-
- News
- Books
Featured Books
- design007 Magazine
Latest Issues
Current IssueProper Floor Planning
Floor planning decisions can make or break performance, manufacturability, and timelines. This month’s contributors weigh in with their best practices for proper floor planning and specific strategies to get it right.
Showing Some Constraint
A strong design constraint strategy carefully balances a wide range of electrical and manufacturing trade-offs. This month, we explore the key requirements, common challenges, and best practices behind building an effective constraint strategy.
All About That Route
Most designers favor manual routing, but today's interactive autorouters may be changing designers' minds by allowing users more direct control. In this issue, our expert contributors discuss a variety of manual and autorouting strategies.
- Articles
- Columns
- Links
- Media kit
||| MENU - design007 Magazine
Estimated reading time: 4 minutes
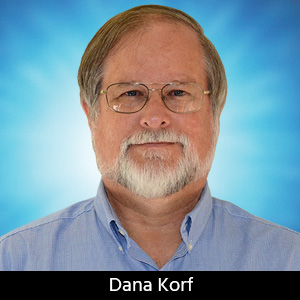
Dana on Data: The Importance of PCB Technology Roadmaps
Peter Drucker once said, “Trying to predict the future is like trying to drive down a country road at night with no lights while looking out the back window.” With that in mind, it is critical that PCB fabricator technology roadmaps and capacity planning align with their customers’ product development and volume requirements to ensure that optimum cost, reliability and performance goals are achieved.
Developing, procuring and installing new fabrication capability is expensive. PCB manufacturers generally have a low profit margin and must optimize their human and capital resources to remain in business. This emphasizes the need to synchronize the customer technology roadmap with the manufacturing roadmap.
I have been fortunate to participate in many plant visits where we have shared our manufacturing technology roadmap as part of a business and capability presentation.
Most customers ask to view a five-year roadmap. These are generally accurate for the first two years because the pre-engineering evaluation has been completed and the capital equipment is in place or on order. The following three years of the roadmap, however, are based on the best intelligence available from our customers. It is difficult to lock down requirements that far out because markets and product design requirements change at a faster rate than five-year cycles.
Very few fabricators have dedicated both financial and engineering resources to support a true research department that can develop new technologies for use in three or more years. They rely on implementing new technologies developed by suppliers and partners.
Customer PCB technology roadmaps generally fall into three categories. The first defines their firmly-established future fabrication design rule requirements. The second presents the product characteristics—size, weight, cost and performance requirements—without specific PCB technology requirements. The third roadmap does not have any long-term requirements and is used in surveying potential suppliers to determine their capabilities. I’ll explain further.
The first roadmap already has determined the routing strategies and required technology requirements to support the boards. It is focused on ensuring that the existing, or new, supply chain can support it. If there is a capability disconnect the fabricator can use that information to enhance capability to match the gap within the required time.
The second product roadmap provides an excellent basis for a very interactive discussion. This provides the fabricator a good opportunity to present current capability, and future thinking or plans. This usually is the longest part of the process, as the designer and fabrication engineering teams discuss various cost/performance options to determine or propose cost effective, lower risk solutions.
Many fabricators have experienced application engineers who reside in various regions and can provide onsite visits to discuss possible approaches and trade-offs with a larger design and manufacturing team before the technology decisions are locked in and can’t be optimized easily.
The most common roadmap and capability discussions revolve around material selection, signal integrity and routing strategies. This is where more than 80% of the product cost is established for a given PCB form factor.
Every year, new materials are being developed and introduced, and are tailored to electrical and thermal performance, mechanical strength and cost. It typically takes years for a revolutionary new material to get developed, UL approved, and quality fabrication processes established.
In the last 20 years, the industry has made extensive progress in combining different materials with specific properties to create a mixed-composite PCB stackup. Low-loss signal integrity requirements can be achieved with low-loss dielectrics, low-loss copper foils and low-loss processes. Product requirements greatly influence which materials will require engineering to develop high yield/reliable processes. After approval, these will be added to the inventory.
There is a wide selection of routing technologies available. These incorporate combinations of line width/space via interconnection technologies. Not all combinations yield reliable interconnection for life or mission critical applications. Short lifetime, more benign environmental condition products can use more aggressive technologies. Not all combinations of these approaches can be used together. For instance, a blind microvia cannot be formed when the PCB layer-layer thickness is five times the via diameter. Each fabricator has tailored capability and a roadmap to match an existing customer’s requirements.
The PCB technologies and strategies that are selected may require that multiple fabricators, or fabrication facilities within the same corporate structure, offer the required capability to reduce the procurement risk. These may have requirements for availability in multiple countries to reduce the risks related to environmental and political factors.
What will most influence the path a manufacturer takes in researching, producing and installing new capability? I believe it’s both the physical and performance requirements—now and in the future. This is more reliable than trying to estimate what products some companies will want. It’s critical to openly discuss product technology if we want to achieve the goal of reliable, cost-effective products.
Present your thinking, even if it’s an educated guess. As Peter Drucker also said, “The best way to predict the future is to create it.”
Dana Korf is the principal consultant at Korf Consultancy LLC.
More Columns from Dana on Data
Dana on Data: Best Practices in Interpreting Drawing Notes—‘Use Latest Revision’Dana on Data: The Missing AI-NPI Link
Dana on Data: Merging 2D Electrical, 3D Mechanical Worlds
Dana on Data: Resurrecting IPC Class 1
Dana on Data: The Evolution of Fabrication Drawing
Dana on Data: The Insane PCB DFM Process
Dana on Data: eCAD PCB Design Deficiencies
Dana on Data: Nuke the Netlist