-
- News
- Books
Featured Books
- smt007 Magazine
Latest Issues
Current IssueSupply Chain Strategies
A successful brand is built on strong customer relationships—anchored by a well-orchestrated supply chain at its core. This month, we look at how managing your supply chain directly influences customer perception.
What's Your Sweet Spot?
Are you in a niche that’s growing or shrinking? Is it time to reassess and refocus? We spotlight companies thriving by redefining or reinforcing their niche. What are their insights?
Moving Forward With Confidence
In this issue, we focus on sales and quoting, workforce training, new IPC leadership in the U.S. and Canada, the effects of tariffs, CFX standards, and much more—all designed to provide perspective as you move through the cloud bank of today's shifting economic market.
- Articles
- Columns
- Links
- Media kit
||| MENU - smt007 Magazine
Estimated reading time: 6 minutes
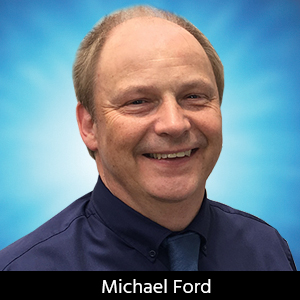
Smart Factory Insights: Trust in Time
We’ve all heard of “just in time” as applied to the supply chain, but with ongoing disruption due to COVID-19, increasing risk motivates us to return to the bad habit of hoarding excess inventory. Based on the public’s initial response to COVID-19—namely hoarding toilet paper—we can only imagine what is filling our manufacturing warehouses right now. Such practices usually just make matters worse. Knowing is everything, yet what we see in ERP in terms of material quantities cannot be trusted. If you fundamentally cannot trust that you have all materials available when you need them, manufacturing will fail. This is happening right now.
Trust in Time
This is simply the knowledge that you physically have, or will have, all of the required materials available to complete an intended production job at the planned time. Don’t bother Googling this phrase; you are hearing it here for the first time. Trust, in this case, is based on knowledge and control. Knowledge includes information about exactly what materials are on site, in what quantities, the supply forms, locations, as well as full accountability of actual consumption, spoilage, and any other dispersion. Control extends through warehouse storage, logistics, as well as the management of part-used materials that are on a carrier, such as on a reel, in a box or carton, etc. The difficulty is that during manufacturing, all of these aspects of knowledge and control are fluid, changing several times every second as materials are allocated, moved, and used. Keeping track manually or by ERP has, in the past, proven to be nearly impossible and certainly impractical.
The Stock Check
Symptoms of the lack of trust in material inventory are easily and commonly found. The periodic stock check entails going through the whole factory and warehouses, counting up the quantities of physical materials. This process can take a couple of days, even with a massive focus of manpower. The factory will be stopped for most of this time to enable an "un-fluid" snapshot to be taken, which costs the operation around 1% in annual lost productivity each time the stock check is performed. The result is usually much more painful, as significant discrepancies between the physical stock, and what ERP has as inventory levels, are revealed and have to be financially written off. In medium-sized electronics manufacturing sites, around $1 million in write-offs of “lost” materials per year, is not unheard of. In terms of cost savings, in this aspect of material management alone there is a great deal of potential justification for a solution that can eliminate these discrepancies.
Where Did It All Go Wrong?
Immediate culprits are easy to identify. In the electronics sector, and in common with other areas of automation, SMT machines throw away materials during their operation that they cannot pick up and recognize in exactly the way they need. The setup of feeders and variations in material dimensions can have quite an effect on the rate of this form of spoilage. A feeder set to the incorrect pitch can create 50% spoilage without anyone noticing until later, when an unexpected internal material shortage happens because materials that ERP identifies as available no longer exist.
Materials are also lost due to repeated handling, especially part-used materials in SMT that need to be put on and taken off from feeders and other carriers. All materials, however, can be lost or damaged whenever they need to be “touched,” including becoming contaminated. In addition, materials become too old to use or obsolete after the relayed product’s end of life.
