-
-
News
News Highlights
- Books
Featured Books
- smt007 Magazine
Latest Issues
Current IssueSpotlight on India
We invite you on a virtual tour of India’s thriving ecosystem, guided by the Global Electronics Association’s India office staff, who share their insights into the region’s growth and opportunities.
Supply Chain Strategies
A successful brand is built on strong customer relationships—anchored by a well-orchestrated supply chain at its core. This month, we look at how managing your supply chain directly influences customer perception.
What's Your Sweet Spot?
Are you in a niche that’s growing or shrinking? Is it time to reassess and refocus? We spotlight companies thriving by redefining or reinforcing their niche. What are their insights?
- Articles
- Columns
- Links
- Media kit
||| MENU - smt007 Magazine
Estimated reading time: 4 minutes
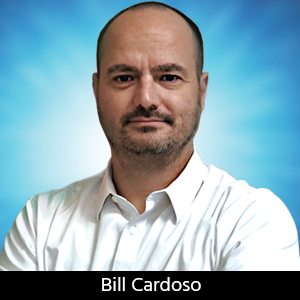
X-Rayted Inspection: Manufacturing in the Eye of a Pandemic
I usually write about X-ray inspection, artificial intelligence, machine learning, and how it all connects to Industry 4.0. This month, however, I’m shifting gears. The impact of the COVID-19 pandemic in our economy greatly disrupted our business. In this column, I’ll share some of the things our company been doing to weather this storm. Hopefully, some of these strategies can be useful to you. As such, please let me know what you have been doing to adapt your business to shelter-in-place policies and to an overall economy that quickly entered a recession. The bottom line is that we won’t stop working hard.
Planning
Our leadership team had been monitoring the situation in Asia—and the consequent disruption to life and manufacturing—since November last year. At that point in time, we knew things could get pretty bad in the U.S. However, we didn’t know when (or if) the coronavirus would land in the U.S. After all, we had weathered ebola, SARS, avian flu, and other outbreaks with little to no impact in our life here in the U.S.
But our motto “plan for the worst and hope for the best” led us to start thinking about the possible scenario of closing down our facility. Because of that, we started looking for smaller facilities near our team’s houses, as we suspected very limited travel ability. Our manufacturing cells, as shown in Figure 1, allow us to build a machine from the ground up in a single location (contrary to a production line, where the machine would move from station to station). We planned on how to move several cells from one large facility to a set of smaller facilities.
Figure 1: One of several manufacturing cells at Creative Electron’s headquarters in San Marcos, California.
Now, the coronavirus had landed in the U.S, but some leaders are still downplaying its impact in the country and calling it a “mild flu.” The gravity of the situation gained clarity when San Francisco issued a shelter-in-place order on March 16, 2020. That’s when our plan to move out of our facility was placed in motion. It was a matter of when, not if, the same shelter-in-place order was to be issued for San Diego.
Executing
On the evening of March 19, Governor Gavin Newsom announced a statewide shelter-in-place policy for California. That triggered the start of our moving plan, and machines in several different stages of completion were moved to eight different facilities around San Diego (Figure 2). At these facilities, smaller teams could continue to work while following the social distancing rules set by California’s policy.
Figure 2: Time to move! All packed to set up the new manufacturing facilities.
During
That’s where we are now. We continue to manufacture X-ray machines (Figure 3). We have lost some efficiency, as we needed to distribute inventory for all eight facilities. Our quality control system was already on the cloud, so it was straightforward to scale and distribute it, and the same was true for the assembly instructions and inventory control.
The main challenge has been communication, as we can no longer walk around the cells and share information (Figure 4). Most of our team would come to one facility every day to work. The idea of working from different places, mostly by ourselves, is a big change for us. We’re still adapting.
Figure 3: One of our eight manufacturing cells in San Diego.
Figure 4: Our weekly (now daily) leadership meeting, which used to happen face to face.
Aftermath
We still don’t know how long it will take until we can reopen our facility in San Marcos. It’s hard to think about an almost 30,000 square foot facility sitting idle as we wait for this virus to run its course. I think a lot about the lessons we are learning now, which we’ll be able to use after these dark clouds clear.
Figure 5: A note found in a manufacturing cell at headquarters that fits the occasion (a quote from Hunter S. Thompson).
I’m sure you’re compiling a list of things that are better (and worse) about your business and your team during this crisis. Some of these things we’ll want to keep; others we will need to change. Here are a few things we are considering.
1. Work From Home
Our software team had been coming to the office every day. Their efficiency has increased during the shutdown period, mostly attributed to the lack of office distractions. That’s a department we can see working from home more often.
2. Distributed Manufacturing Cells
Our whole development and manufacturing team worked under one roof. I didn’t see any other way since this “experiment.” There are some advantages of having somewhat isolated, smaller teams. Some have gained in speed (perhaps because of fewer distractions). A set of eight facilities is too much, but maybe two or three to minimize commutes to a central location might make sense going forward. Some of our assemblers were driving over one hour each way to work. Communication between these cells would definitely be a long-term challenge.
3. Quality Control
We started with a great set of quality control and assembly instructions. If we continue with this structure, how do we ensure the continuation of quality documentation and control? Since we can’t compromise on quality, this will be a critical point of attention to management.
Conclusion
These are challenging times that are stretching the capabilities of every business. The past two weeks have registered over 10 million unemployment claims. There is a lot of fear out there. People are afraid for their health and for their jobs. That hits the base of Maslow’s hierarchy of needs. As business leaders, these fears further complicate how we navigate these turbulent waters. Historia est Magistra Vitae; history is life’s teacher. What lessons are we learning today?
Dr. Bill Cardoso is CEO of Creative Electron.
More Columns from X-Rayted Files
X-Rayted Files: Best Practices in Buying MachinesX-Rayted Files: ’23 and Me?
X-Rayted Files: Battery-Powered Advancements Keep on Ticking
X-Rayted Files: What’s Cooler Than X-ray?
X-Rayted Files: My Favorite BGA Assembly Ever, Part 3
X-Rayted Files: My Favorite BGA Assembly Ever, Part 2
X-Rayted Files: My Favorite BGA Assembly Ever
X-Rayted Files: Smart vs. Intelligent SMT Factory