-
- News
- Books
Featured Books
- pcb007 Magazine
Latest Issues
Current IssueInventing the Future with SEL
Two years after launching its state-of-the-art PCB facility, SEL shares lessons in vision, execution, and innovation, plus insights from industry icons and technology leaders shaping the future of PCB fabrication.
Sales: From Pitch to PO
From the first cold call to finally receiving that first purchase order, the July PCB007 Magazine breaks down some critical parts of the sales stack. To up your sales game, read on!
The Hole Truth: Via Integrity in an HDI World
From the drilled hole to registration across multiple sequential lamination cycles, to the quality of your copper plating, via reliability in an HDI world is becoming an ever-greater challenge. This month we look at “The Hole Truth,” from creating the “perfect” via to how you can assure via quality and reliability, the first time, every time.
- Articles
- Columns
- Links
- Media kit
||| MENU - pcb007 Magazine
Estimated reading time: 4 minutes
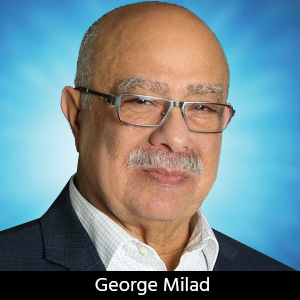
The Plating Forum: Eliminating Waste From Electrolytic Acid Copper Plating
Acid copper plating in most shops is done in vertical plating tanks. Acid copper solutions are not dumped but are continuously used with occasional carbon treatment to remove organic build-up from the additives and from dry film leaching. Anodes used are commonly copper balls in titanium baskets. The copper metal at the anode is continuously oxidized to the copper ion and goes into solution. The copper ion is then reduced to copper metal at the cathode (the panel):
The plating reaction requires vigorous solution movement to maintain the replenishment of copper ions at the plating interface. This is normally done by strong uniform air agitation. Air is a mild oxidant and would help the anodic oxidation and the dissolution of copper.
Over time, the copper content of the electrolytes will continue to rise to the point where it would violate the upper specification limit for copper concentration to meet the throwing power and integrity of the plated copper. When this occurs, the bath is diluted down by a partial dump and remake to reduce the copper concentration. The dumped electrolyte is then waste treated by the use of alkaline precipitation. The copper falls out of solution as copper hydroxide. Then, the precipitate is filtered out using a filter press, bagged, and disposed of by a certified waste disposal company. This is labor-intensive and costly; it also does not help the environment.
The use of air sparging creates an acidic mist that pollutes ambient air in the plating area and is hazardous if not properly removed. This is accomplished by an exhaust system above the tank. Exhaust systems are costly to build and maintain.
The copper balls in the anode baskets will continue to recede as they are dissolved in the electrolyte, which will require replenishment of copper balls on top of each anode basket. This activity is unsafe and usually requires additional dummy plating to film the newly replenished balls. Dummy plating is also required after prolonged inactivity to release any organic additives that get tied up in the anode. Dummy plating is a non-productive activity that is wasteful.
With continuous plating, the anode balls will eventually be reduced in size, particularly at the bottom of the basket. These very small balls would be surrounded by anode sludge, causing the bottom 3–4 inches of the anode basket to become inactive, which has the effect of shortening the total length of the anode. This will have a direct effect on the thickness distribution of the plated copper. The corrective action taken is referred to as “anode maintenance.”
Anode maintenance, depending on the size of the plating line, could take two or three individuals 3–8 hours. The anodes are removed from the electrolyte, the bag is removed and discarded, and the contents of the basket are poured out. The basket is refilled with new balls as well as some of the larger dumped-out balls. This will leave the smaller balls, which are usually sold as scrap. New balls are bought at a premium.
Once the anodes are refilled, they are bagged with new bags. The entire anode maintenance activity is extremely wasteful in labor, scrap copper, and the cost of new bags. The use of insoluble anodes with eductor sparging will eliminate waste in labor and material and will afford a cleaner ambient air environment in the plating area.
Insoluble anodes are made of a titanium mesh that is coated with MMO. MMO is a proprietary, mixed-metal oxide layer. This anode does not require any maintenance and will perform without any dimensional variation day in and day out for months on end. The insoluble anodes must be sized and properly located in the plating tank to give optimum copper thickness uniformity. The anodes should be placed evenly across the anode bar. They should also be 3-4” shorter than the panel and must be tucked 3–4 inches inside the cathode plating window. Insoluble anodes require the continuous addition of copper to the electrolyte; this is accomplished by the controlled addition of copper oxide based on ampere-hours of plating.
The use of bottom eductors to replace air sparging will eliminate all acid mist and the need to exhaust the air above the plating tank. Eductor size and location must be designed to ensure adequate and uniform solution replenishment at the plating site.
With insoluble anodes and eductor sparging, waste in acid copper plating is eliminated as follows:
- No variability in anode dimensions
- No copper waste: every gram of copper added will be plated on the parts
- No anode maintenance or the labor and hazard associated with the activity
- No dummy plating required
- No polluted air requiring exhaust
- No bag replacement
This system with insoluble anodes and eductor sparging is maintenance-free and non-polluting and is presently in use in vertical dip tanks in a couple of large U.S. shops. It is also used extensively in conveyorized acid copper plating equipment.
This column originally appeared in the March 2020 issue of PCB007 Magazine.
More Columns from The Plating Forum
The Plating Forum: Reduction Assisted Immersion Gold for ENEPIG Surface FinishThe Plating Forum: Surface Finish Evolution from Conventional to Advanced
The Plating Forum: Plating in Electronic Applications
The Plating Forum: How the Pandemic Impacted PCB Manufacturing
The Plating Forum: The Significance of IPC ENIG Specification 4552 Revision B
The Plating Forum: The IPC Surface Finish Specifications
The Plating Forum: An Overview of Surface Finishes
The Plating Forum: DIG—The Next Generation