-
- News
- Books
Featured Books
- design007 Magazine
Latest Issues
Current IssueAll About That Route
Most designers favor manual routing, but today's interactive autorouters may be changing designers' minds by allowing users more direct control. In this issue, our expert contributors discuss a variety of manual and autorouting strategies.
Creating the Ideal Data Package
Why is it so difficult to create the ideal data package? Many of these simple errors can be alleviated by paying attention to detail—and knowing what issues to look out for. So, this month, our experts weigh in on the best practices for creating the ideal design data package for your design.
Designing Through the Noise
Our experts discuss the constantly evolving world of RF design, including the many tradeoffs, material considerations, and design tips and techniques that designers and design engineers need to know to succeed in this high-frequency realm.
- Articles
- Columns
- Links
- Media kit
||| MENU - design007 Magazine
iNEMI’s PCB Roadmap Explained
May 1, 2020 | Pete Starkey, I-Connect007Estimated reading time: 7 minutes
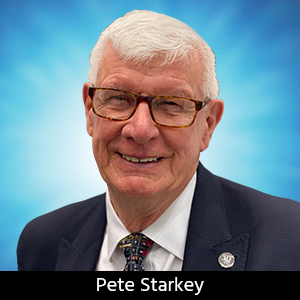
In an informative and enlightening webinar, iNEMI Project Manager Steve Payne was joined by Isola Group CTO Ed Kelley to explain, review, and discuss the details of the recently published “iNEMI 2019 Roadmap for Organic PCBs.”
Payne summarised the structure and objectives of iNEMI, the International Electronics Manufacturing Initiative—an industry-led, not-for-profit, R&D consortium of approximately 80 leading electronics manufacturers, suppliers, associations, government agencies, and universities with its organic PCB chapter addressing the technology needs for all forms of PCBs and flexible circuits. The iNEMI roadmap was a global collaborative effort representing many perspectives from the electronics manufacturing supply chain, defining the state-of-the-art in the electronics industry, identifying technology and infrastructure gaps, and setting industry R&D priorities with a 10-year outlook.
Referring to a schematic combination of product needs and technology evolution plotted on the same timescale, Payne indicated the area where a gap existed between the two curves, and it was this gap that represented the area of opportunity for iNEMI collaborative projects, along with long-term research and internal R&D. The roadmap gave direction as to which way the industry needed to go, with product needs mapped to technology needs and capabilities. And clearly, it was necessary to consider environment, climate change, end-of-life, reuse, and recycling as additional drivers.
Payne welcomed Ed Kelley to provide an insight from the perspective of a PCB materials manufacturer and to describe some key market drivers. His list included 5G infrastructure and handsets; increasing the use of personal devices, electrification of vehicles, and advanced driver assistance systems; the move toward autonomous vehicles, smart factory and smart home infrastructure, and the internet of things; and semiconductor packaging and substrate technologies. Factors—such as the widespread impact of 5G, miniaturisation, increasing density of semiconductor packaging, higher frequency operation, durability and thermal reliability, reduced circuit geometries, and greater density requirements—demanded advances in PCB technology. These included new manufacturing methods, such as modified semi-additive processing (mSAP) and improved base materials, rigid and flexible, with greater emphasis on electrical performance. And the expectation of cost reduction was universal.
Kelley gave a series of specific examples and indicated where these issues were initiating iNEMI projects and materials developments: A 26% compound annual growth rate in bandwidth demand was forecast as a consequence of the increase in the number of devices and connections and the volume of data associated with 5G. Increased PCB routing density and higher-frequency operation would lead to greater heat generation and more-demanding reliability requirements. PCB warpage would become an increasingly critical consideration with the growing use of organic semiconductor packages, especially with thinner substrates and hybrid builds. Effective thermal management solutions would become vitally important with miniaturisation combined with high voltage and high current operation and the increasing use of embedded components. Additionally, the root causes of failure mechanisms such as pad cratering, delamination, via breakdown, and conductive anodic filament (CAF) formation required exhaustive study.
