-
- News
- Books
Featured Books
- design007 Magazine
Latest Issues
Current IssueAll About That Route
Most designers favor manual routing, but today's interactive autorouters may be changing designers' minds by allowing users more direct control. In this issue, our expert contributors discuss a variety of manual and autorouting strategies.
Creating the Ideal Data Package
Why is it so difficult to create the ideal data package? Many of these simple errors can be alleviated by paying attention to detail—and knowing what issues to look out for. So, this month, our experts weigh in on the best practices for creating the ideal design data package for your design.
Designing Through the Noise
Our experts discuss the constantly evolving world of RF design, including the many tradeoffs, material considerations, and design tips and techniques that designers and design engineers need to know to succeed in this high-frequency realm.
- Articles
- Columns
- Links
- Media kit
||| MENU - design007 Magazine
New Solder Joint Technology From Schmartboard
August 17, 2020 | I-Connect007 Editorial TeamEstimated reading time: 14 minutes
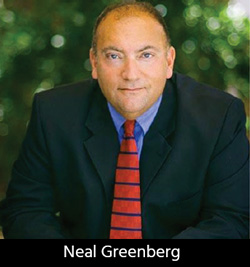
Schmartboard has a surprisingly simple patented process to improve solder joint reliability. Founders Neal Greenberg and Andrew Yaung discuss this process in detail, as well as their hopes of finding a go-to-market partner.
Dan Feinberg: We are joined by the founders of Schmartboard, who have come up with a process that appears to significantly improve reliability. I’m going to let them talk a little bit about Schmartboard first and then about this process. I have to state ahead of time that they are a client of mine, but with all the issues we’ve been talking about at IPC regarding improving reliability for areas such as autonomous transportation, medical devices, military, etc., this is a very interesting and timely topic. Neal, tell our readers about Schmartboard.
Neal Greenberg: We started as an engineering service company designing circuits, doing layouts for companies like Analog Devices, Intel, Texas Instruments, and a lot of smaller companies. In that process, we found a problem. These companies were going through many iterations of prototyping boards. We would start with revision A and go through the alphabet sometimes. We started thinking about how we could improve that from a prototyping standpoint. Back then, if you were going to use an IC from Analog Devices, for example, you’d get a reference board for it from them. This reference board would have the main core and all the bells and whistles—every type of I/O that you could imagine memory—and you would have to dissect it down to what you needed for your development.
That’s what you were doing as an engineer, taking this reference board and dissecting it down. We thought that was kind of silly. Wouldn’t it make more sense if you have the core functionality—what it is that you’re buying—and then have a way to add different things that you need, different I/O, etc.? Our first patent was what we called circuit board building blocks, and they were two-inch by two-inch boards that you take the core technology and then physically connect it to needed I/O. Here’s an SOIC chip—0.5 millimeters in pitch—here’s some kind of an RS232 connector, and here’s some memory. We invented a way to connect these little circuit board blocks together.
Generally, it was well-received. But the problem we found was that people could no longer hand solder these parts onto the boards as they could a few years ago. When the pitch was a 1.27 millimeter, they could do that, but when pitches started getting down to 0.65, 0.5, and 0.4, and they could no longer hand solder it. We asked ourselves, “Is there a way for us to make it where people could now solder these new parts the way they used to with older technology?” We worked for two years and went through many different ideas. We finally came up with the idea of significantly raising the solder mask, letting the parts fall in, and then the solder mask turns into walls in between the legs. It then became much easier to solder—even a 0.4-millimeter pitch IC—and the products quickly went into Fry’s, Digi-Key, and Mouser and Arrow, for example. Today, our products are sold to a “who’s who” of companies.
Andrew Yaung: One of the hardest things for someone to do when hand soldering a surface-mount IC onto a PCB is to position the legs. We brought up the solder mask a little bit higher and ended up achieving two things during the process. One is that the chips then dropped into what we call canals, and second, the solder mask became protective barriers for shorts between each leg. If you were to look at the current product lines that do the prototyping for people with hand soldering, you would see canals—the traces are long so that they can use soldering iron and push the solder through inside that canal. That was done on purpose so that they don’t necessarily have to use outside solder, although if they use outside solder, it’s better for them.
We always thought that someday, eventually, if this technology were to be polished, it could get much better usage. We started talking to folks from the aerospace industry, such as Lockheed Martin NASA. We discovered one of the biggest problems that they have is these joints get broken in a very high-pressure and high-vibration environment. The idea for using this technology is that, if you can imagine, each of those legs sits inside a pocket or a nest. Then, the whole leg will be covered with solder during the solder reflow process. This will make the joint not only stronger but also not crackable anymore. It’s almost like a thorough-hole technology—and perhaps even better than through-hole—because the whole leg or nest is surrounded with solder. The idea that we are taking into the next phase is to have this be used in the volume production environment for reliability purposes.
