-
-
News
News Highlights
- Books
Featured Books
- design007 Magazine
Latest Issues
Current IssueAll About That Route
Most designers favor manual routing, but today's interactive autorouters may be changing designers' minds by allowing users more direct control. In this issue, our expert contributors discuss a variety of manual and autorouting strategies.
Creating the Ideal Data Package
Why is it so difficult to create the ideal data package? Many of these simple errors can be alleviated by paying attention to detail—and knowing what issues to look out for. So, this month, our experts weigh in on the best practices for creating the ideal design data package for your design.
Designing Through the Noise
Our experts discuss the constantly evolving world of RF design, including the many tradeoffs, material considerations, and design tips and techniques that designers and design engineers need to know to succeed in this high-frequency realm.
- Articles
- Columns
- Links
- Media kit
||| MENU - design007 Magazine
Estimated reading time: 7 minutes
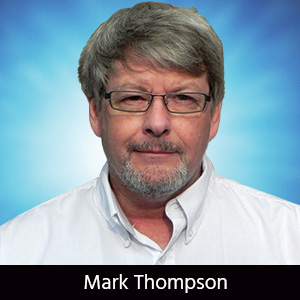
The Bare (Board) Truth: 5 Questions About Improving Thermal Management
In this column, I will focus on answering five questions about thermal management at the design and PCB levels. These questions were sent to me from one of the owners at Monsoon Solutions, where I now work. Jeff Reinhold, EE and designer, asked:
- When I get a datasheet that calls out some area of copper for heat dissipation, how do I translate that requirement to fit my board that may or may not have the specified area available?
- How much heat does a via dissipate, and how does size and fill change that?
- Does moving heat to internal layers help at all or even work?
- How do I identify potential thermal issues?
- How do I translate a heat dissipation requirement, in whatever form it is given, into parameters I can use to design a solution?
Some of the questions I can answer from my “previous life” in PCB fabrication, but for others, I asked my co-workers for their comments.
Question #1
Regarding the first question, Kevin Carrington, a design engineer at Monsoon, said:
Thermal management is all about deltas. Heat only moves along a gradient, so if heat isn’t actively being removed, then it’s simply spread, which means your delta-T is diminished. Spreading over a long enough time achieves steady-state, so understanding a use scenario is often important. Putting more copper in the circuit board would have zero impact on thermal management if the board is at a steady-state condition.
The physical size of parts is very important when considering heat dissipation. A great example is the power SO-8 package that many discrete FETs come in nowadays and have largely replaced the DPAK components. Parts in those packages are often rated very similarly for operating parameters, but the DPAK is far superior when it comes to getting heat out because of the size of the thermal tab.
Accounting for the resistance change of metal with temperature can have a big impact on the system. If you ignore copper—like the circuit board, big common-mode chokes, or inductors—you might be cutting a lot of power dissipation and heat out of your analysis. Even if you include them but use room-temperature copper calculations, there can be big differences between analysis and reality. Thermal foam can be a very useful way to get heat to a metal case when a closed system is used (e.g., no fan). It’s critical to have the foam in compression, otherwise, it won’t achieve the desired low thermal resistance.
The ambient temperature is very important, and “ambient” is often not considered properly. Just because the air outside your product is 50°C doesn’t mean inside is 50°C. For most electronics, the actual ambient temperature in which they’re operating is the steady-state temperature inside the enclosure.
Question #2
For the most part, the most effective way of getting the heat out/dissipating heat from one side to the other is to use filled vias.
The best filled-via is a stitching via with solid copper plug matching the CTE of the copper being used on the PCB. The next best solution would be copper epoxy-filled vias. After that, a silver-filled via works okay. Lastly, epoxy fill can get some of the heat out. All work better than a standard stitching via that is unfilled. Air—particularly stagnant air—is a poor thermal conductor, so any material filling the via will lower that thermal pathway’s resistance.
A smaller via filled with solid copper and many such stitching vias in an array would be the best if using vias to dissipate heat. Also, note that many fabricators have a size limitation on the size of filled vias; most say 0.008”–0.020.”
Question #3
Generally, not increasing the copper area via a ground or power plane and even adding higher copper weight internally is not the answer. This approach may be quite beneficial for transient thermal excursions, but for most products, steady-state power dissipation is the concern. Here, I would recommend a basic analysis through rough equations would be of a greater benefit than adding copper layers internally. But, as Kevin said, producing a prototype that can be tested in a thermal chamber would really tell you where you are.
