-
- News
- Books
Featured Books
- smt007 Magazine
Latest Issues
Current IssueSupply Chain Strategies
A successful brand is built on strong customer relationships—anchored by a well-orchestrated supply chain at its core. This month, we look at how managing your supply chain directly influences customer perception.
What's Your Sweet Spot?
Are you in a niche that’s growing or shrinking? Is it time to reassess and refocus? We spotlight companies thriving by redefining or reinforcing their niche. What are their insights?
Moving Forward With Confidence
In this issue, we focus on sales and quoting, workforce training, new IPC leadership in the U.S. and Canada, the effects of tariffs, CFX standards, and much more—all designed to provide perspective as you move through the cloud bank of today's shifting economic market.
- Articles
- Columns
- Links
- Media kit
||| MENU - smt007 Magazine
Estimated reading time: 3 minutes
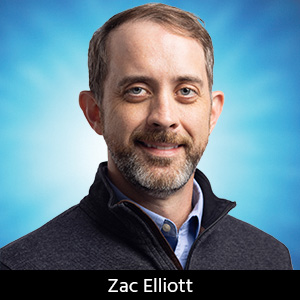
Lean Digital Thread: Driving Productivity Excellence—Lean PCB Manufacturing
I’m in the software business, but I’m used to hearing about supply chain issues from our customers. During the last few months, thanks to COVID-19, I felt the supply chain impact on our hardware production for the first time. I have decided to dedicate this column to effective material management. From my point of view, the new reality brings new challenges—everyone will need to improve productivity (while maintaining a high level of quality, of course) and react faster to changes. We must change our mindset.
Here’s a quote I like from the Zen master of Lean Six Sigma, Taiichi Ohno (Ohno-San is considered to be the father of the first Lean manufacturing system he designed for Toyota): “The Toyota style is not to create results by working hard. It is a system that says there is no limit to people’s creativity. People don't go to Toyota to ‘work’ they go there to ‘think.’”
If you follow the financial reports in electronics manufacturing, you know that the average cost of materials can easily represent around 90% of the cost of the product. In addition, we can all agree that during the last decade, the number of products manufactured and their complexity is skyrocketing. If you pour into this mix the demand to lower the cost and shorten the time-to-market, the only way to thrive is to master how to get the most out of your resources.
“Efficiency is doing things right; effectiveness is doing the right things,” stated Peter Drucker, who was a “business thinker.” His career took off when he was hired to “think” by General Motors.
The most important costs that can be controlled are the investment cost of excess inventory: the cost of space needed to store the materials, logistics operations required to manage the materials, and of course, material that creates bottlenecks in production (Figure 1).
Figure 1: Automated guided vehicles (AGVs) can improve production efficiency, but one has to simulate and plan in advance. This factory decided to use AGVs to move bare boards and semi-finished boards and separate the lines into work cells (and not for moving components into the line).
The motivation to improve material management has resulted in materials management systems that are more of a warehouse system. There is no single responsibility to manage all materials in the supply chain across the whole operation. ERP systems are usually not focused on material tracking once they moved to the production area. And, as mentioned earlier, COVID-19 will make it more difficult to plan.
One of the pillars of Industry 4.0 is agility and planning in particular. Most of the data already exist in various locations (ERP, MES, machines, towers, manufacturing intelligence, and smart shelves). On the production floor, you can find family setups, feeders, trolleys, and moisture-sensitive materials—all the information should be visible to the maximum possible to allow the production managers to make smarter decisions and improve. The inventory should now be more accurate than ever (Figure 2).
Figure 2: Material data flow, such as consumption or pick-up error cost, provides better insights for planning.
Counterfeit Material Traceability
Manufacturers are fully aware that there’s a lot of counterfeit material; however, I’m not sure they are aware that it comprises around 10% of the components they are using, even when provided by the official vendor.
This may cause statistical failures later on in the product life cycle that is signed-off as “the cost of doing business.” In addition to the profit motive, components are often counterfeited to infiltrate malicious code into systems. Until now, checking every single component in an efficient manner has been an impossible mission. Checking the reel label almost never leads to discoveries of counterfeiting or of deficiencies that render the components unfit for assembly. Needless to say, in some cases, there will be return merchandise authorization (RMA) consequences as well.
There are now solutions that allow you to scan each component during assembly and ensure that only authentic, fresh, and untampered components get into your product. Such solutions use AI-based image processing (leveraging data that is already collected by the machines) and provide a report that can impact quality, conformance, and procurement decisions (Figure 3).
Figure 3: The data flow and process of counterfeit traceability.
Conclusion
To summarize, it seems like we are facing a new reality across industries and supply chains. We now need to focus on being prepared for changes—and that can be achieved by gaining more control over the production details.
Sagi Reuven is a business development manager for the electronics industry, Siemens Digital Industries. Download your free copy of the book The Printed Circuit Assembler's Guide to… Advanced Manufacturing in the Digital Age from Mentor, a Siemens Business, and visit I-007eBooks.com for other free, educational titles.
More Columns from Lean Digital Thread
Lean Digital Thread: The Manufacturing Metaverse RevisitedLean Digital Thread: The Secure Digital Thread
Lean Digital Thread: The Manufacturing Metaverse
Lean Digital Thread: Closing the Loop on Manufacturing
Lean Digital Thread: Keeping an Eye on Quality
Lean Digital Thread: Streamlining the Internal Supply Chain
Lean Digital Thread: Achieving Supply Chain Resilience
Lean Digital Thread: (Pro)curing the Supply Chain Virus