-
- News
- Books
Featured Books
- pcb007 Magazine
Latest Issues
Current IssueInventing the Future with SEL
Two years after launching its state-of-the-art PCB facility, SEL shares lessons in vision, execution, and innovation, plus insights from industry icons and technology leaders shaping the future of PCB fabrication.
Sales: From Pitch to PO
From the first cold call to finally receiving that first purchase order, the July PCB007 Magazine breaks down some critical parts of the sales stack. To up your sales game, read on!
The Hole Truth: Via Integrity in an HDI World
From the drilled hole to registration across multiple sequential lamination cycles, to the quality of your copper plating, via reliability in an HDI world is becoming an ever-greater challenge. This month we look at “The Hole Truth,” from creating the “perfect” via to how you can assure via quality and reliability, the first time, every time.
- Articles
- Columns
- Links
- Media kit
||| MENU - pcb007 Magazine
Estimated reading time: 5 minutes
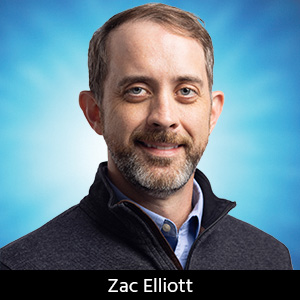
Lean Digital Thread: Streamlining the Internal Supply Chain
In response to labor shortages exacerbated by the global pandemic, many manufacturers are leveraging digitalization and automation to reduce labor needs and improve productivity in the factory. This is not exactly a new trend, as many manufacturers have used Enterprise Resource Planning (ERP) systems and automated production lines to drive their manufacturing operations for many years. However, as new processes are automated and existing automated lines are connected to the full factory, there are many pitfalls to avoid and challenges to overcome. This article reviews the typical digitalization and automation opportunities and describes how to streamline the internal supply chain and realize the full return on investment of an ERP system.
ERP: The Alpha and Omega
For many manufacturers, ERP systems are the most important piece of digitalization in their business. Most business processes begin and end in the ERP system which is responsible for taking customer orders, planning the availability of materials and resources in the factory, releasing and tracking the production of the finished goods, and distributing products to the customer.
By their very nature, ERP systems are complex and costly to implement and maintain. Unless the system is specialized for the particular manufacturing process, additional configuration and customization are needed to model the specific manufacturer requirements. Due to the complexity, in most cases only high-level business processes are automated. Typically, these are “front office” processes: Taking customer orders, planning requirements, shipping goods, taking payments, and so on. Many times, the detailed steps executed on the shop floor are managed externally to the ERP system, creating a disconnect between the ideal view of the ERP system and the very real chaos that can ensue on the shop floor.
One simple example is the raw material inventory database of the ERP system. Without accurate feedback from the shop floor about the usage and spoilage of inventory, gaps increasingly appear between MRP stock levels and actual physical usable materials. However, the ERP system is designed to make corrections when data is available. An intra-plant logistics solution that connects directly to the equipment on the floor and synchronizes the ERP system with the actual consumption of materials occurring in production enables the ERP to work as expected. With real-time shop floor data, it can order materials to replace losses and avoid unnecessary internal shortages and unplanned downtime due to missing materials.
MES: The Rest of the Alphabet
With the ERP managing the front-end business processes, the details of managing the production processes are typically orchestrated by the Manufacturing Execution System (MES). The MES tracks an individual product or production order through its detailed routing to ensure that all manufacturing processes are performed within the product specification, including materials, resources, recipes, and more.
As products become more complex, sophisticated controls are often needed to manage the raw materials used in production. Materials may have special storage considerations or unique handling requirements when on the shop floor, such as moisture-sensitive devices for electronics components. These components have a specific floor lifetime when exposed to the ambient moisture in the air and additional controls that define the drying process to remove moisture from overexposed materials. Using materials that have expired exposes the manufacturer to product quality issues, and poor management of the materials can lead to reduced productivity as materials are not ready when the production line is scheduled to run.
An intra-plant logistics solution can coordinate with the MES to ensure that all material requirements are satisfied and controlled. This applies to two key processes: planning/scheduling and execution.
- For planning and scheduling, the intra-plant logistics solution can provide visibility regarding the availability of materials. This ensures that orders are not dispatched if they cannot be completed due to material handling concerns, avoiding downtime on the line, and improving production efficiency.
- For execution, the intra-plant logistics solution ensures that quality products are built by coordinating the specific and unique material requirements with the MES system and preventing the use of any compromised materials.
Automation: Tying It All Together
With the front and back-end of the manufacturing processes digitized in the ERP and MES systems, the work of producing the product is driven through several stages of automated manufacturing lines. The current trend is to decouple long, specialized manufacturing lines into smaller, flexible work cells that can handle many different product configurations. Automated vehicles and warehouse control systems transfer raw materials to the manufacturing cells and store work-in-progress (WIP) products between each process. The goal is to enable a flexible, self-organizing manufacturing flow, but the reality is that there needs to be an unprecedented level of coordination between each system and each robot to avoid starved lines and excess WIP buildup.
An intra-plant logistics solution is key to realizing a lean manufacturing flow. By connecting the ERP, MES, and automation, an intra-plant logistics solution can take the high-level requirements of the ERP system, coordinate the individual tasks executed on the shop floor by MES, and dispatch the required automation. Raw materials can then flow from the warehouse to the manufacturing cell for just-in-time fulfillment on the line, and WIP is transferred from work cell to intermediate storage to work cell as needed.
Conclusion
For modern manufacturers, an intra-plant logistics solution is necessary for a lean internal supply chain.
Zac Elliott is technical marketing engineer for Siemens Digital Industries Software.
Check out this additional content from Siemens Digital Industries Software:?
- The Printed Circuit Designer’s Guide to... Stackups: The Design within the Design by Bill Hargin (a free eBook available for download)
- The Printed Circuit Assembler's Guide to... Smart Data: Using Data to Improve Manufacturing?by Sagi Reuven and Zac Elliott (a free eBook available for download)?
- The Printed Circuit Assembler's Guide to… Advanced Manufacturing in the Digital Age? by Oren Manor (a free eBook available for download)?
- The Printed Circuit Designer’s Guide to… Power Integrity by Example by Fadi Deek (a free eBook available for download)
- Siemens’ free, 12-part, on-demand webinar series?“Implementing Digital Twin Best Practices?From?Design Through Manufacturing.”?
- Real Time?with...?Siemens and Computrol: Achieving Operational Excellence in Electronics Manufacturing?
- You can also view other titles in our full I-007eBook library here
More Columns from Lean Digital Thread
Lean Digital Thread: The Manufacturing Metaverse RevisitedLean Digital Thread: The Secure Digital Thread
Lean Digital Thread: The Manufacturing Metaverse
Lean Digital Thread: Closing the Loop on Manufacturing
Lean Digital Thread: Keeping an Eye on Quality
Lean Digital Thread: Achieving Supply Chain Resilience
Lean Digital Thread: (Pro)curing the Supply Chain Virus
Lean Digital Thread: Why is Everyone Suddenly Interested in Supply Chain?