If you are looking to dissipate heat and are considering adding copper, the best layers would be the outer layers with copper pour. This helps EMI but can dissipate heat through the surface. Again, as Kevin said, “There is no magic copper layer that will be the best way to get the heat out.”
Regarding heat in an enclosure, what is the best way to get the heat out when a board is in an enclosure? The first and oldest way is to simply have a fan in the enclosure.Not being able to do that, Kevin mentioned a trick he learned when he was designing for DVRs that cannot have a fan. Another good method is to utilize compressed foam in the enclosure, but why compressed? Common sense would say uncompressed foam is porous. The idea behind the foam is primarily spreading the heat to a chassis or other system component, which can hopefully get the heat out. The compression helps achieve lower thermal resistance, improving the effectiveness of the thermal pathway.
Question #4
A simple operating test in a thermal chamber using a prototype design can help make substantial leaps in understanding product risks, missed aspects of analysis, and correlating calculations.
Question #5
Question #5 is probably the best and toughest question to answer. The short version is to use the aforementioned techniques to identify, mitigate, evaluate, and optimize the thermal operating conditions of your product. Often, this means implementing a somewhat blind first attempt, using the best practices you can within your constraints, and then checking whether the performance is adequate. Drawing upon previous experience is a key part of this, whether that’s the capability of a device, heat sink, or enclosure or understanding the environment in which it operates.
In general, thermal management is something of an iterative process, and explicit technical requirements aren’t available nor knowable. For example, the most common requirement is related to the electronic components on the board not exceeding their rated junction temperatures. How to do that is a combination of the system implementation operating in the field conditions, which usually requires prototyping or simulation to baseline. Knowing that a part will dissipate 3W of power is simply not enough. Once you have an idea of where you’re at, then you can assess opportunities for improvement.
Generally, these optimizations involve:
- Lower the power dissipation of the device (component selection, functional operating load)
- Improve the heat transfer conditions (thermal pathways through PCB, heat sinks, etc.)
- Constrain the operating environment/use case (software-controlled limits, environmental ratings)
Whenever something is a risk, we must mitigate it, and because the nature of thermal management is heavily influenced by environmental conditions, prototyping is key. Even if it’s just a small portion of the system, being able to characterize the limits will enable an understanding of whether simple thermal pathway improvements can succeed or whether drastic architecture changes are required. The latter is quite important to know as soon as possible. Lastly, use thermal vias and heat sinks where possible.
To remove the heat created by power dissipation of the components, and especially the power components, one solution is to improve the vertical heat transfer through the supporting material.
Typically, this is achieved by providing thermal through-contacts, or thermal vias, going through the substrate from the top side to the bottom side. It is typical to use thermal vias beneath the rear contact or mounting surfaces of the components and particularly the power components, and then plate the through-holes through the entire thickness of the material/substrate.
A second remedy for the heat dissipation problem relates to external heat removal. For this, the substrate may be mounted on a metallic cooling body or heat sink, such as a copper plate, which conveys the power dissipation heat to a cooling system. Such a cooling body may be separated from the supporting substrate by an electrical insulating layer, such as an insulating film or foil. After applying the components to the mounting surface of the substrate, the components are electrically connected with contact surfaces or specifically contact pads and the traces.
To achieve this, a solder paste is printed onto the contact surfaces and the top surface of the thermal vias and is then melted in a reflow soldering process to solder-connect the components.
Conclusion
I hope this column has helped to explain just a few ways to stay out of the hot seat. And, as always, I appreciate any feedback. I can be reached at markt@msoon.com.
This column originally appeared in the September 2020 issue of Design007 Magazine.
More Columns from The Bare (Board) Truth
The Bare (Board) Truth: My Top Six Design ChallengesThe Bare (Board) Truth: Via Basics
The Bare (Board) Truth: Teaching the Next Generation—An Overview of Today’s University Courses
The Bare (Board) Truth: Fabrication Starts With Solid Design Practices
Board Negotiations: Design Rules and Tolerances
The Bare (Board) Truth: Eliminate Confusion
The Bare (Board) Truth: Getting on the Same Page—A Data Story
The Bare (Board) Truth: Refining Output Data Packages for Fabricators