The other thing that we also discovered was that during the manufacturing process today in high-volume products—because components are becoming smaller and smaller and smaller—when they go through the reflow oven, they have to bring up the temperature as high as possible and then cool it down by blowing air into it. During that process, many tiny components get shifted. That’s why, in a production assembly line, you’ll see a separate station called final inspection for boards. They’re inspecting by eye whether a component gets shifted and which one they have to rework. This technology will also improve that. You can imagine that the component legs will be sitting inside the pocket so that it will not come up. That’s the whole idea behind this. Dr. Ephraim Suhir, a Ph.D. who worked for Bell Laboratory, mathematically proved that this would be 10 times more reliable than the current way of doing things.
Greenberg: This also works for things like QFN and BGA and any of the modern components.
Nolan Johnson: This technology has also evolved out of what you were previously doing with your earlier Schmartboard product.
Greenberg: Exactly.
Yaung: We are taking it one step further, and this in addition to what we’ve been doing.
Greenberg: Now, the truth is we are small and don’t have the resources to bring this from where it is now to where it needs to be as a proven technology that could be used. One of the reasons that we’re working with Dan is to help us get to the point where we find a partner or someone who wants to take this to the next level. We’re looking for someone with that need, and we have an idea of who those types of customers are.
Barry Matties: Do you have companies already interested, and if so, what’s their key motivation?
Greenberg: We are in the process of speaking to people. We’ve had a few who are interested in the need, but we are only beginning to talk about what the technology is and how they’re going to need to be involved in taking this forward.
Matties: With your product, how widely accepted for use do you expect this to be?
Greenberg: Initially, it’s going to be the people that have the critical need. I was watching the SpaceX launch, and that’s a perfect application, as would be any military or automotive technology and critical medical supplies. But like with everything else, cost savings or significant improvements in yields have to happen, which is one of the things that we claim this will do before it’s brought into the mass market for consumer goods.
Matties: How are you validating the data, and what would the timing be for acceptance into space or automotive?
Yaung: As Neal explained earlier, we are a very small company. We have shown that with the current product line for using this technology to do hand soldering, you can count the total complaints with a couple of fingers, and it all came down to the user error. The technology has been very widely accepted in terms of how this is being used. Many people with a technology background or PCB background came back to us and said, “How come I didn’t think of this?” It’s so simple. For taking it to the next step to use it in volume production, one of our criteria is not to alter today’s manufacturing processes because the minute you start altering them, you have to introduce new equipment.
Matties: It’s a roadblock.
Yaung: Yes. As part of the invention process, that is a no-no for us. Where are the areas that need to be fine-tuned in the manufacturing process for this to be used? Number one is the PCB. When you make a PCB today, the solder mask layer is put on before finishing the PCB in the process. If you’re taking a look at the board, the pads where the IC legs sit on is a little bit higher than the mask in today’s technology. Because we reversed that, the way that it changes is the solder mask may have to be put on even earlier, and then the process of taking off the solder mask may have to use a laser to etch out all of the path areas or apply multiple coats. That’s one additional step that needs to be done.
The second step to be looked at is when the PCB is put in the manufacturing process for assembly use, they have to put on solder paste. How do you control the solder paste that goes inside each nest or pocket in these IC legs or joints? If you put too much, it’s going to flow out, and if you put too little, it may not be enough. That has to be a trial and error that required some experiments to perfect the process. When you start dropping the components with the SMT machine, the third phase is we may need to fine-tune the robotic head to make the precision be that much better? There is an opportunity to fine-tune the robotic heads and hardware, as well as software, to make this process a lot more precise so that when it’s dropped into these nests, once the IC goes in, it will perfectly sit inside.
Those are a couple of areas that immediately come to my mind: knowing what the processes look like today, not altering today’s processes, and then how do you fit into those processes? Those may be some of the areas that we have to experiment and work with, and this is where we need a partner who has the resources to make this thing a reality.
Matties: Oftentimes, we see new technologies come along—and there are some great ideas—but without the proper funding or distribution, they fail. There’s a big risk in the mind of the user to even invest in experimenting with this new technology. Not yours, per se, but we’ve seen the history time and time again. It repeats itself.
Yaung: Every new technology or invention has its own risk. We have seen a lot of new technologies go through the process, spend billions of dollars, and never even go anywhere. In our case, the first barrier that we already removed is not to alter today’s manufacturing processes. That’s already a plus. Now, how do you work with the processes to make this thing a reality? A lot of it is trial and error. And to do that, you need the time and resources.
Matties: How many shops are currently using this?
Yaung: We have had five shops, and we purposely experimented in different places: one in Korea, one in the United States—because we invented it in America—two in China, and one in Taiwan, but Taiwan was short-lived. We don’t produce these things in Korea anymore because the cost is high. The two shops in China are making them. Now, with the pandemic, we are thinking about bringing it back to the U.S. I’m having discussions with a couple of shops. They’re very intrigued. They look at this and say, “Wow, but let us think about it. How are we going to do this thing?”
Johnson: To be clear, this is in production in those shops.
Yaung: Yes. They are volume production shops. For one reason or another, these two shops in China are able to do this thing very well. They signed the NDA with us, we tell them exactly what our criteria are, and we are not altering their processes. They go out and do it. As long as they meet our specifications, we’ll be fine, and they came back with it.
