-
- News
- Books
Featured Books
- design007 Magazine
Latest Issues
Current IssueProper Floor Planning
Floor planning decisions can make or break performance, manufacturability, and timelines. This month’s contributors weigh in with their best practices for proper floor planning and specific strategies to get it right.
Showing Some Constraint
A strong design constraint strategy carefully balances a wide range of electrical and manufacturing trade-offs. This month, we explore the key requirements, common challenges, and best practices behind building an effective constraint strategy.
All About That Route
Most designers favor manual routing, but today's interactive autorouters may be changing designers' minds by allowing users more direct control. In this issue, our expert contributors discuss a variety of manual and autorouting strategies.
- Articles
- Columns
- Links
- Media kit
||| MENU - design007 Magazine
Estimated reading time: 6 minutes
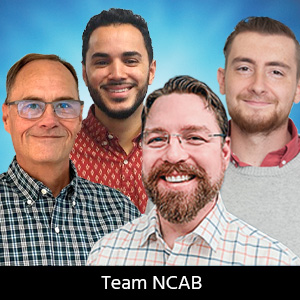
Fresh PCB Concepts: 7 Options for Via Treatment
Many times, I come across a PCB design with via holes that are completely exposed. In some cases, this is acceptable. But there are many other times when I recommend that the hole either be covered and/or tented. But in most cases, I recommend they be plugged.
For example, here are several advantages of via hole plugging:
- Prevents residues becoming trapped in the holes, preventing corrosion
- Prevents air leakage during ICT
- Prevents solder balling
- Prevents solder paste loss (solder migration)
- Prevents contamination entrapment under components
- Prevents migration of adhesives and conformal coatings used during assembly
But before getting into options for via treatment, I want to talk about the term “tenting.” This term is a bit antiquated and refers to dry film solder mask that has fallen to the current liquid photoimagable (LPI) solder mask. In days past, the dry film would cover over the hole without opening and form a “tent.” With LPI mask, the effect is essentially lost, and the liquid will fall into the barrel of the hole. Some of the intended effects remain, but the overall encapsulation is not quite the same.
Now, let’s consider IPC-4761 (design guide for protection of printed board via structures). There are seven different via hole protection types in IPC-4761 (classified as Types I–VII). Some of these types are recommended while others are not, and others are necessary for certain technologies.
Type I: Tented Via Holes
Type I is split into two categories: Type Ia (single-sided) and Type Ib (both sides). Single-sided is not recommended by IPC. In Type I, there is no solder mask opening over the via hole, so it will not be developed away. The aim is to apply solder mask over the via hole, effectively tenting it. However, there is a risk with this option. The tent can break down on one or both sides, leading to entrapment of chemistry or even solder. I personally do not recommend Type I for immersion tin finish due to the risks of solution entrapment and risk of copper corrosion.
Type II: Tented and Covered Via Holes
This type of via plugging is also split into two categories: Type IIa (single-sided) and Type IIb (both sides). Type II is very similar to Type I with a secondary covering of mask applied over the via hole. Again the single-sided version (Type IIa) is not recommended. Even with the secondary coat, similar concerns apply when compared to Type I, and with this type, there is a concern of increased processing/mask height over the via hole, thus causing concerns for stencil applications. Again, I do not recommend this type for immersion tin finish for the same reasons, including risks of solution entrapment and risk of copper corrosion. In addition, I do not recommend this type of plug be used within a footprint of a BGA due to the potential for elevation over the pad surface.
Type III: Plugged Via Holes
Again, this via is split into two categories: Type IIIa (single-sided) and Type IIIb (both sides). Single-sided is also not recommended by IPC. With Type III, a material is applied, allowing for partial penetration into the via. This may be applied from one or both sides; however, as this is not filling the hole, there is no guarantee the hole will be “blocked.” As with the previous types I mentioned, this can lead to exposed copper in the holes, and air entrapment can cause blow out of the partially plugged hole. And I do not recommend it for immersion tin finish due to the risks of solution entrapment and risk of copper corrosion.
Type IV: Plugged and Covered Via Holes
Split into two categories—Type IVa (single-sided) and Type IVb (both sides)—this method is the same as Type III with additional mask applied over the top. Single-sided is, again, not recommended by IPC. The same concerns apply as with the previous types I described, as well as I do not recommend this for immersion tin finish due to the risks of solution entrapment and risk of copper corrosion (Figure 1).
Figure 1: An example showing the potential result of single-sided plug/single-sided tent (Type I–Type IV) with immersion tin surface finish, where the chemistry becomes entrapped and corrodes the copper within the hole. This can be resolved through moving to either type VI via plugging (preventing chemical entrapment) or leaving the hole open (allowing for adequate rinsing/solution flow).
Type V: Filled Via Holes
This is a via hole with material applied into the via, targeting a full penetration of the via hole with full encapsulation. This provides a complete fill of non-conductive (or conductive) material that will eliminate contaminants remaining in the hole.
Type VI: Filled and Covered Via Holes
This is the same as a Type V via hole (full penetration of material into the hole) with an additional covering of solder mask applied over the via hole and pad (Figures 2 and 3). The solder mask may be applied to one or both sides, depending on design needs. When both pads are covered, this offers superior protection of the full hole/pad. Again, with this approach, there is a complete fill within and over the via hole that, therefore, eliminates the concerns previously mentioned (contaminants, chemical residue entrapment, risk of blow out, eliminate paste loss, etc.).
Figure 2: The target is to achieve a complete fill; however, knowing production and process tolerances, we accept a minimum of 70% fill. To achieve the desired results of preventing any residues or chemicals in the hole, we always recommend filling to at least 70%.
Figure 3: With Type VI via hole plugging, we fill the hole from one side to the other, using a stencil and a screen printing process, before we apply solder mask to the surface of the panel.
Type VII: Filled and Capped Via Holes
This is the same as a Type VI via hole with a secondary metalized coating (copper) applied over the top of the via hole on both sides. This is normally used for such applications as via in pad or in BGA applications where high-density features are required. In this case, it is typical that a special resin is used to plug the via to minimize the risk of air bubbles or voids and also prevent expansion due to thermal excursions. Highly specialized equipment is also required to ensure the resin is adequately drawn into the via and eliminate voiding. While many fabricators say they can do this type of via treatment, we have seen that without the specialized equipment to support, quality becomes sacrificed (Figure 4).
Figure 4: A physical board example of a Type VII filled and capped via hole normally used for such applications as via in pad or in BGA applications where high-density features are required.
My Recommendations
I recommend you consult with your PCB supplier with all your PCB designs, particularly when the design is more complex. With many options for treating the vias, it is important to have an open discussion with your fabricator. Clearly explaining why you need a via treatment and what factors are and are not desirable will ensure the best option is used and that it is compatible with other factors in your design.
Jeff Beauchamp is a field application engineer at NCAB Group.
More Columns from Fresh PCB Concepts
Fresh PCB Concepts: Designing for Success at the Rigid-flex Transition AreaFresh PCB Concepts: More Than Compliance—A Human-centered Sustainability Approach
Fresh PCB Concepts: Assembly Challenges with Micro Components and Standard Solder Mask Practices
Fresh PCB Concepts: The Power of a Lunch & Learn for PCB Professionals
Fresh PCB Concepts: Key Considerations for Reliability, Performance, and Compliance in PCBs
Fresh PCB Concepts: Traceability in PCB Design
Fresh PCB Concepts: Tariffs and the Importance of a Diverse Supply Chain
Fresh PCB Concepts: PCB Stackup Strategies—Minimizing Crosstalk and EMI for Signal Integrity