-
- News
- Books
Featured Books
- design007 Magazine
Latest Issues
Current IssueAll About That Route
Most designers favor manual routing, but today's interactive autorouters may be changing designers' minds by allowing users more direct control. In this issue, our expert contributors discuss a variety of manual and autorouting strategies.
Creating the Ideal Data Package
Why is it so difficult to create the ideal data package? Many of these simple errors can be alleviated by paying attention to detail—and knowing what issues to look out for. So, this month, our experts weigh in on the best practices for creating the ideal design data package for your design.
Designing Through the Noise
Our experts discuss the constantly evolving world of RF design, including the many tradeoffs, material considerations, and design tips and techniques that designers and design engineers need to know to succeed in this high-frequency realm.
- Articles
- Columns
- Links
- Media kit
||| MENU - design007 Magazine
Business Practices Drive the Smart Factory, Not the Other Way Around (Pt. 2)
April 9, 2020 | I-Connect007 Editorial TeamEstimated reading time: 2 minutes
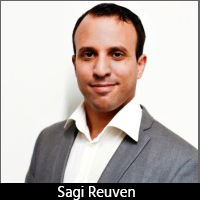
In Part 2 of this conversation, Sagi Reuven— business development manager at Mentor, a Siemens Business—continues his discussion on how smart factory implementations must start with traditional process analysis and improvement before the data capture process is useful. Read Part 1 of this interview in the March 2020 issue of SMT007 Magazine here.
Johnson: Sagi, we started out this conversation with the proposition, “How do you transform your brownfield site—your existing facility— into a smart factory?” So far, we’ve learned that converting to a smart factory is not necessarily about the equipment; it’s centered around business practices, and manufacturers don’t necessarily need to go build a brand-new greenfield facility to implement a smart factory. What you need to do is be “greenfield” about how you think about the operation of your business. We left off with materials as the first place your customers usually start their smart factory transition. If the compelling event to get them off the dime and moving is material handling, where do they tend to go next?
Reuven: Usually, they start with the basics of data acquisition, including IIoT. This will be the first step if they don’t want to do it all at once. They will do basic data acquisition and look into some dashboards and analytics; one example could be around optimizing the changeover. Then, the second step would be advanced material management like ERP visibility, such as just-in-time delivery, including AGVs and material towers. If the material is about to be fully consumed on the machine, it will send a notification to the storage tower or the operator in the storage that you need to put a new reel in the machine so that it will keep on working. Again, when you look at the numbers, it saves 3–4 minutes, but I want to go back to the numbers.
The margins in electronics are very small. You have a 7–8% margin because the material is super expensive. If you save three minutes on one machine, there are three machines per line, and the line is working 20 hours for six days a week, you can multiply the three minutes that the machine stops because you need to bring a new reel and change it since it didn’t bring it on time. When you’re thinking about it from the basic level, you would say, “I don’t need to invest $100,000 in a software piece that will save me three minutes.” However, there is no problem here.
Johnson: That three minutes of time, accumulated, can double your margin.
Reuven: Exactly. You should not think, “I don’t have a real problem because three minutes is not a big deal. I will get the reel and replace it. No problem. It’s fine.”
To read the rest of this interview, which appeared in the April 2020 issue of SMT007 Magazine, click here.
Suggested Items
Specially Developed for Laser Plastic Welding from LPKF
06/25/2025 | LPKFLPKF introduces TherMoPro, a thermographic analysis system specifically developed for laser plastic welding that transforms thermal data into concrete actionable insights. Through automated capture, evaluation, and interpretation of surface temperature patterns immediately after welding, the system provides unprecedented process transparency that correlates with product joining quality and long-term product stability.
Smart Automation: The Power of Data Integration in Electronics Manufacturing
06/24/2025 | Josh Casper -- Column: Smart AutomationAs EMS companies adopt automation, machine data collection and integration are among the biggest challenges. It’s now commonplace for equipment to collect and output vast amounts of data, sometimes more than a manufacturer knows what to do with. While many OEM equipment vendors offer full-line solutions, most EMS companies still take a vendor-agnostic approach, selecting the equipment companies that best serve their needs rather than a single-vendor solution.
Keysight, NTT, and NTT Innovative Devices Achieve 280 Gbps World Record Data Rate with Sub-Terahertz for 6G
06/17/2025 | Keysight TechnologiesKeysight Technologies, Inc. in collaboration with NTT Corporation and NTT Innovative Devices Corporation (NTT Innovative Devices), today announced a groundbreaking world record in data rate achieved using sub-THz frequencies.
Priority Software Announces the New, Game-Changing aiERP
06/12/2025 | Priority SoftwarePriority Software Ltd., a leading global provider of ERP and business management software announces its revolutionary aiERP, leveraging the power of AI to transform business operations.
Breaking Silos with Intelligence: Connectivity of Component-level Data Across the SMT Line
06/09/2025 | Dr. Eyal Weiss, CybordAs the complexity and demands of electronics manufacturing continue to rise, the smart factory is no longer a distant vision; it has become a necessity. While machine connectivity and line-level data integration have gained traction in recent years, one of the most overlooked opportunities lies in the component itself. Specifically, in the data captured just milliseconds before a component is placed onto the PCB, which often goes unexamined and is permanently lost once reflow begins.