-
- News
- Books
Featured Books
- pcb007 Magazine
Latest Issues
Current IssueInventing the Future with SEL
Two years after launching its state-of-the-art PCB facility, SEL shares lessons in vision, execution, and innovation, plus insights from industry icons and technology leaders shaping the future of PCB fabrication.
Sales: From Pitch to PO
From the first cold call to finally receiving that first purchase order, the July PCB007 Magazine breaks down some critical parts of the sales stack. To up your sales game, read on!
The Hole Truth: Via Integrity in an HDI World
From the drilled hole to registration across multiple sequential lamination cycles, to the quality of your copper plating, via reliability in an HDI world is becoming an ever-greater challenge. This month we look at “The Hole Truth,” from creating the “perfect” via to how you can assure via quality and reliability, the first time, every time.
- Articles
- Columns
- Links
- Media kit
||| MENU - pcb007 Magazine
Estimated reading time: 5 minutes
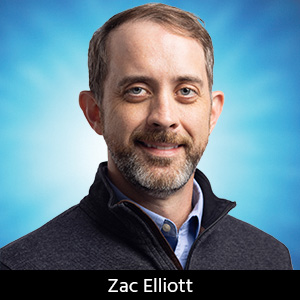
Lean Digital Thread: Keeping an Eye on Quality
So far in this series of articles, we have looked at current trends in the supply chain and the challenges facing manufacturers. In general, the takeaway has been that we must do more with less:
- We need to be more flexible while simultaneously decreasing labor input
- We need to be more efficient while also managing component shortages
But as we strive to manage these challenges, one area where we cannot lose focus or sacrifice is the quality of products being manufactured. This article will look at how current trends impact product quality and new methods to manage the risk.
Challenges to Quality
Several trends contribute to challenges in maintaining product quality.
A higher mix of products: As digitalization, automation, and specialization disrupt consumer and industrial markets, there is an increase in the variety of electronic products being produced today. As the mix of products increases, the production volume of each device or lot of devices decreases. Taken to the extreme, lot sizes have decreased over time from thousands to hundreds to dozens to the now common lot-size-one production orders. With such small lot sizes, there is simply not enough production volume to debug manufacturing process and reach a steady-state quality level.
Increased new product introductions (NPIs): The number of engineering changes, revisions, and new product introductions is increasing across the board. With an explosion in the number of products and the increased product mix mentioned above, it is more difficult to identify trends related to product quality. This is driving manufacturers to focus on process quality as opposed to product quality.
Supply chain disruptions: While still recovering from capacitor shortages a couple of years ago, the silicon supply remains constrained for electronics manufacturers. The industry is planning new foundries to alleviate the lack in supply of IC components, but many manufacturers are stockpiling components to weather the current deficits, often turning to less qualified, second-source vendors for interim supply. Until IC supply catches up with increased demand, manufacturers face an increased risk of counterfeit, recycled, or otherwise inauthentic components.
The AI Solution
Traditional methods of managing these challenges and mitigating the additional risk are not compatible with the industry trends. It isn’t possible to add a new team to support new product introductions, buy a new line to handle the increased product mix, or even inspect every component or material used in the factory. Remember, the trend is to move toward more flexibility and more output from the same (or even fewer) resources.
This presents the perfect opportunity for technology to contribute to improvement and decrease risk for manufacturers. Artificial Intelligence (AI) and Machine Learning (ML), in particular, offer the ability to leverage the complex digital twins of the product, the factory, and the production processes to make improvements and aid in decision making on the production line.
Working with AI presents its own set of challenges. It is a very innovative domain that requires specialized knowledge of the technology and the mathematical models used in the decision-making process. Beyond the technical challenges, a successful AI system requires deep knowledge of the manufacturing domain to provide a solution that can actually improve the process. However, when it’s done right, AI can provide enormous quality control advantages to manufacturers.
To better understand how this works, let’s look at some interesting and novel uses of artificial intelligence in the manufacturing environment.
Inspection False Call Reduction
Walk down almost any SMT line and near the end you will find an operator dutifully reviewing the results of the AOI inspection process. Specifically, the operator is reviewing the products that have failed the AOI process to see whether any of the suspected defects are actually acceptable units. In the best-case scenario, you might even find the AOI engineer tuning the machine to reduce the incidence of false calls or false-negative results. Tuning the machine for optimal performance is a topic for a different article, but what can be done today to make the AOI operator more efficient in his/her tasks?
By combining the historical results from the AOI together with the historical decisions made by an operator, an AI model can be created to predict the likelihood of a given failure being a true failure or a false alarm. When a failure is presented to an operator, the AI solution displays the likelihood that the product is actually defective, providing a much quicker way of dispositioning the board. The operator is free to focus on other tasks, and the line can run more efficiently.
100% Component Inspection
With supply chain issues forcing manufacturers to use second- or third-tier suppliers for components, there is an additional risk of inauthentic materials being assembled on the line. These could be aged components, mixed lots, counterfeit or recycled items, or even components that have been tampered with. Current methods of mitigating these risks rely on destructive samples of components or partial inspection of the top of the component. These methods leave gaps for bad components to enter the supply, become assembled to products, and then be shipped out to the field. Many manufacturers wonder, “Is there an efficient way to inspect 100% of components to prevent bad components from being used on the assembly line?”
There are several points in the typical PCB assembly process where images are taken of the product and the components that can be used to identify faulty components. For example, the SMT machine takes a picture of the bottom of every component to use when aligning the component before placement. The AOI process takes a very detailed image of the board and the top of components after assembly. With AI, these images can be used to identify the source of the component and flag any components that are damaged.
Especially in the SMT process, the decision to assemble or discard the component can be made during the assembly cycle to prevent assembling any bad components. As an extra benefit, the traceability for the board is based on actual evidence of the component on the board and does not rely on operators labeling and scanning materials properly.
With this capability, each component placed on the board can be inspected without any additional labor or loss of efficiency on the line.
Conclusion
With current trends driving the industry to do more with less, artificial intelligence technologies offer the ability to improve performance and reduce risk without sacrificing quality.
Zac Elliott is technical marketing engineer for Siemens Digital Industries Software.
Additional content from Siemens Digital Industries Software:
- The Printed Circuit Assembler's Guide to ...Smart Data: Using Data to Improve Manufacturing?(a free eBook available for download)
- The Printed Circuit Assembler's Guide to… Advanced Manufacturing in the Digital Age? (a free eBook available for download)
- Siemens’ free, 12-part, on-demand webinar series?“Implementing Digital Twin Best Practices From Design Through Manufacturing.”
- Real Time With ...?Siemens and Computrol: Achieving Operational Excellence in Electronics Manufacturing
More Columns from Lean Digital Thread
Lean Digital Thread: The Manufacturing Metaverse RevisitedLean Digital Thread: The Secure Digital Thread
Lean Digital Thread: The Manufacturing Metaverse
Lean Digital Thread: Closing the Loop on Manufacturing
Lean Digital Thread: Streamlining the Internal Supply Chain
Lean Digital Thread: Achieving Supply Chain Resilience
Lean Digital Thread: (Pro)curing the Supply Chain Virus
Lean Digital Thread: Why is Everyone Suddenly Interested in Supply Chain?