Payne then commented on the enormous scope for the utilisation of embedded components: passives, actives, and combinations of both, with some illustrations of practical examples and challenges. The message from the roadmap was of a steady and continuing adoption. “What’s going on in the PCB industry?” was Payne’s question as he handed back to Kelley for a situational analysis of what had come out of the roadmap.
Regarding rigid PCBs and laminate materials, Kelley summarised the trend for increasing demands for electrical performance, with hybrid stack-ups, reducing conductor width and pitch, reducing via hole geometries, increasing blind via aspect ratios, increasing thermal reliability requirements, smoothness of copper conductors, multiple sequential lamination, and semi-additive build-up technology. The response had been the development of laminates with extreme low-loss resin systems, low Dk and Df glass fabrics, and very-low-profile and no-profile copper foils, with improved thermal reliability and CAF resistance. Kelly illustrated some of the new developments with comparative graphs of electrical performance. More innovative solutions had been the use of non-woven glass reinforcement and, in some cases, non-reinforced resin films. Heavy copper and embedded coin applications demanded high-flow resin characteristics, and there was a continuing trend toward halogen-free flame retardants.
Payne gave a situational analysis of flexible circuits, discussing the increasing demand for portability of devices. He discussed wearable and stretchable circuits and flexible circuits in high-frequency applications. There was an increasing use of thin copper, thin dielectric, and adhesive-less materials. He commented on the high cost of high-performance flexible materials.
Payne briefly mentioned electro-optical PCBs, which were also covered in iNEMI’s organic PCB chapter, remarking upon the continuing technical challenges in embedding effective optical interconnects within a PCB structure and discussing ongoing developments with fibre-optic flex planes, polymer waveguides and planar glass waveguides.
A fundamental outcome of the roadmap was to predict future technology over the next 10 years. Kelley and Payne looked at a selection of the technology gaps and challenges.
Kelley summarised those identified for rigid PCBs and laminates, beginning with a study of the effect of copper bonding treatments on signal losses in high-frequency circuits. It was found that the 10% improvement in a loss at 28GHz achieved using one-micron instead of two-micron very-low-profile foil, and ultra-low-loss resin was significantly reduced if the copper was treated with an oxide-alternative bonding treatment. A related project was studying the effect of copper profile on its adhesion to resin. Skew could be an issue on differential pairs at high data rates because of fibre-weave effects in glass fabric reinforcement, and improved materials had been developed to mitigate the effect. Methods for reliability testing of hybrid PCB constructions were being investigated. Techniques were being developed to mitigate field failures from pad cratering. Further advances were being made in embedding technology for active and passive components. Improved Z-axis interconnection methods continued to be investigated for build-up technologies, as well as alternatives to back-drilling for stub-reduction in through-vias.
The requirement for CAF-resistant laminates continued to increase as circuit features became smaller and denser, and Kelley showed examples of routes through which CAF could propagate. Extremely low-loss resin systems were driving the development of coupling agents for resin-to-glass wetting and bonding. And improvements in process engineering were enabling the manufacture of more robust laminate materials. New failure modes were becoming apparent, associated with higher-voltage applications in electric vehicle applications.
Payne summarised technology gaps and challenges for flexible materials and PCBs. There was a need for materials capable of higher data-processing speed, with thinner dielectric layers and high breakdown voltage. Dimensional stability with changes in temperature and humidity remained a challenge. Materials were required with durability and improved thermal characteristics, capable of carrying a higher density of fine-line conductors, as well as an ongoing need for low-cost, process-friendly substrates. And development continued on stretchable circuits and textile circuitry.
Payne briefly mentioned semiconductor packaging, commenting that although this was currently outside the remit of the iNEMI PCB chapter, the future trend would be toward organic-laminate-based packaging technology.
A great deal work had already been done on electro-optical PCBs, but there were still significant challenges, and more work was needed on topics, such as polymer wave-guides, fibre-optic flex planes, and planar glass waveguides.
