacturing are size-related. Though automation has been developed to follow the trend of miniaturization, unfortunately, with humans, the trend has, if anything, been the reverse. More and more traditional assembly tasks have become impossible to execute through manual assembly, such that they become the target of specialist robotic assembly or require the need for specialist tools and equipment. The effect of all of these challenges is simply an increase in the cost and lead-time for assembly, which is not good news in a highly competitive industry.
Beyond manufacturing, the reliability of products in the market is also affected, as smaller product sizes make it more difficult to dissipate heat effectively, for instance. The smaller sizes of components also means less tolerance to unusual conditions, such as overvoltage. Life expectancy may be limited in many cases.
The Role of the Digital Twin
The development of digital tools for design, together with the subsequent flow of data to manufacturing and the many tools that are then required to execute manufacturing, have been quite removed from the world in which they work, with no concept of evaluating the physical result of what they are doing. This connection is vital. Without it, it is on a par with a media company creating television programs without understanding what audiences like.
The definition of the digital twin goes beyond the simple gathering of data related to product design, manufacturing, and operation. It is the reconciliation of physical and virtual worlds such that the manipulation and use of data are done in the precise context of the physical constraints. This includes not only the product itself, but also all materials, tools, machines, and processes used throughout the life cycle of the product, as well as environmental aspects such as temperatures, pressure, energy supplies, and physical stresses and strains to which the product may be subjected.
The Use of the Digital Twin
The true digital twin, therefore, is inclusive of a vast array and architecture of technologies, all of which are represented through data, available to any application that wishes to be a part of the new paradigm of digital manufacturing. At the highest level, we can see the point at which a corporate business manager will simply select a digital product model on his screen, and then drag and drop it into a digital assembly model of a line or factory. This will automatically determine and show the capability, delivery, timing, and cost of manufacturing with many layers of software (likely from many different vendors)—including IIoT-driven MES and machine vendors—working seamlessly together to model the physical and digital world.
Designers no longer need to depend on static design-rules, but can seamlessly understand the effects of producibility and product reliability as they perform the original design. In manufacturing, rather than the dependence on the physical analysis of the product to determine production configuration parameters, they can be set based on the digital model without a doubt that constraints of the actual equipment, materials, and tools selected have been taken into account. This is just as well, as any form of manual intervention in the equipment programming or engineering processes can no longer be reliably made based on the physical domain alone as product sizes decrease, and component densities increase.
The Realization of the Digital Twin
The practical ways forward towards the real digital twin have already started. The IPC-2581 Digital Product Model (DPMX), for example, is a mature and successful way to model the complete electrical design of a PCB in a single simple file. The JEDEC JEP-30 standard is a new way to model components in three dimensions, including temperature profiles, specifications, and tolerances. The IPC Connected Factory Exchange (CFX) standard promotes open IIoT-driven communication amongst machines and systems, orchestrated by the IIoT-based MES platform—which is essential as the connectivity required for the digital twin to be inclusive of all components—without the need any longer for hundreds of millions of dollars to be spent throughout the industry on bespoke connections.
The true digital twin will encompass all of these existing technologies and expand its purview to include such things as mechanical design, robot simulation, and reliability performance. These elements are not solutions or proprietary, nor do they belong to any one vendor, but they define the environment in which solutions from many different vendors can work together.
What Can I Do?
For the vast majority of people in the industry, it is important to understand the true scope of what is happening and judge solutions as they are marketed based on the knowledge of what has to happen to make the transition from separated physical management and digital management into becoming the true digital twin that combines both. For those adventurous enough to want to contribute to the creation of a digital twin standard or simply understand more about what the true digital twin is about, IPC has just started such an initiative, which will quickly develop into the necessary guidance for what must happen in the industry to make the step-change required in our miniaturizing world.
This column originally appeared in the February 2020 issue of SMT007 Magazine.
More Columns from Smart Factory Insights
Smart Factory Insights: Making Rework a Smart Business OpportunitySmart Factory Insights: The Sustainability Gold Rush
Smart Factory Insights: Today’s Manufacturing Jobs Require a New Skill Set
Smart Factory Insights: Compose Yourself, Mr. Ford
Smart Factory Insights: The Smart Business Case for Local PCB Manufacturing
Smart Factory Insights: Manufacturing Digital Twin—Spanners in the Works
Smart Factory Insights: Machines, People, and AI
Smart Factory Insights: Is Sustainability in Manufacturing a Benefit or Burden?