-
- News
- Books
Featured Books
- pcb007 Magazine
Latest Issues
Current IssueInventing the Future with SEL
Two years after launching its state-of-the-art PCB facility, SEL shares lessons in vision, execution, and innovation, plus insights from industry icons and technology leaders shaping the future of PCB fabrication.
Sales: From Pitch to PO
From the first cold call to finally receiving that first purchase order, the July PCB007 Magazine breaks down some critical parts of the sales stack. To up your sales game, read on!
The Hole Truth: Via Integrity in an HDI World
From the drilled hole to registration across multiple sequential lamination cycles, to the quality of your copper plating, via reliability in an HDI world is becoming an ever-greater challenge. This month we look at “The Hole Truth,” from creating the “perfect” via to how you can assure via quality and reliability, the first time, every time.
- Articles
- Columns
- Links
- Media kit
||| MENU - pcb007 Magazine
Estimated reading time: 6 minutes
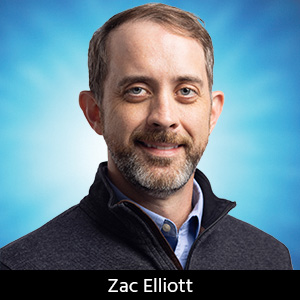
Lean Digital Thread: Closing the Loop on Manufacturing
Throughout this series of articles, we have looked at the benefits of implementing a digital thread for electronics manufacturing. In this edition, I would like to close the loop (pun very much intended) on the lean digital thread and discuss closed-loop manufacturing.
What is Closed-Loop Manufacturing?
In closed-loop manufacturing (CLM) the systems and business processes used to design, plan, manufacture, and use a product are connected, thus enabling continuous improvement and self-organization of production processes. Each step along the value chain constantly feeds data back to the preceding stages so that simulations can be refined, and decisions improved. At the same time, data is automatically pushed forward to the downstream processes, to ensure production plans and manufacturing processes are up to date. This creates a continuous cycle to improve quality, efficiency, and profitability.
The Role of the Digital Twin
Closed-loop manufacturing depends on the ability to share information between different business processes using a digital twin. A digital twin is simply a virtual version of a product that can be used to simulate and test how a device will be built and used in the real world.
There are several digital twins for a given product:
-
Digital twin of the design: The digital twin of the design is all the data that can be used to visualize and simulate the final end-product. This includes the mechanical and electrical designs, schematics, etc.
-
Digital twin of the process: The digital twin of the process defines the manufacturing sequence and steps needed to build the product. This includes the machine technology, recipes, work instructions, and other information needed to simulate and improve the manufacturing flow.
-
Digital twin of production: The digital twin of production includes all the data aggregated during the manufacturing process of a device, including all records of test results, traceability, parametric readings from assembly equipment and the environment, and any exceptions encountered during manufacturing of the device.
Having multiple versions of the digital twin allows specialized software to be used during the various stages of the manufacturing flow. Software that is optimized to design a PCB is not the same software that is optimized to collect the test results from an ICT machine that tests the PCB. Each type of software has completely different inputs and outputs. But they don’t work in isolation. The design information is needed to develop the ICT test protocol and the aggregated test results can be used to improve the product design.
If the different software programs can communicate in a standardized digital twin format, then each can be optimized for its own purpose, and each can improve its results by leveraging information from the other software programs.
The CLM System Golden Triangle
Across the digital enterprise, there are countless software tools to manage the business: desktop productivity suites, business systems, product design tools, partner portals, equipment software, and the list goes on and on. For closed-loop manufacturing, there are three systems that are key to orchestrating the continuous feedback and feedforward loops:
-
ERP: The enterprise resource planning system is responsible for driving the requirements of the business in terms of demand for product and availability of resources. It is responsible for taking the end-customer demand for products and creating the internal production orders needed for manufacturing.
-
PLM: The product lifecycle management system acts as the collaboration platform for design data. It is where the bill of material (BOM) and bill of process (BOP) are created. The BOM and summarized BOP developed in the PLM system become the product master data in the ERP system.