Matties: You said the shop in Taiwan stopped using it. Why did they stop?
Yaung: We stopped using them because they were having trouble making the height of the solder mask even close. We were very forgiving in terms of meeting exact spec, even though we have a specification call-out for it, our tolerances were quite generous, but they were still having a difficult time. They tried it for two or three lots, and there was a 30–40% yield loss.
Greenberg: Right now, we’re talking about our current product line, which is the prototyping product line. I want to make sure that’s clear. We are not talking about the mass production product at this point.
Yaung: If you look inside of our current product, you’ll see canals. Where the IC leg sits, the trace is pretty long out there, and the purpose for that was for manual hand soldering with a soldering iron. You push the solder in the canal toward the legs to adhere to it, but the volume production one that we are talking about, or that we are taking it to, is not bad. It’s just a pocket. The pocket is as long as the chip leg will sit.
Feinberg: At I-Connect007, we’re following a lot of the advances in 3D additive manufacturing, and there have been some very significant advantages over the last three to four years. In fact, Barry and I were the initial ones to cover it about five years ago at CES. One of my thoughts is that the geometry that meets with the patent and meets with what gives the higher level of reliability depends on the solder mask, but that geometry can be created by 3D additive printing.
This is a process that may very well be applicable to 3D additive printing—especially since with 3D additive manufacturing, we’re now getting to the point where we can 3D print the dielectric, conductors, solder mask, another dielectric, resistors, and capacitors, but not the chips. The chips are going to be very small. One of the issues is making sure that they have a reliable solder joint because these things are being produced not in two-dimensional circuit boards—height and width; there’s some thickness, but they’re creating the circuit on the outside of a pipe, etc. That’s something else that is an opportunity to be discussed with some of these companies.
Greenberg: Absolutely.
Yaung: It’s like any invention. You think of something, and you invent it along that line, and all of a sudden, someone else finds it useful in their applications that you never even considered.
Matties: That’s how these things evolve. This looks great. I appreciate you sharing what you’re doing. What are the critical next steps?
Greenberg: We want to find the right partner where this is a huge need for them, they have resources, and they’re going to work with us. Then, we’re going to figure out all the details and all the definitions of how this is to be done.
Matties: Is the future of this technique predicated on a partnership, or is this something that you can carry forward without a partner?
Greenberg: It’s going to be predicated on finding the right partner. Our focus now is exclusively partnership and testing.
Matties: Hopefully, this will help. When it comes to rethinking manufacturing, you’re definitely an example. As the industry or the world rethinks manufacturing, they have to think in terms of seeking out and examining new processes because it’s so easy to get trapped in what we know.
Greenberg: We are responding to the issues created by advances in technology or things that are beyond everyone’s control. This is kind of in response to RoHS never truly being resolved. Component miniaturization continues, but it’s never been resolved. Everything has been a bandaid, and what we have to offer is the solution that’s better than a bandaid.
Johnson: Thank you, gentlemen, and good luck to you.
Yaung: Thank you.
Suggested Items
Driving Innovation: Direct Imaging vs. Conventional Exposure
07/01/2025 | Simon Khesin -- Column: Driving InnovationMy first camera used Kodak film. I even experimented with developing photos in the bathroom, though I usually dropped the film off at a Kodak center and received the prints two weeks later, only to discover that some images were out of focus or poorly framed. Today, every smartphone contains a high-quality camera capable of producing stunning images instantly.
Hands-On Demos Now Available for Apollo Seiko’s EF and AF Selective Soldering Lines
06/30/2025 | Apollo SeikoApollo Seiko, a leading innovator in soldering technology, is excited to spotlight its expanded lineup of EF and AF Series Selective Soldering Systems, now available for live demonstrations in its newly dedicated demo room.
Indium Corporation Expert to Present on Automotive and Industrial Solder Bonding Solutions at Global Electronics Association Workshop
06/26/2025 | IndiumIndium Corporation Principal Engineer, Advanced Materials, Andy Mackie, Ph.D., MSc, will deliver a technical presentation on innovative solder bonding solutions for automotive and industrial applications at the Global Electronics A
Fresh PCB Concepts: Assembly Challenges with Micro Components and Standard Solder Mask Practices
06/26/2025 | Team NCAB -- Column: Fresh PCB ConceptsMicro components have redefined what is possible in PCB design. With package sizes like 01005 and 0201 becoming more common in high-density layouts, designers are now expected to pack more performance into smaller spaces than ever before. While these advancements support miniaturization and functionality, they introduce new assembly challenges, particularly with traditional solder mask and legend application processes.
Knocking Down the Bone Pile: Tin Whisker Mitigation in Aerospace Applications, Part 3
06/25/2025 | Nash Bell -- Column: Knocking Down the Bone PileTin whiskers are slender, hair-like metallic growths that can develop on the surface of tin-plated electronic components. Typically measuring a few micrometers in diameter and growing several millimeters in length, they form through an electrochemical process influenced by environmental factors such as temperature variations, mechanical or compressive stress, and the aging of solder alloys.