The symptom of the need to perform a stock check is the occurrence of unexpected material shortages. Having to stop or delay production is bad, but in many cases, it’s not even the worst issue. The immediate response in such cases is the mandate to maintain higher levels of buffer stock, which leads to holding excessive inventory on the balance sheet. ERP will not order materials unless it can see the requirement, so the required buffer levels in the system have to be increased. It is not the fault of ERP that it is mind-numbingly difficult to manually count and update the attrition of every lost part; it just doesn’t get done.
ERP also has additional challenges when the consumption of materials is not registered until the product is completed. Materials may be in the factory, many of which are already on a partially assembled product. If the completion of that product is delayed, perhaps due, ironically, to lack of a material, the problem compounds. The knee-jerk reaction, going back decades, is to bloat the stock levels, even though it is expensive, risky, and not good for the bottom line of the business. In the vast majority of manufacturing operations today, we find bloated inventories, with (hopefully) enough materials to carry the operation from one stock check to the next. And then COVID-19 comes along.
What Do We Do Now?
As humans facing COVID-19, we bought toilet paper, bread, and wine. I’m not sure what the connection is between these items, but what food items should we stock up on? For too long, people in manufacturing have been concerned with the supply of critical materials, forgetting that the absence of any part, no matter how insignificant, will mean the product cannot be completed. As humans, we can go without chickpeas or avocados for a couple of weeks, but in manufacturing, the full set of ingredients in the recipe for each product is always required.
Unexpected material shortages cause havoc, especially mid-way through a production run. Before any production commitment, availability of materials to complete the order must be checked, though with this being a fluid concept, it is not easy unless cages are set up to surround kits of materials that have been created. ERP, the tool purchased to manage this situation that we trust to keep our factory moving, cannot help us because we are in between stock checks, with many unknowns in terms of actual physical inventory quantities.
Software technology in manufacturing has radically advanced recently, specifically related to IIoT data exchange and associated digital MES functionality. This is a clear step up from the capabilities of ERP or incumbent MES systems, though modern IIoT-based MES solutions are designed to directly complement ERP, as well as many aspects of PLM. With production processes linked up as part of the IIoT-based MES platform, every individual component that exists in the factory is accounted for, almost all without the need for human intervention—whether individually identified or supplied in bulk. The IIoT-based MES platform supports decision-making for immediate production changes, safe in the knowledge that the exact materials are definitely available for use without the indulgence of bloated stock levels.
As the physical stock levels are so closely aligned with the system, the stock check process becomes virtual, continuous, without nasty surprises. ERP performs its work more seamlessly, optimizing the incoming supply-chain in terms of cost, risk, and quality. With such technology, we typically see up to a 75% reduction of materials on the shop floor. Short-term schedule changes are handled seamlessly without additional concerns. Warehouse sizes have been known to reduce by a factor of four when all the unnecessary bloated stock is removed.
The overall effect on the bottom line of the business of the “trust in time” Lean supply chain within the factory is seen by many as being the most significant cost saving that can be made. “Trust in time” lean materials is a very simple concept and far simpler to computerize than the push-kit system that it replaces. It is a real differentiator that any operation, regardless of size or location, can utilize today.
This column appears in the August 2020 issue of SMT007 Magazine.
More Columns from Smart Factory Insights
Smart Factory Insights: Making Rework a Smart Business OpportunitySmart Factory Insights: The Sustainability Gold Rush
Smart Factory Insights: Today’s Manufacturing Jobs Require a New Skill Set
Smart Factory Insights: Compose Yourself, Mr. Ford
Smart Factory Insights: The Smart Business Case for Local PCB Manufacturing
Smart Factory Insights: Manufacturing Digital Twin—Spanners in the Works
Smart Factory Insights: Machines, People, and AI
Smart Factory Insights: Is Sustainability in Manufacturing a Benefit or Burden?