-
MES: The manufacturing execution system controls the product flow and production processes as devices are manufactured on the shop floor. It is responsible for maintaining the “as-built” records for the product. The MES receives detailed BOM, BOP, and product specifications from the PLM system and reports shop floor issues and build records back to the PLM system. From the ERP system, the MES receives production orders and reports back confirmation of operation completion.
Figure 1: The “golden triangle” of closed-loop manufacturing.
Top CLM Use Cases
Having defined the key systems, let’s look at some examples of the most frequent uses cases for closed loop manufacturing.
Design for Manufacturability
Design for manufacturing (DFM) analysis ensures that the product design can be produced using the manufacturing platform available at a given factory. This is typically performed during a new product introduction (NPI) procedure to confirm the capability of the manufacturing equipment at a given site.
During the DFM analysis, the PLM system manages the collaborative BOP development between manufacturing and engineering. The MES provides the factory layout and equipment configuration details using the digital twin of production, while the PLM system communicates with the validation tools using the digital twin of the design. When the DFM analysis is completed successfully, the finalized BOM and BOP master data is released to the ERP and MES using the digital twin of the design and the digital twin of the process.
Using a closed-loop process for DFM analysis allows the procedure to be performed continuously as minor product revisions occur or as manufacturing equipment details change. The PLM backbone controls any product updates and ensures that validated master data is used by the ERP and MES system.
Flexible Manufacturing
Many individual products are part of similar product families that may be produced on the same equipment with the only differences being in the equipment set points or recipes. Closed-loop systems facilitate self-organizing manufacturing by dynamically applying recipes or set points to the equipment as work orders are produced.
This process is orchestrated by the MES system, which is aware of the product specifications that were sent from the PLM system using the digital twin of the process. The MES is then able to manage the recipes on the equipment, matching them with the product defined in the work order coming from the ERP system.
Closed-Loop Quality
Closed-loop quality, which is closely related to closed-loop manufacturing, is where design issues identified on the shop floor are driven back through engineering with a systematic corrective action process. Closed-loop quality depends on the digital thread between PLM, MES, and ERP to ensure that quality issues detected in production are visible to the engineers who can resolve the issue. Likewise, the digital thread is needed to ensure that consistent “as-built” and “as-designed” records are controlled throughout the corrective action process while different versions of a design are actively being produced.
Sharing digital twins provides additional, enhanced capabilities. By correlating CAD design data with measurements taken from production processes, engineering can use the CAD model as a powerful tool for problem-solving and root cause analysis. Conversely, by embedding the 2D and 3D CAD models directly into the MES operator pages, the shop floor is empowered to provide feedback and collaborate directly with engineering.
Closing (the Loop)
If you would like to look further into how closed-loop manufacturing can improve quality, efficiency, and profitability, please reach out to me.
Zac Elliott is technical marketing engineer for Siemens Digital Industries Software.
See this additional content from Siemens Digital Industries Software:?
- The Printed Circuit Designer’s Guide to... Stackups: The Design within the Design by Bill Hargin (a free eBook available for download)
- The Printed Circuit Assembler's Guide to... Smart Data: Using Data to Improve Manufacturing?by Sagi Reuven and Zac Elliott (a free eBook available for download)?
- The Printed Circuit Assembler's Guide to… Advanced Manufacturing in the Digital Age?by Oren Manor (a free eBook available for download)?
- The Printed Circuit Designer’s Guide to… PowerIntegrity by Example by Fadi Deek (a free eBook available for download)
- Siemens’ free, 12-part, on-demand webinar series?“Implementing Digital Twin Best Practices?From?Design Through Manufacturing.”?
- RealTime?with...?Siemens and Computrol: Achieving Operational Excellence in Electronics Manufacturing?
- You can also view other titles in our full I-007eBook library here.
More Columns from Lean Digital Thread
Lean Digital Thread: The Manufacturing Metaverse RevisitedLean Digital Thread: The Secure Digital Thread
Lean Digital Thread: The Manufacturing Metaverse
Lean Digital Thread: Keeping an Eye on Quality
Lean Digital Thread: Streamlining the Internal Supply Chain
Lean Digital Thread: Achieving Supply Chain Resilience
Lean Digital Thread: (Pro)curing the Supply Chain Virus
Lean Digital Thread: Why is Everyone Suddenly Interested in Supply Chain?