Summarising the business trends that had come out of the roadmap, the overcapacity for rigid PCBs and the continuing consolidation of PCB fabricators were well known. There was an increasing demand for flexible circuits. There had been issues with critical materials, as well as important environmental and end-of-life issues. And the drive towards smart manufacturing had prompted a new iNEMI initiative on multi-directional physical and information flow.
The technical trend was to very-high-density interconnects through semi-additive processing, together with a convergence of packaging and board-level technologies, as well as embedding passives and actives and the integration of optical with electrical PCB-level interconnects.
Payne and Kelley reviewed several topics derived from the roadmap, which could form proposals and result in iNEMI projects. The first was on material challenges for 5G to provide guidelines for materials characterisation at millimetre-wave frequencies, which had already progressed to an active project. Other topics included the effect of copper surface treatment on signal integrity, mitigation of field failures through pad cratering, assembly-level reliability testing for multilayer builds incorporating dissimilar materials, alternatives to back-drilling, and PCB-level interconnect for co-packaged optics. In each case, the motivation, objective, and strategy were suggested, together with longer-term aims such as producing guideline publications, reporting to standards bodies, or reporting to the industry on manufacturing and cost issues.
Steve Payne and Ed Kelley delivered a clear and comprehensive explanation of the ways in which iNEMI roadmaps identify future opportunities and challenges for the electronics manufacturing industry, helping OEMs, EMS providers, and suppliers to prioritise investments in R&D and technology deployment, influencing the focus of university-based research and providing guidance for government investment in emerging technologies.
An hour well-spent. Many thanks!
Related content: 2019 iNemi Roadmap Overview
Suggested Items
Trouble in Your Tank: Can You Drill the Perfect Hole?
07/07/2025 | Michael Carano -- Column: Trouble in Your TankIn the movie “Friday Night Lights,” the head football coach (played by Billy Bob Thornton) addresses his high school football team on a hot day in August in West Texas. He asks his players one question: “Can you be perfect?” That is an interesting question, in football and the printed circuit board fabrication world, where being perfect is somewhat elusive. When it comes to mechanical drilling and via formation, can you drill the perfect hole time after time?
The Evolution of Picosecond Laser Drilling
06/19/2025 | Marcy LaRont, PCB007 MagazineIs it hard to imagine a single laser pulse reduced not only from nanoseconds to picoseconds in its pulse duration, but even to femtoseconds? Well, buckle up because it seems we are there. In this interview, Dr. Stefan Rung, technical director of laser machines at Schmoll Maschinen GmbH, traces the technology trajectory of the laser drill from the CO2 laser to cutting-edge picosecond and hybrid laser drilling systems, highlighting the benefits and limitations of each method, and demonstrating how laser innovations are shaping the future of PCB fabrication.
Day 2: More Cutting-edge Insights at the EIPC Summer Conference
06/18/2025 | Pete Starkey, I-Connect007The European Institute for the PCB Community (EIPC) summer conference took place this year in Edinburgh, Scotland, June 3-4. This is the third of three articles on the conference. The other two cover Day 1’s sessions and the opening keynote speech. Below is a recap of the second day’s sessions.
Day 1: Cutting Edge Insights at the EIPC Summer Conference
06/17/2025 | Pete Starkey, I-Connect007The European Institute for the PCB Community (EIPC) Summer Conference took place this year in Edinburgh, Scotland, June 3-4. This is the second of three articles on the conference. The other two cover the keynote speeches and Day 2 of the technical conference. Below is a recap of the first day’s sessions.
Preventing Surface Prep Defects and Ensuring Reliability
06/10/2025 | Marcy LaRont, PCB007 MagazineIn printed circuit board (PCB) fabrication, surface preparation is a critical process that ensures strong adhesion, reliable plating, and long-term product performance. Without proper surface treatment, manufacturers may encounter defects such as delamination, poor solder mask adhesion, and plating failures. This article examines key surface preparation techniques, common defects resulting from improper processes, and real-world case studies that illustrate best practices.